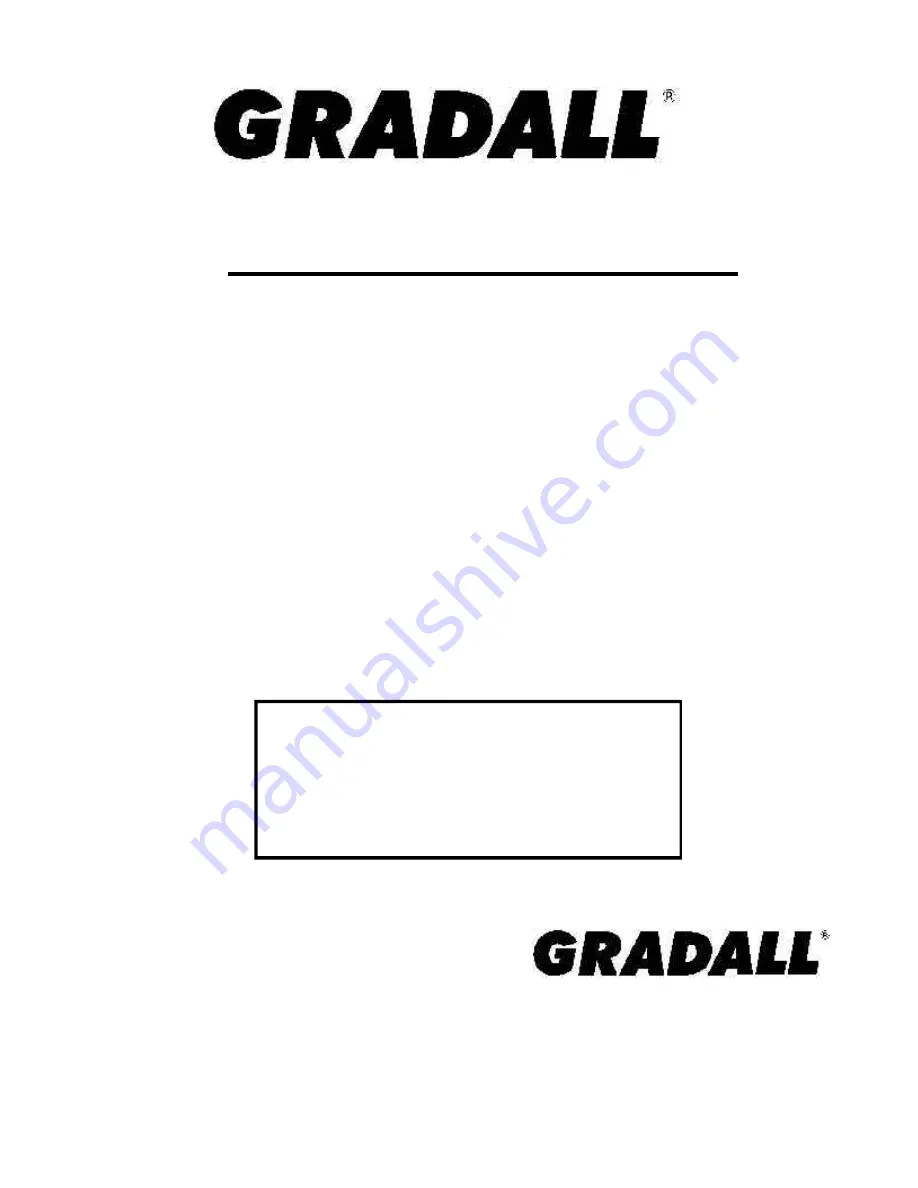
LOED MATERIAL HANDLER
MODEL 534A
Service Manual
PART NO. 9020-5896
®
IMPORTANT
READ AND UNDERSTAND THIS MANUAL
BEFORE STARTING, OPERATING OR
PERFORMING MAINTENANCE PROCEDURES
ON THIS MACHINE.
KEEP THESE MANUAL IN CAB
Gradall is a registered trademark for hudraulic
excavators built by The Gradall Co.
THE
COMPANY
406 MILL AVENUE S.W.
NEW PHILADELPHIA, OHIO 44663
(216) 339-2211
This manual describes the LOED Handler as origionally
designed and built by the LOED Corporation. The LOED
Handler product line was purchased October 15, 1982 by
The Warner & Swasey Co., a subsidiary of The Bendix
Corporation. Descriptions and specifications shown herein
are subject to change without notice.
Содержание LOED 534A
Страница 5: ...MODEL 534 6 000 Capacity 4 FIGURE 1...
Страница 20: ...19 FIGURE 19...
Страница 28: ...CARRIER SUBASSEMBLY FRONT 24 TO 1 REAR 35 TO 1 27 FIGURE 24...
Страница 41: ...SECTION II TROUBLE SHOOTING 41 FIGURE 40...
Страница 44: ...TROUBLESHOOTING GUIDE FOR GEAR TYPE HYDRAULIC PUMPS 44 FIGURE 43...
Страница 55: ...REAR DRIVE MOTOR 55 FIGURE 72...
Страница 56: ...PARTS IDENTIFICATION 56 FIGURE 73...
Страница 74: ...FRONT DRIVE MOTOR before s n 237 74 FIGURE 119...
Страница 75: ...75 FIGURE 120...
Страница 88: ...FIGURE 150 FIGURE 151 88...
Страница 89: ...FIGURE 152 89...
Страница 90: ...FIGURE 151 FIGURE 153 90...
Страница 91: ...FIGURE 154 91...