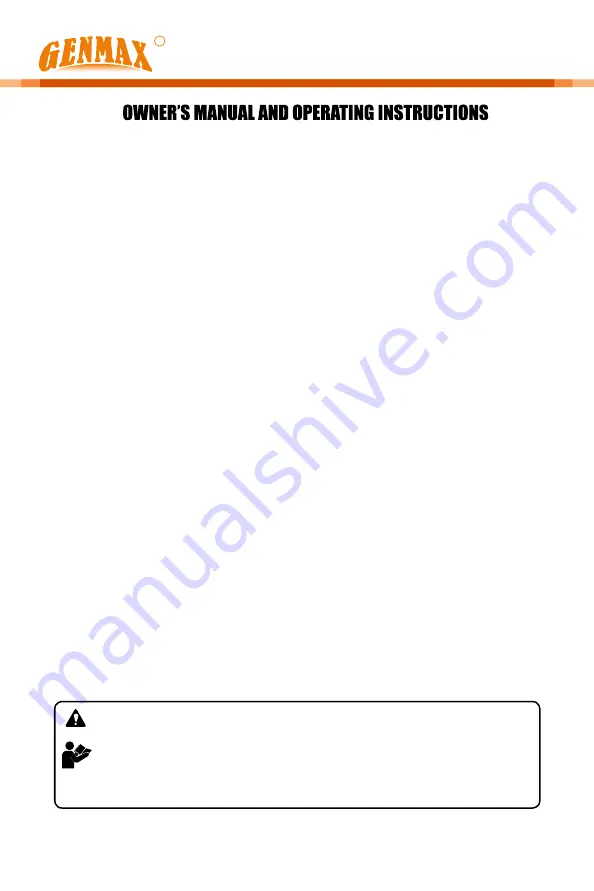
HIGH PRESSURE
WASHER
User manual
WARNING:
SAVE THISMANUAL FOR FUTUREREFERENCE
This manual contains important information regarding safety. Operation,
maintenance
and
storage
of
this
product
.
Before
use
,
read
carefully
and
understand
all
cautions
,
warnings
,
instructions
and
product
labels
.
Failure
to
do
so
could
result
in
serious
personal
injury
and/or
property
damage
.
R
Summary of Contents for GPW2500V-E
Page 36: ...34 6800 W01 GEM 02 01 V2 ...