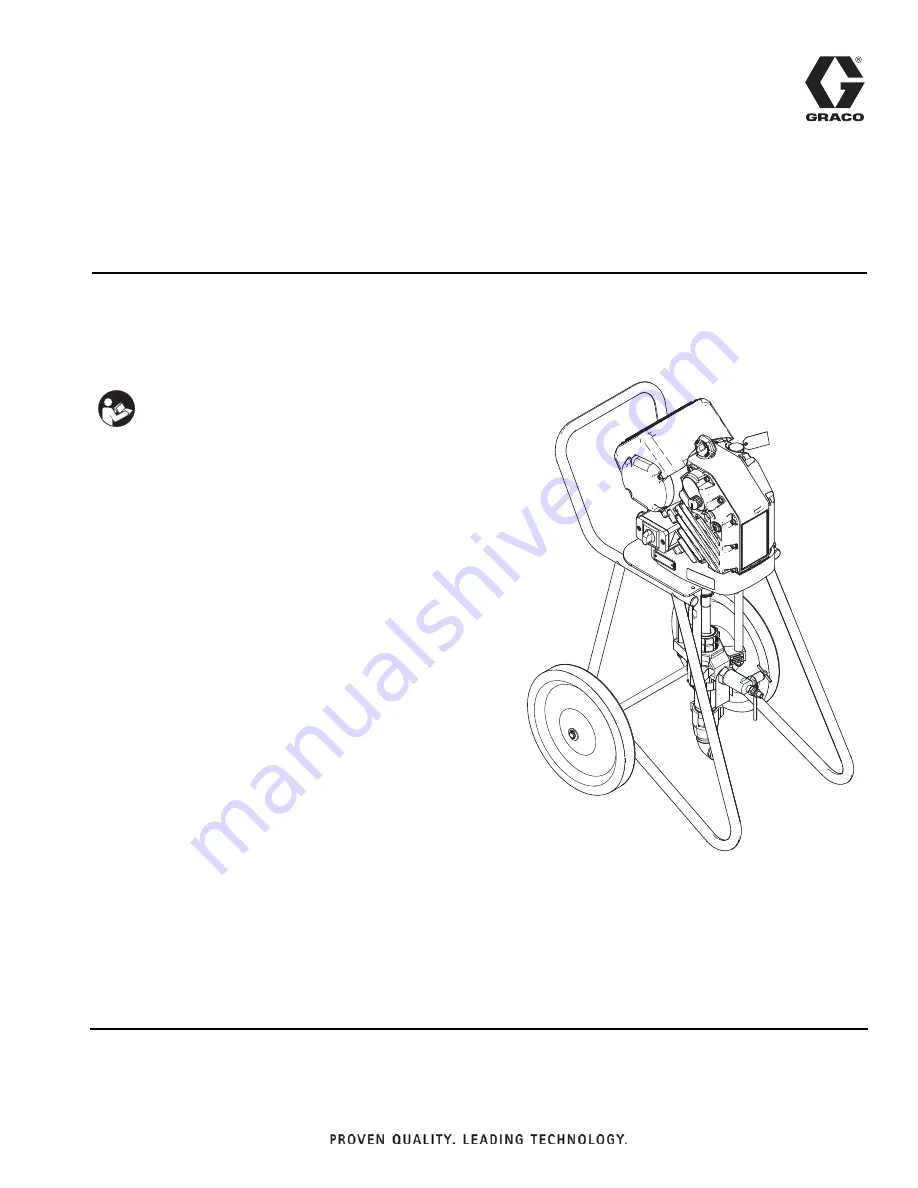
333208F
EN
Operation-Repair-Parts
Electric High Pressure
Airless Sprayer
Electric high pressure sprayer packages for application of protective coatings.
For professional use only.
Not approved for use in explosive atmospheres or hazardous locations.
For
Model Information
and maximum working pressure,
Important Safety Instructions
Read all warnings and instructions in this
manual. Save these instructions.
WLE