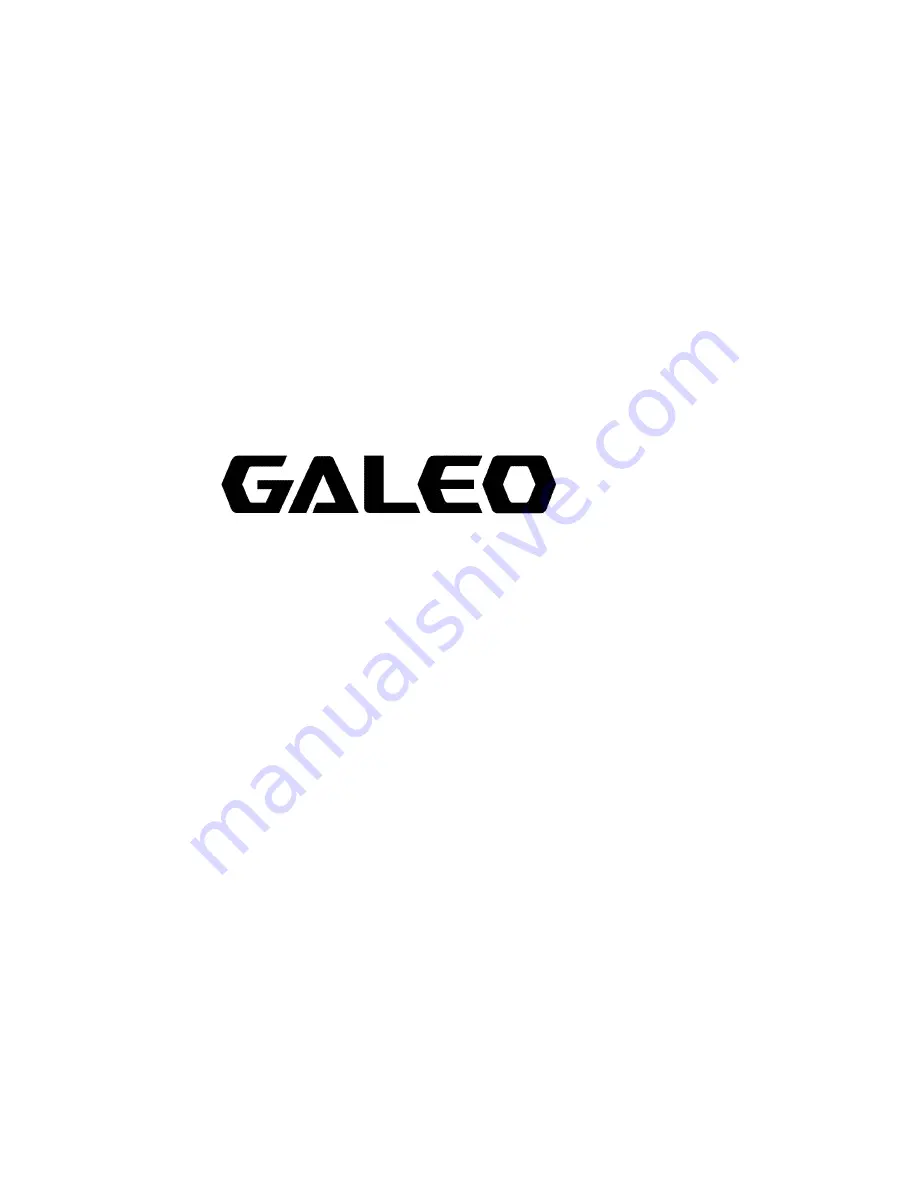
TEN00074-00
Operation & Maintenance
Manual
PC78MR
-6
HYDRAULIC EXCAVATOR
SERIAL NUMBERS
PC78MR-6 1507
and up
This material is proprietary to Komatsu America Corp. and is not to be reproduced, used, or disclosed except in
accordance with written authorization from Komatsu America Corp.
It is our policy to improve our products whenever it is possible and practical to do so. We reserve the right to make
changes or improvements at any time without incurring any obligation to install such changes on products sold
previously.
Due to this continuous program of research and development, revisions may be made to this publication. It is
recommended that customers contact their distributor for information on the latest revision.
Copyright 2005 Komatsu
Printed in U.S.A.
Komatsu America Corp.
April 2005
Summary of Contents for PC78MR-6
Page 2: ... 1 1 ...
Page 4: ... FOREWORD FOREWORD 1 3 ...
Page 5: ... FOREWORD FOREWORD 1 4 ...
Page 15: ... ...
Page 16: ... 2 1 ...
Page 20: ... SAFETY SAFETY LABELS LOCATION OF SAFETY LABELS 2 5 ...
Page 55: ... ...
Page 56: ... 3 1 ...
Page 195: ... ...
Page 196: ... 4 1 ...
Page 271: ... ...
Page 272: ... 5 1 ...
Page 275: ... ...
Page 276: ... 6 1 ...
Page 294: ... ...