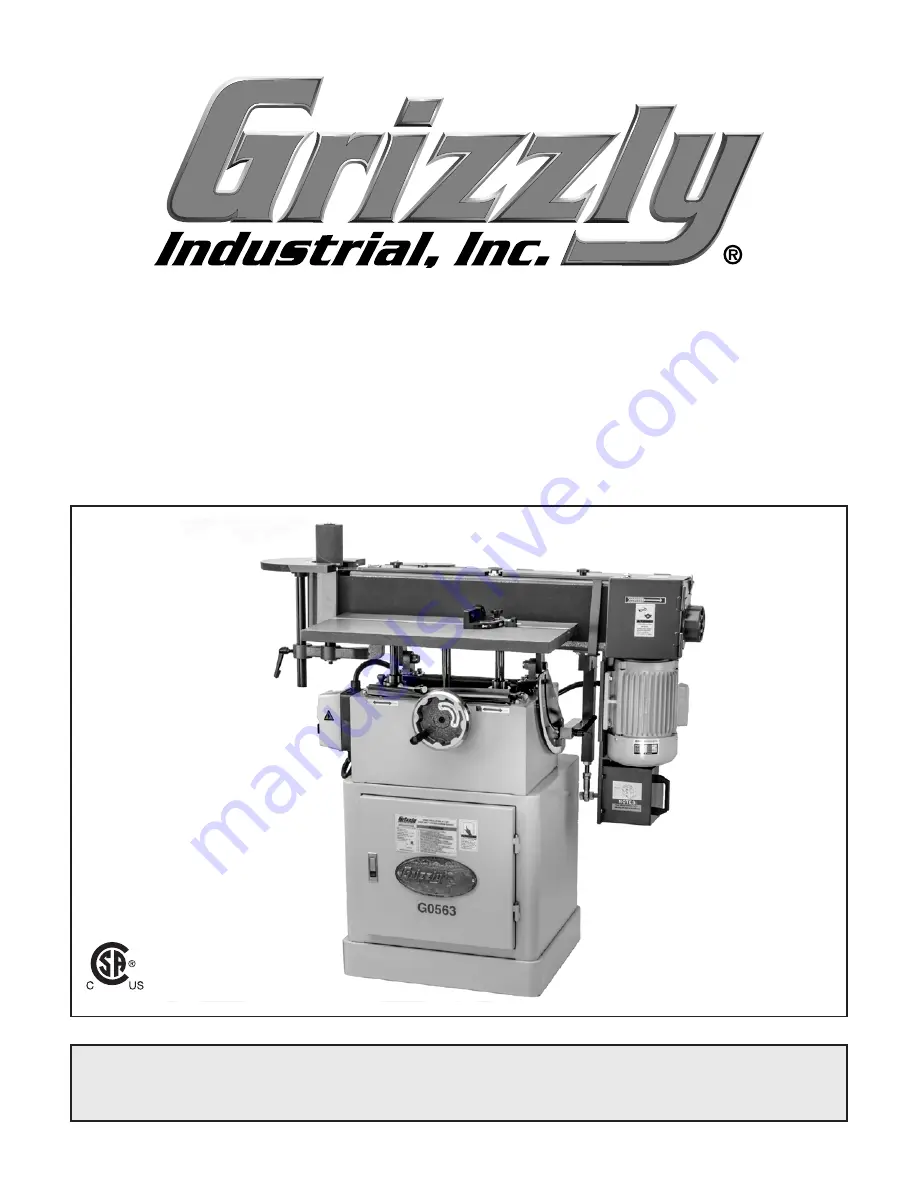
247570
COPYRIGHT © JULY, 2004 BY GRIZZLY INDUSTRIAL, INC., REVISED SEPTEMBER 2014 (WK)
WARNING: NO PORTION OF THIS MANUAL MAY BE REPRODUCED IN ANY SHAPE
OR FORM WITHOUT THE WRITTEN APPROVAL OF GRIZZLY INDUSTRIAL, INC.
#CA6304
PRINTED IN TAIWAN
V2.09.14
MODEL G0563/G0564
OSCILLATING EDGE SANDER
OWNER'S MANUAL
(For models manufactured since 10/11)
Summary of Contents for G0563
Page 19: ...Model G0563 G0564 Mfd Since 10 11 17 Hardware Recognition Chart ...
Page 52: ......