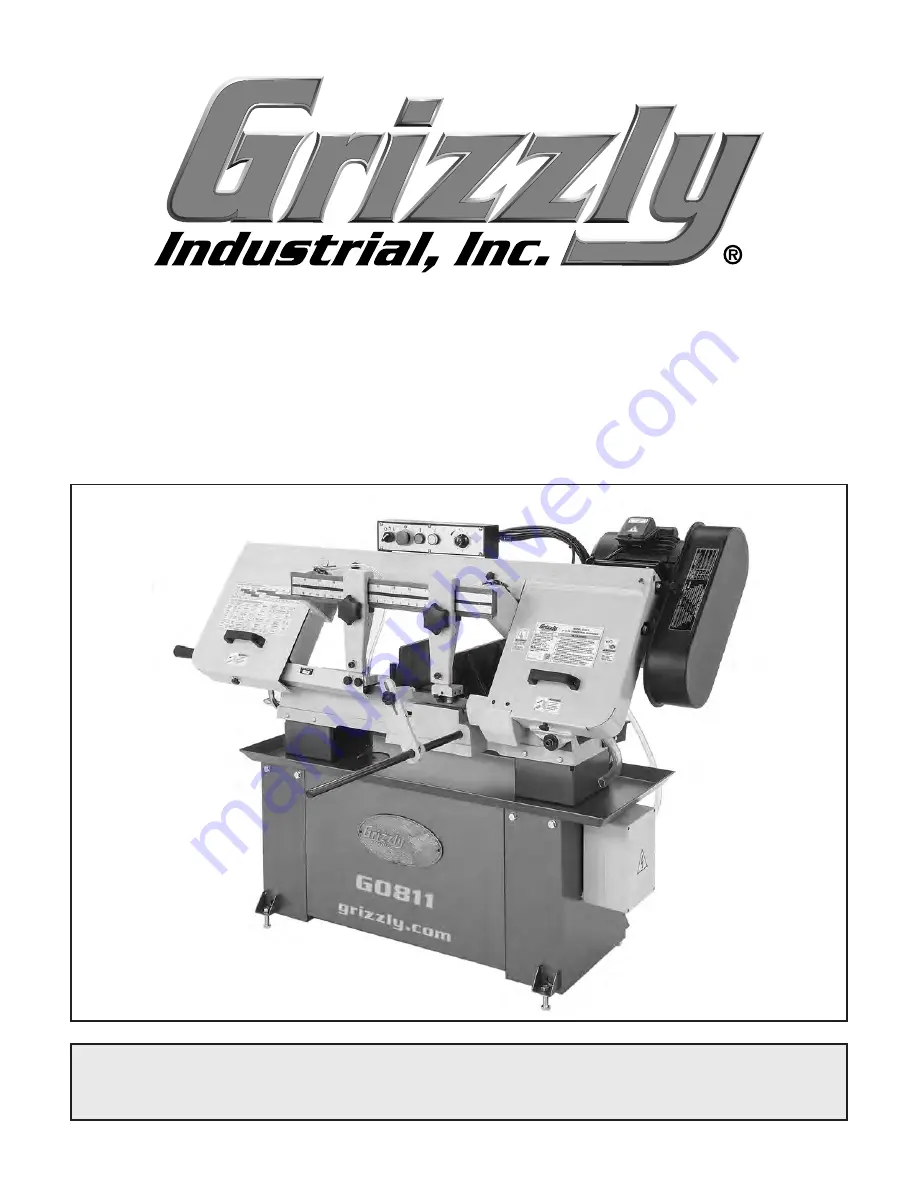
MODEL G0811
9" X 16" METAL-CUTTING BANDSAW
OWNER'S MANUAL
(For models manufactured since 02/16)
COPYRIGHT © NOVEMBER, 2016 BY GRIZZLY INDUSTRIAL, INC.
WARNING: NO PORTION OF THIS MANUAL MAY BE REPRODUCED IN ANY SHAPE
OR FORM WITHOUT THE WRITTEN APPROVAL OF GRIZZLY INDUSTRIAL, INC.
#BL18346 PRINTED IN TAIWAN
V1.02.17
Summary of Contents for G0811
Page 68: ......