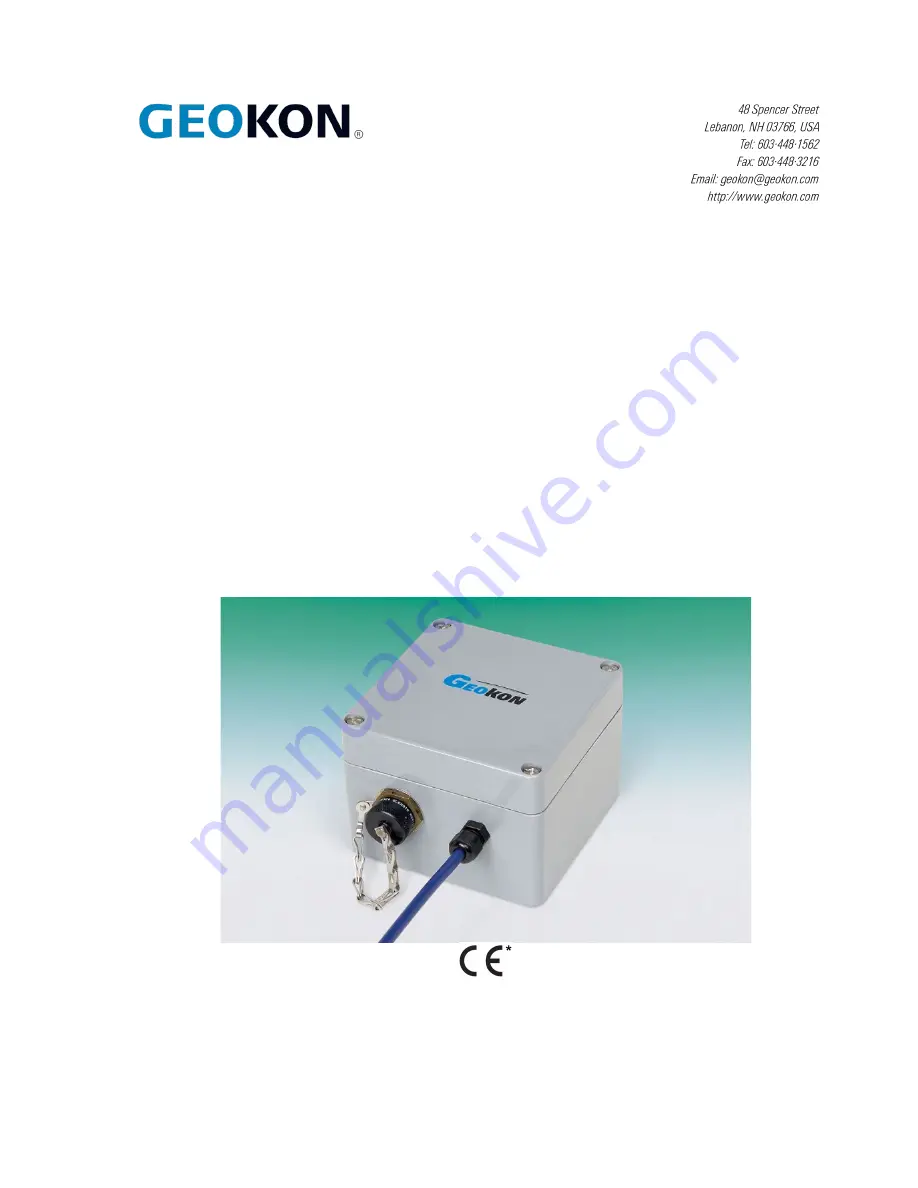
*Waterproof Single-Channel Dataloggers Models 8002-WP-1 and 8002-WP-2 are not CE Approved.
Instruction Manual
Model LC-2
Single Channel Datalogger
No part of this instruction manual may be reproduced, by any means, without the written consent of Geokon
®
.
The information contained herein is believed to be accurate and reliable. However, Geokon
®
assumes no responsibility for
errors, omissions or misinterpretation. The information herein is subject to change without notification.
Copyright © 2007-2019 by Geokon
®
(Doc Rev FF, 02/19/2019)