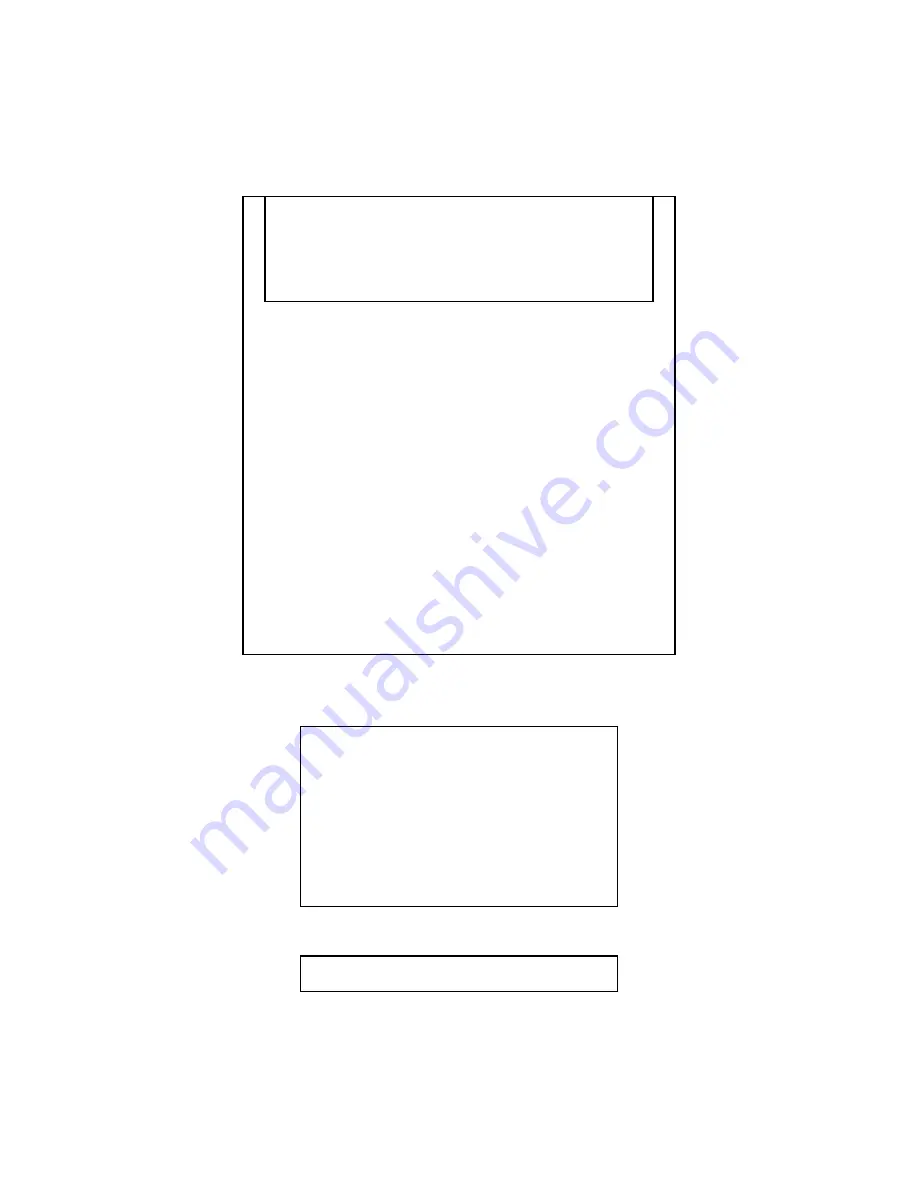
- Do not store or use gasoline or other flammable
vapors and liquids in the vicinity of this or any
other appliance.
- WHAT TO DO IF YOU SMELL GAS:
• Do not try to light any appliance.
• Do not touch any electrical switch; do not use
any phone in your building.
• Immediately call your gas supplier from a
neighbour’s phone. Follow the gas supplier’s
instructions.
• If you cannot reach your gas supplier, call the
fire department.
WARNING:
If the information in this manual
is not followed exactly, a fire or explosion
may result causing property damage, personal
injury or loss of life.
WARNING:
Improper installation,
adjustment, alteration, service or
maintenance can cause injury
or property damage. Read the
installation, operating and maintenance
instructions thoroughly before installing
or servicing this equipment.
WARNING:
For Outdoor Use Only
Summary of Contents for P-5050
Page 4: ......
Page 8: ......
Page 44: ...Gentherm Global Power Technologies 5 12 P 5050 62553 rev 8 ...
Page 46: ...Gentherm Global Power Technologies 6 2 P 5050 62553 rev 8 ...
Page 60: ...Gentherm Global Power Technologies 8 10 P 5050 62553 rev 8 ...
Page 98: ...Gentherm Global Power Technologies 14 4 P 5050 62553 rev 8 ...