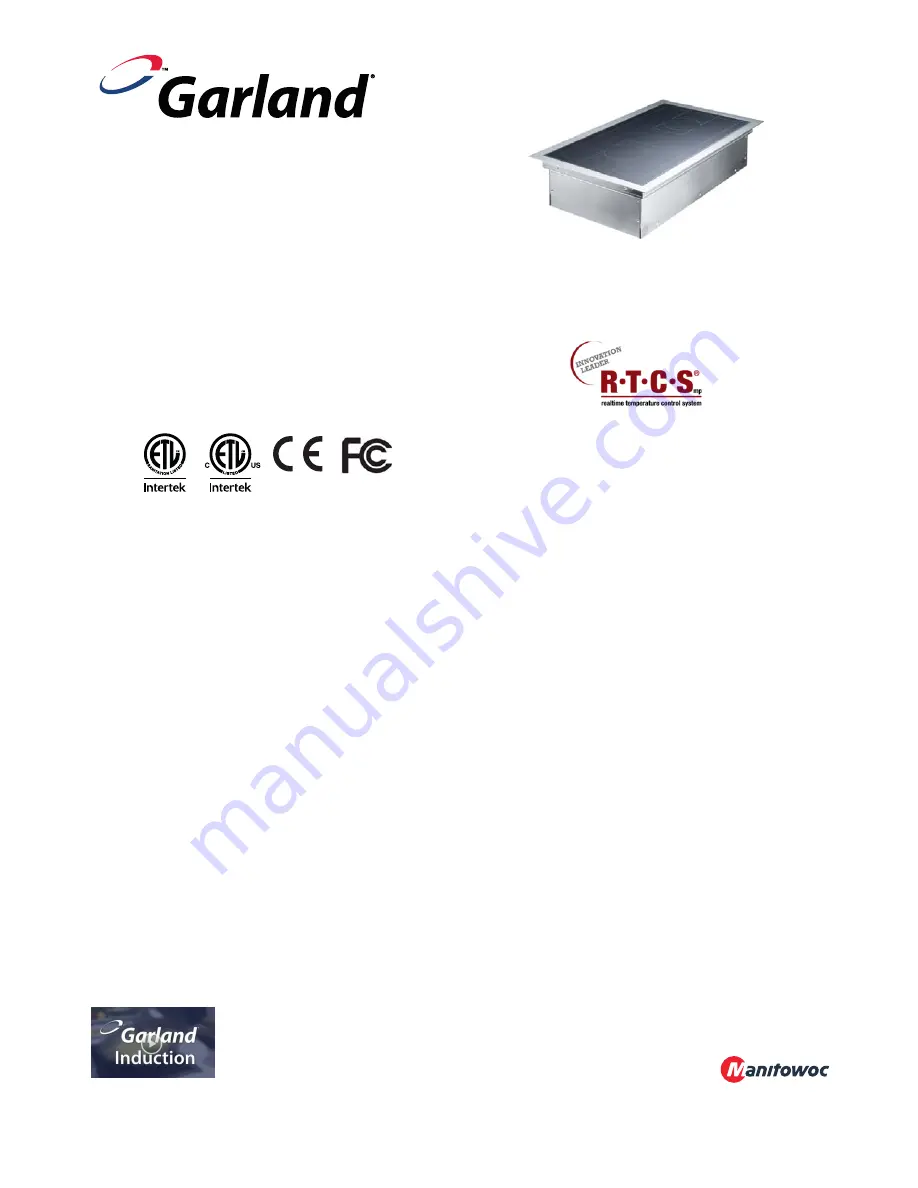
Part # 4532285 Rev 4 (4/29/14)
© 2013 Garland Commercial Ranges Limited
Models:
SH DU IN 7000 (2x3500 / 7kW)
SH DU IN 10000 (2x5000 / 10kW)
INSTALLATION AND
OPERATION MANUAL
GARLAND INDUCTION
BUILT-IN LINE
DUAL-ZONE COOKERS
with RTCSmp TECHNOLOGY
R
eal-time
T
emperature
C
ontrol
S
ystem
m
ulti-
p
oint sensing
PLEASE READ ALL SECTIONS OF THIS MANUAL AND
RETAIN FOR FUTURE REFERENCE.
THIS PRODUCT HAS BEEN CERTIFIED AS
COMMERCIAL COOKING EQUIPMENT AND MUST BE
INSTALLED BY PROFESSIONAL PERSONNEL AS
SPECIFIED
INSTALLATION
AND ELECTRICAL CONNECTION
MUST COMPLY WITH CURRENT CODES IN YOUR
REGIION:
IN CANADA – THE CANADIAN ELECTRICAL CODE
PART 1 AND / OR LOCAL CODES.
IN USA – THE NATIONAL ELECTRICAL CODE ANSI /
NFPA – CURRENT EDITION.
FOR YOUR SAFETY
DO NOT STORE OR USE GASOLINE OR OTHER
FLAMMABLE VAPORS OR LIQUIDS IN THE VICINITY OF
THIS OR ANY OTHER APPLIANCE
CE models
comply with the latest European
Norms:
EN 60335-1, EN 60335-2-36, EN 62233 (EMC/EMV)
North American models
: ETL listed in compliance
with UL 197, CSA C22.2 No.109, NSF-4
Complies with FCC part 18, ICES-001
WARNING
IMPROPER INSTALLATION, ADJUSTMENT,
ALTERATION, SERVICE OR MAINTENANCE CAN
CAUSE PROPERTY DAMAGE, INJURY, OR DEATH.
READ THE INSTALLATION, OPERATING AND
MAINTENANCE INSTRUCTIONS THOROUGHLY
BEFORE INSTALLING OR SERVICING THIS
EQUIPMENT
Users are cautioned that maintenance and repairs must be performed by a Garland authorized service agent using only
genuine Garland replacement parts. Garland will have no obligation with respect to any product that has been improperly
installed, adjusted, operated or not maintained in accordance with national and local codes and/or installation instructions
provided with the product or any product that has its serial number defaced, obliterated or removed, and/or which has been
modified or repaired using unauthorized parts or by unauthorized service agents. For a list of authorized service agents
and/or genuine replacement parts, please visit our website at
www.garland-group.com (USA and Canadian customers) or
www.manitowocfoodservice.com (international customers).
The information contained herein, including design and part
specifications, may be superseded and is subject to change without notice.
Visit our
Video Gallery
at
www.Garland-Group.com