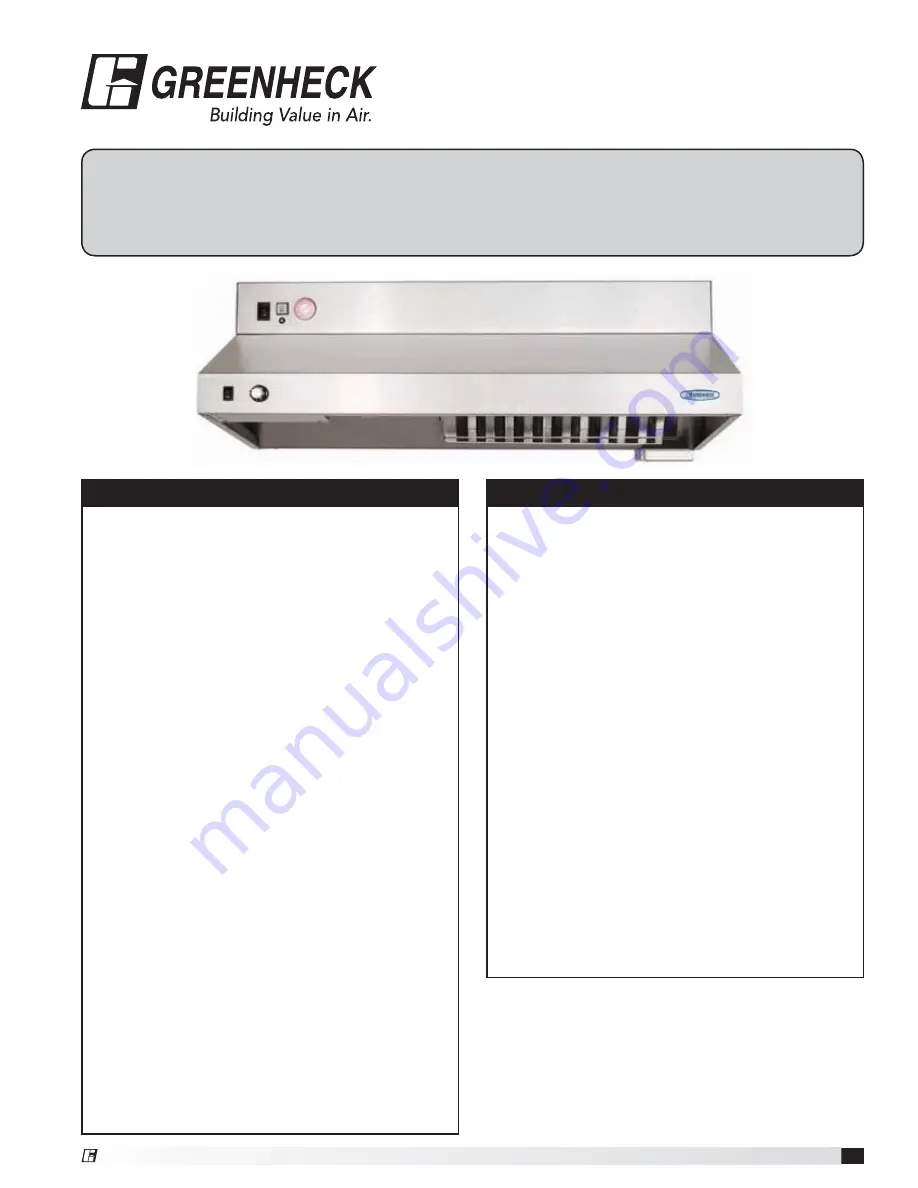
1
Fire Ready Hood
Installation, Operation and Maintenance Manual
Please read and save these instructions for future reference. Read carefully before attempting to assemble, install,
operate or maintain the product described. Protect yourself and others by observing all safety information. Failure
to comply with instructions could result in personal injury and/or property damage!
WARNING
To reduce the risk of fire, electric shock, or injury
to persons, observe the following:
• Use this unit only in the manner intended by the
manufacturer.
• Before servicing or cleaning unit, switch power off
at service panel and lock the service disconnecting
means to prevent power from being switched on
accidentally. When the service disconnecting means
cannot be locked, securely fasten a prominent
warning device, such as a tag, to the service panel.
• Installation work and electrical wiring must be
done by a qualified person(s) in accordance with all
applicable codes and standards, including fire rated
construction codes and standards.
• Sufficient air is needed for proper combustion
and exhausting of gases through the flue
(chimney) of fuel burning equipment to prevent
backdrafting. Follow the heating equipment
manufacturer’s guideline and safety standards such
as those published by the National Fire Protection
Association (NFPA), and the American Society
of Heating, Refrigeration and Air Conditioning
Engineers (ASHRAE), and the local code authorities.
• When cutting or drilling into wall or ceiling, do not
damage electrical wiring and other hidden utilities.
• To reduce the risk of fire or electric shock, do
not use this range hood with an additional speed
control device.
• Ducted fans must always be vented to the
outdoors.
• To reduce the risk of fire, use only metal ductwork.
• Use with approved wiring only.
• This unit must be grounded.
WARNING
To reduce the risk of range top grease fire:
• Never leave surface units unattended at high
settings. Boilovers cause smoking and greasy
spillovers that may ignite. Heat oils slowly on low or
medium settings.
• Always turn hood ON when cooking at high heat or
when cooking flaming foods.
• Clean ventilation fans frequently. Grease should not
be allowed to accumulate on fan or filter.
• Use proper pan size. Always use cookware
appropriate for the size of the surface element.
To reduce the risk of injury to persons in the event
of a range top grease fire, observe the following:*
• SMOTHER FLAMES with a close-fitting lid, cookie
sheet, or metal tray, then turn off the burner. BE
CAREFUL TO PREVENT BURNS. If the flames do
not go out immediately, EVACUATE AND CALL THE
FIRE DEPARTMENT.
• NEVER PICK UP A FLAMING PAN. You may be
burned.
• DO NOT USE WATER, including wet dishcloths or
towels - violent steam explosion will result.
* Based on “Kitchen Fire Safety Tips” published by
NFPA.
®
®
Model GRRS
Fire Ready Hood