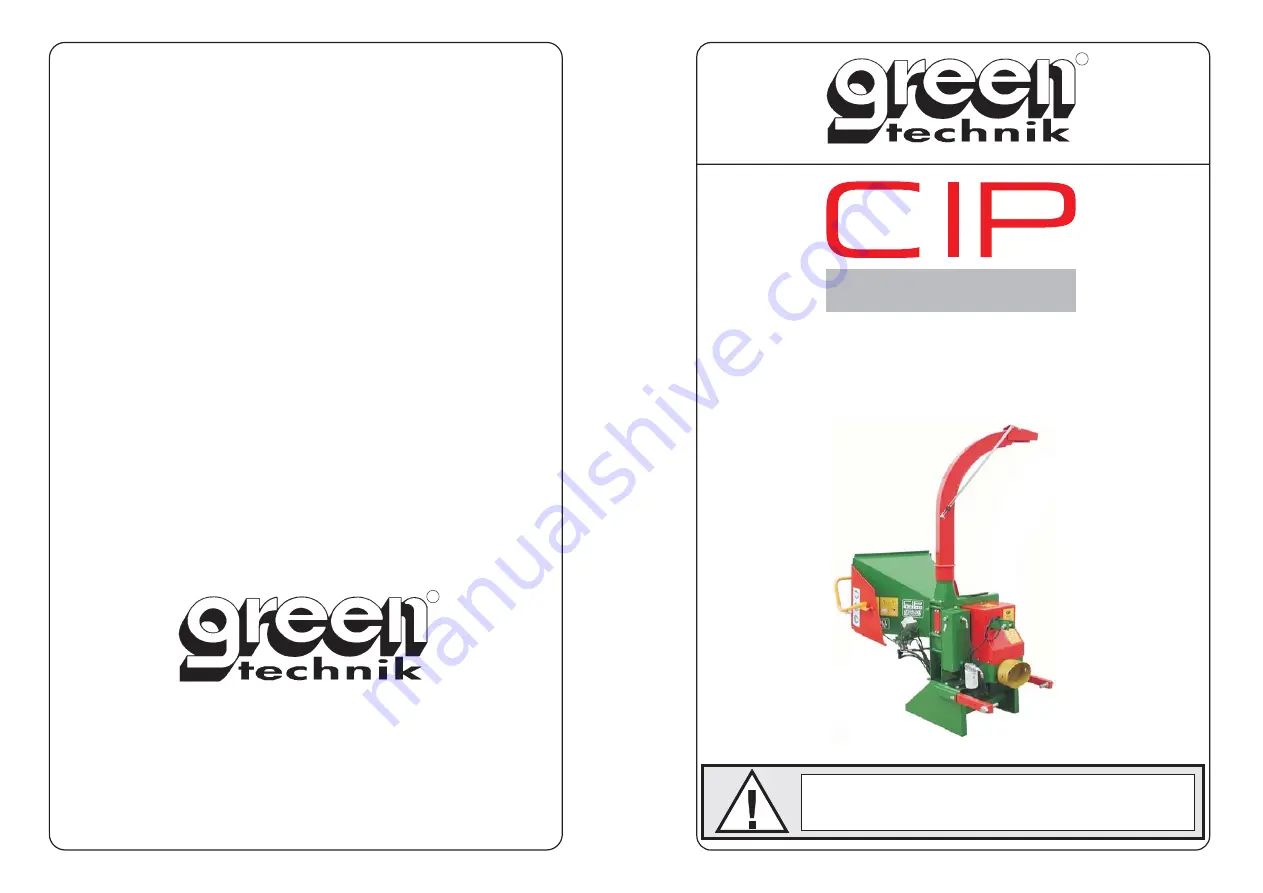
Rev
.01/03
1300
R
www.green-technik.com
By: GREEN-PRODUZIONE s.r.l.
Via Mons. Vigolungo, 2 - 12040 VEZZA D'ALBA -
R
AZIENDA CON SISTEMA QUALITÀ
CERTIFICATO
=
=
UNI EN ISO 9001/2008
PROFESSIONAL
CHIPPER
OPERATION AND
MAINTENANCE HANDBOOK
CAUTION !
Befor using the machine, carefully read this Handbook!