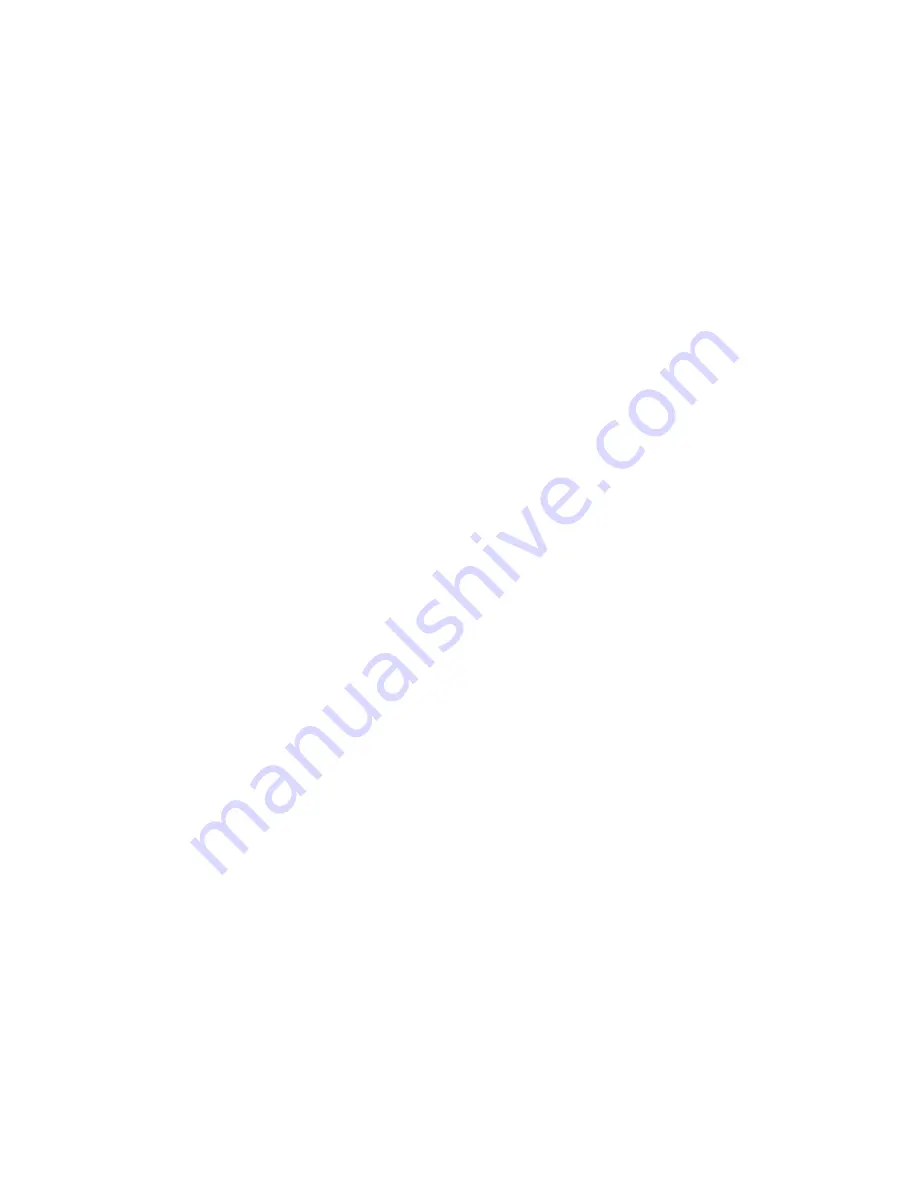
X-7425
1973 GMC Motorhome
Maintenance Manual
Table of Contents
Section Description
0
Information, Periodic Maintenance and Lubrication
1
Body, Heating and Air Conditioning
2 Frame
3A Front
Suspension
3B Drive
Axles
3C Final
Drive
4 Rear
Suspension
5 Brakes
6A Engine
6K Engine
Cooling
6M
Engine Fuel System
6T
Emission Control Systems
6Y Engine
Electrical
7 Transmission
8
Fuel Tank and Exhaust
9 Steering
System
10 Wheels
and
Tires
12 Chassis
Electrical
13
Radiator and Coolant Recovery System
14 Bumpers
24 Miscellaneous
Living Area Facilities
24A
Periodic Maintenance and Lubrication
24B
Living Area Electrical System
24C Motor
Generator
24D Refrigerator
24E
Roof Mounted Air Conditioner (Information not available at time of publication)
24F
LP Gas System
24G Furnace
24H Range/Oven
24J
Living Area Water System
24K Toilet
24L
Holding Tank and Drainage System
24M Thermasan
System
24N
Cabinets and Furniture
24P Exhaust
Vents
24Q
Other Equipment (Vacuum Cleaner)
Wiring
Diagrams