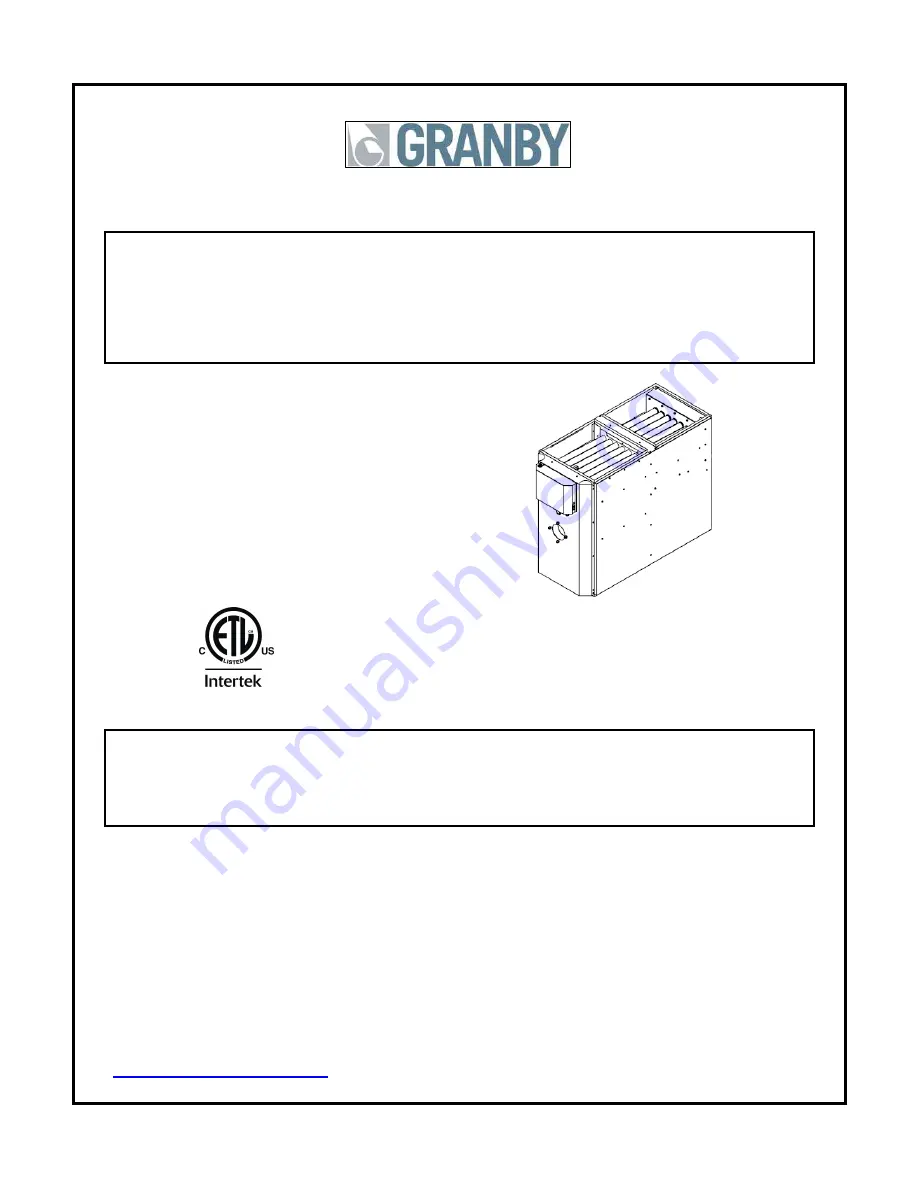
Installation, Operation and
Service Manual
KLC
Condensing Unit
95% + EFFICIENCY
OIL FIRED
LOWBOY FURNACE
Model KLC- 100
CONFORTO CHE
INSTALLATIONS MUST MEET ALL LOCAL AND FEDERAL
CODES THAT MAY DIFFER FROM THIS MANUAL
Please read the manual in its entirety before beginning installation.
This manual must be kept with the furnace for future reference.
GRANBY FURNACES INC.
PO Box 637
12118 Hwy 209
Parrsboro Nova Scotia Canada
B0M 1S0
902-254-2543
www.granbyindustries.com
01-24-2014
G2012-E3 Rev.G