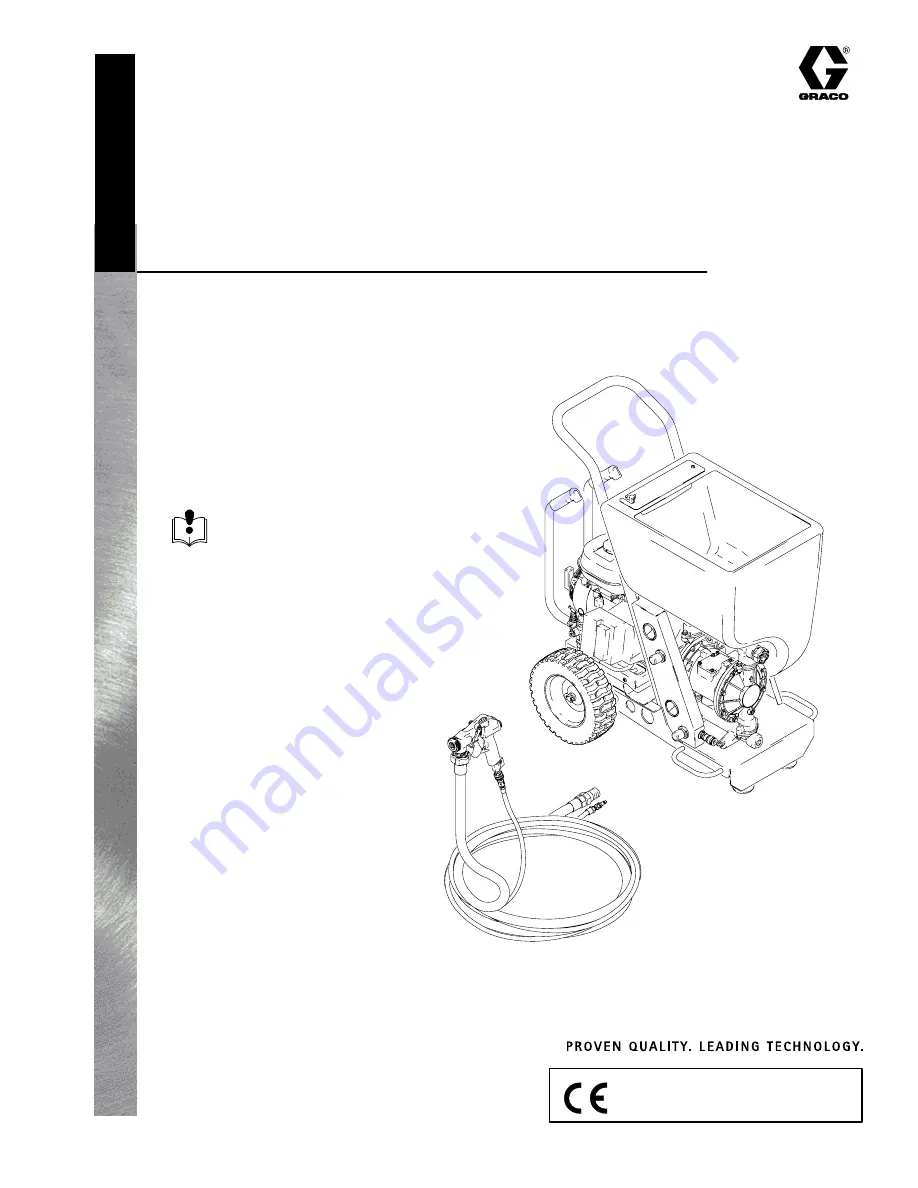
Repair – Parts List
GRACO INC.ąP.O. BOX 1441ąMINNEAPOLIS, MNą55440-1441
Copyright 2003, Graco Inc. is registered to I.S. EN ISO 9001
TexSpray GTX
t
2000
– For Water-Based Materials Only –
Model: 246880
120 psi (8.27 bar) Maximum Working Air Pressure
120 psi (8.27 bar) Maximum Working Fluid Pressure
309916D
Read warnings and instructions.
Related Manuals:
Pump:
308479
Gun:
310616
Operation:
309915 English
ti3785b