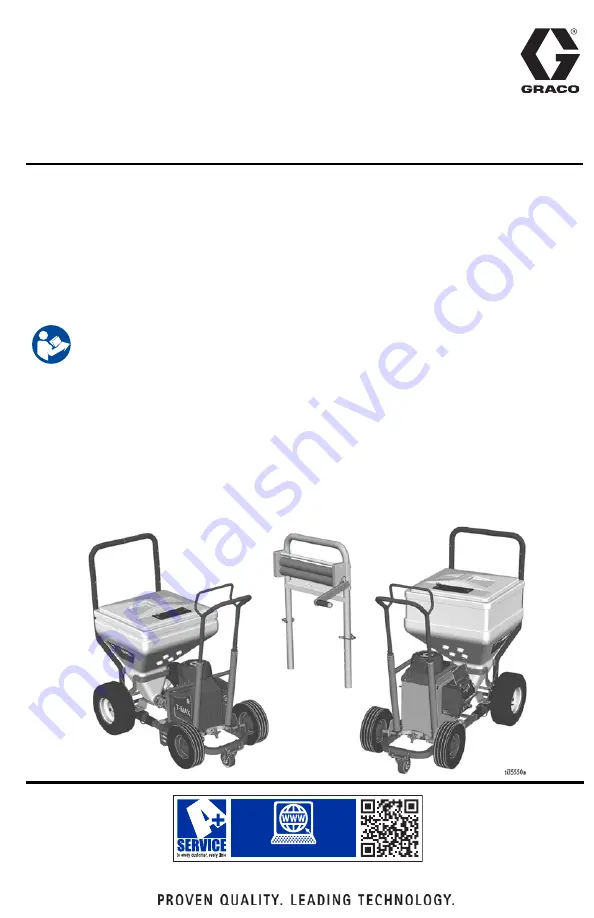
3A6748B
EN
Operation, Repair, Parts
T-Max
™
506/657/6912
Texture Sprayer
For portable spraying of water-based materials. Can be used for application of
solvent-based materials only when solvent compatible seals are installed and
solvent compatible, conductive hoses are used. For professional use only.
Not approved for use in European explosive atmosphere locations.
T-Max 506
: 50 bar (5 MPa, 725 psi) Maximum Working Pressure
T-Max 657
: 65 bar (6.5 MPa, 940 psi) Maximum Working Pressure
T-Max 6912:
69 bar (6.9 MPa, 1000 psi) Maximum Working Pressure
See page 4-6 for model information.
Important Safety Instructions
Read all warnings and instructions in this manual and related manuals before using
the equipment. Be familiar with the controls and the proper usage of the equipment.
Save these instructions.
Related Manuals
STX Trigger Gun
3A6746
Bag Roller Kits
312790, 3A4995
T-Max Remote Switch Kit
3A6784
T-Max Applicator
312879
PrimeValve Accessory Kit
3A6785
Free Flow Applicator
313537
Vibra-Flo T-Max
3A6909
Inline Applicator
309495
Air Manifold Kit
3A6839
www.graco.com/techsupport
??
??
Summary of Contents for T-MAX 506
Page 53: ...Repair 3A6748B 53 6 Install motor cover using four screws 7 Connect pump to hopper ...
Page 63: ...Repair 3A6748B 63 Cross Section Reference Pump Ball Identification 6912 ...
Page 67: ...Notes 3A6748B 67 Notes ...
Page 68: ...Parts Hopper Frame 68 3A6748B Parts Hopper Frame b a ...
Page 70: ...Parts Power Module 506 657 70 3A6748B Parts Power Module 506 657 PAGE 78 PAGES 74 75 ...
Page 72: ...Parts Power Module 6912 72 3A6748B Parts Power Module 6912 PAGE 80 PAGE 76 ...
Page 76: ...Parts Pump 25E668 6912 76 3A6748B Parts Pump 25E668 6912 ...
Page 78: ...Parts Control Box 506 657 78 3A6748B Parts Control Box 506 657 ...
Page 81: ...Wiring Diagrams 3A6748B 81 Wiring Diagrams 506 657 ...
Page 82: ...Wiring Diagrams 82 3A6748B 6912 US ...