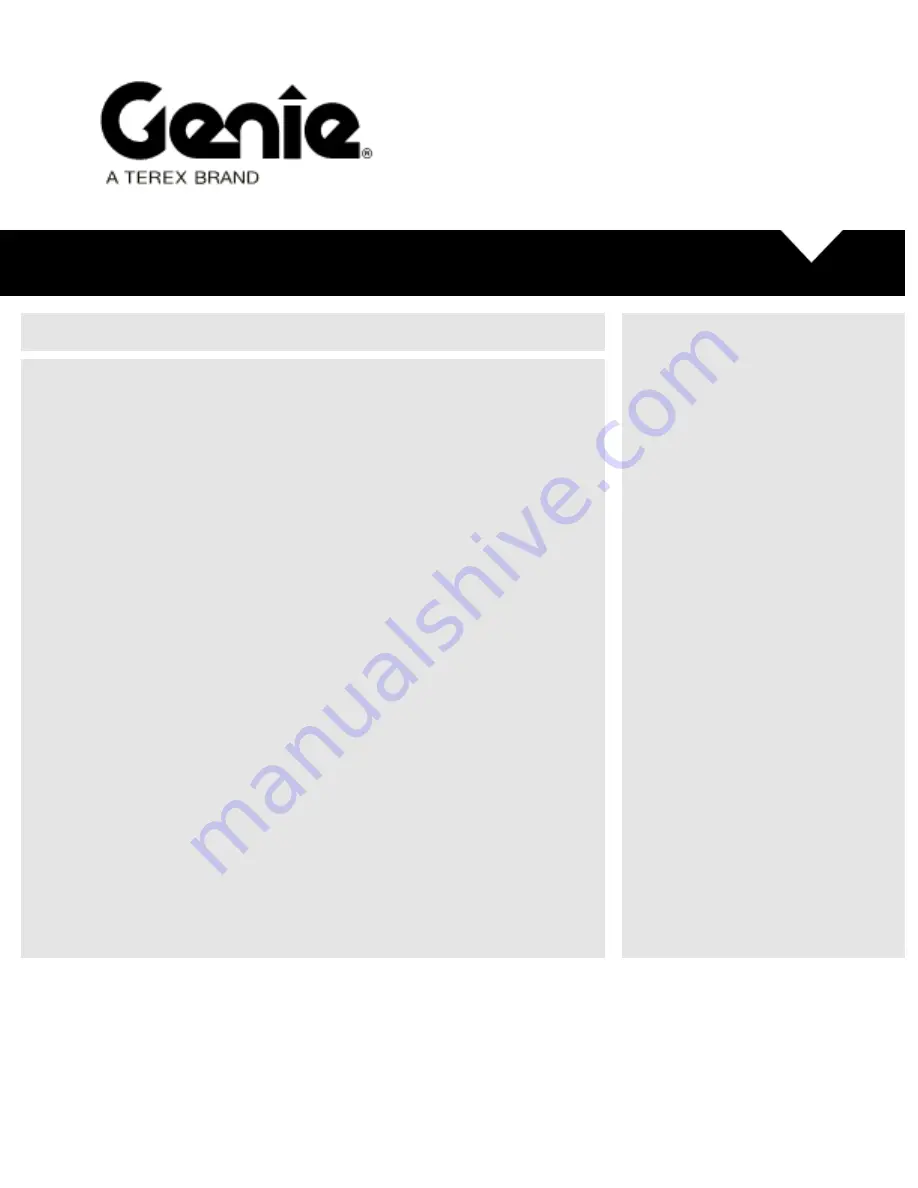
Service and Repair Manual
Serial Number Range
GS
™
-2669 IC
from GS69F-18000
from GS69M-101
This manual includes:
Repair procedures
Fault Codes
Electrical and
Hydraulic Schematics
GS
™
-3369 IC
GS
™
-4069 IC
For detailed maintenance
procedures, refer to the
appropriate Maintenance
Manual for your machine.
Part No. 1306516GT
Rev A1
May 2022
Summary of Contents for GS-2669 IC
Page 141: ...May 2022 Service and Repair Manual 127 GM 998L Engine Wire Harness...
Page 144: ...Service and Repair Manual May 2022 130 Control Panel Circuit Diagram...
Page 145: ...May 2022 Service and Repair Manual 131 Electrical Schematic GS 69 RT GM 998L Models ANSI CSA...
Page 148: ...Service and Repair Manual May 2022 134 Electrical Schematic GS 69 RT GM 998L Models ANSI CSA...
Page 149: ...May 2022 Service and Repair Manual 135 Electrical Schematic GS 69 RT GM 998L Models ANSI CSA...
Page 152: ...Service and Repair Manual May 2022 138 Electrical Schematic GS 69 RT Diesel Models ANSI CSA...
Page 153: ...May 2022 Service and Repair Manual 139 Electrical Schematic GS 69 RT Diesel Models ANSI CSA...
Page 156: ...Service and Repair Manual May 2022 142 Electrical Schematic GS 69 RT Diesel Models ANSI CSA...
Page 157: ...May 2022 Service and Repair Manual 143 Electrical Schematic GS 69 RT GM 998L Models AS CE...
Page 160: ...Service and Repair Manual May 2022 146 Electrical Schematic GS 69 RT GM 998L Models AS CE...
Page 161: ...May 2022 Service and Repair Manual 147 Electrical Schematic GS 69 RT GM 998L Models AS CE...
Page 164: ...Service and Repair Manual May 2022 150 Electrical Schematic GS 69 RT Diesel Models AS CE...
Page 165: ...May 2022 Service and Repair Manual 151 Electrical Schematic GS 69 RT Diesel Models AS CE...
Page 168: ...Service and Repair Manual May 2022 154 Electrical Schematic GS 69 RT Diesel Models AS CE...
Page 169: ...May 2022 Service and Repair Manual 155 Hydraulic Schematic GS 69 RT...
Page 171: ......