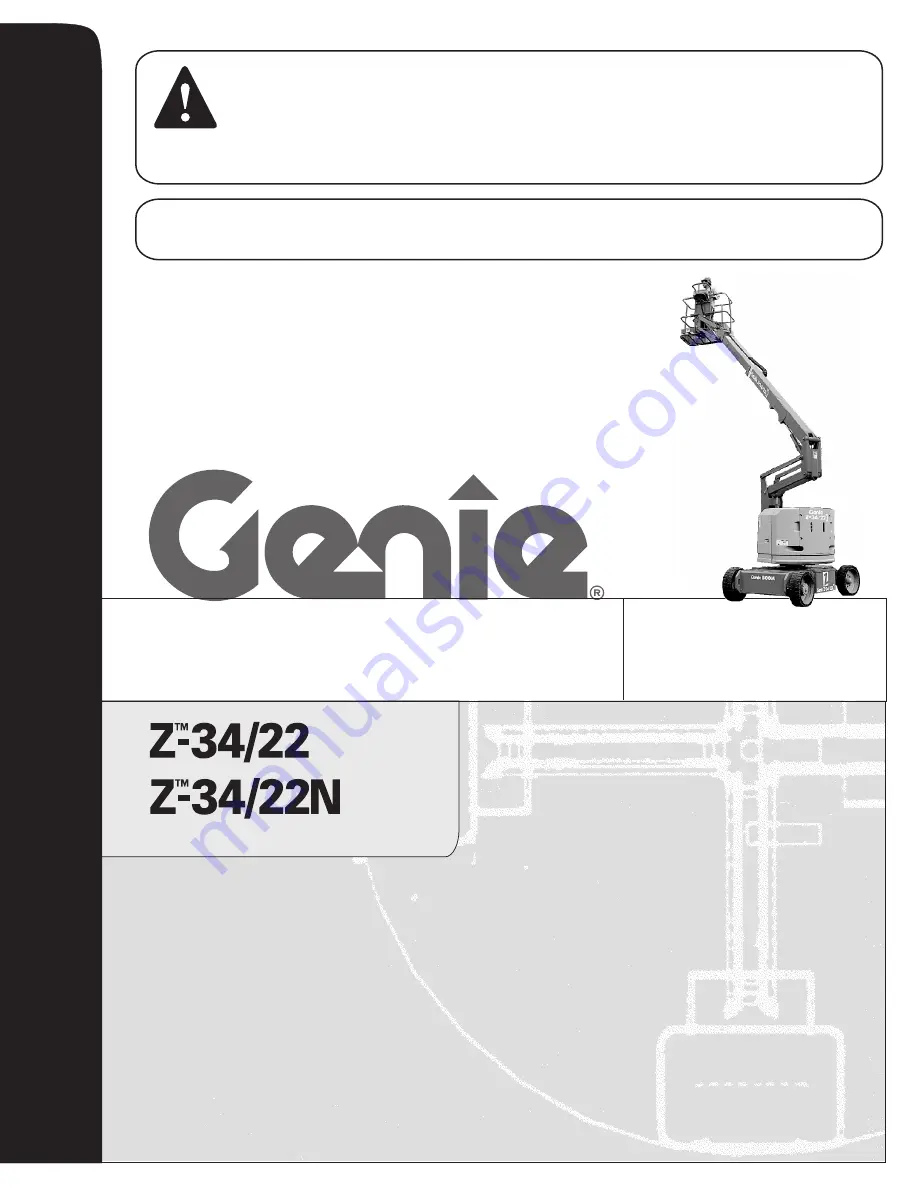
Operator’s Manual
Second Edition
Ninth Printing
Part No. 43654
with Maintenance Information
Before serial number Z34N-2101 and Z34-1735:
Incorrect operation can result from use of this manual on machines that have not been updated
according to Genie Campaign Bulletin 070001. Death or Serious Injury can result.
This manual only applies to machines that have been updated according to Genie Campaign
Bulletin 070001. Contact Genie Industries for information on this bulletin.
After serial number Z34N-2100 and Z-34-1734:
Genie Campaign Bulletin 070001 does not apply to these machines.