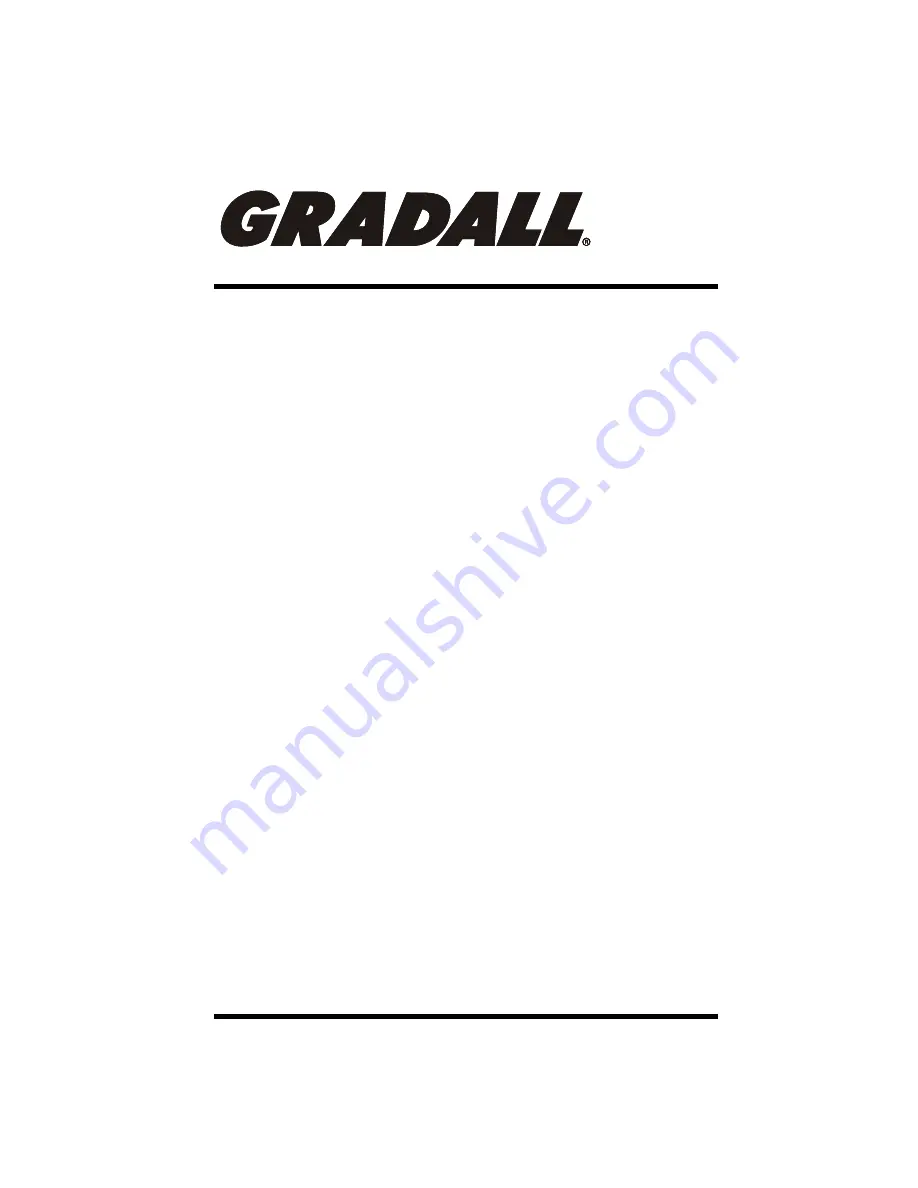
Operator & Safety
Manual
Keep this manual with machine at all times.
D152/D154
S/N D152000001 & After
S/N D154000001 & After
82104002
Revised
February 10th, 2020
This manual, and all manuals for the Gradall Hydraulic
Excavator product line, can be viewed or downloaded, free-of-charge, at
www.mygradall.com
Summary of Contents for D152
Page 6: ...Read This First d 82104002 NOTES...
Page 10: ...Table of Contents iv 82104002...
Page 24: ...Section 1 General Safety Practices 1 14 82104002 NOTES...
Page 39: ...Section 2 Pre Operation and Controls 2 15 82104002 This Page Intentionally Left Blank...
Page 42: ...Section 2 Pre Operation and Controls 2 18 82104002 NOTES...
Page 55: ...Section 3 Operation 3 5 82104002 This Page Intentionally Left Blank...
Page 76: ...Section 3 Operation 3 26 82104002 This Page Intentionally Left Blank...
Page 96: ...Index 2 82104002 Travel Hazard 1 8 U Upperstructure Cab Controls Indica tors 2 8...