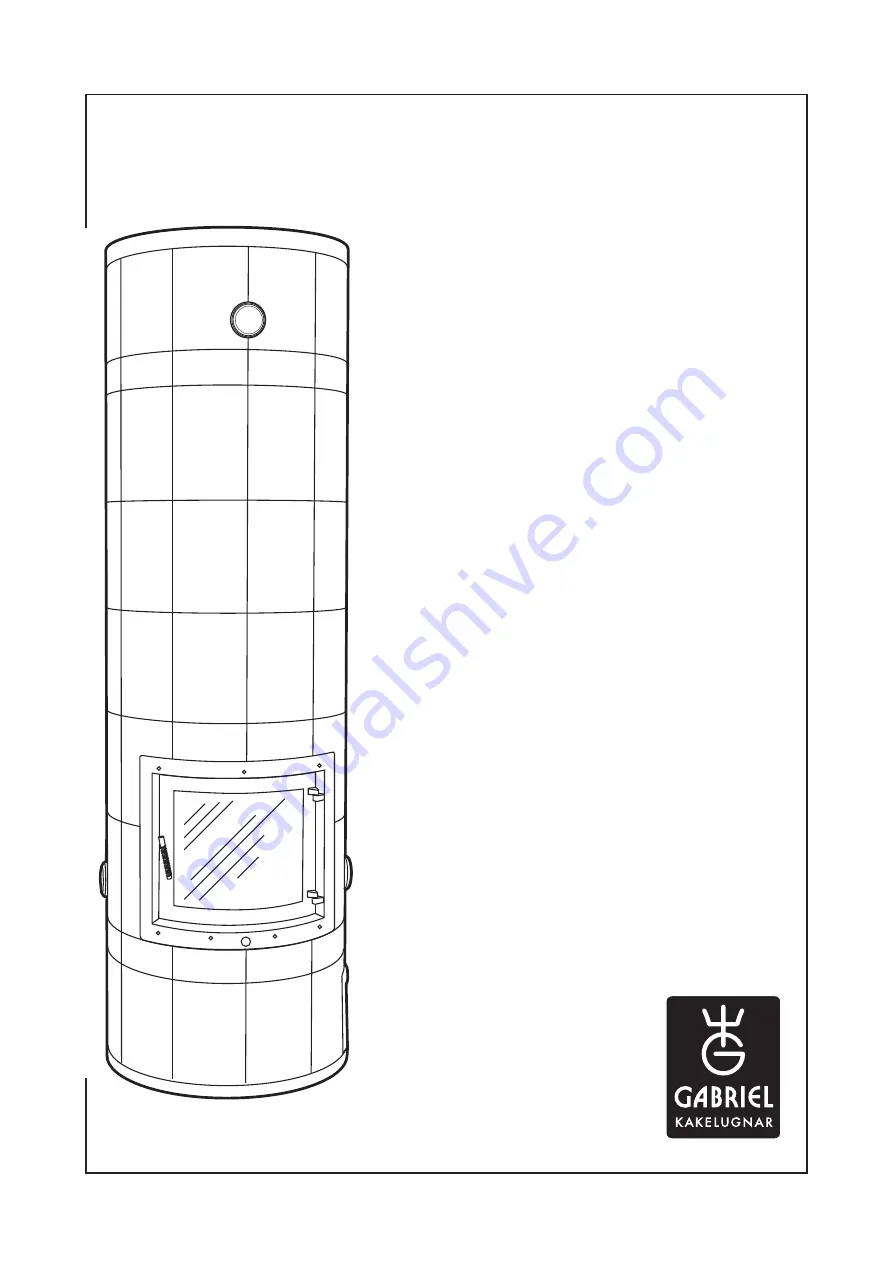
2012-07-02
Assembly instruction
STUDIO
tiled stove
(series 400)
Model....................................
Content
Tests and approvals ............................ 2
Explanation of symbols / foreword ...... 3
Body
Preparations ...................................... 4
Important measurements...................... 5
Overall installation sequence ............... 6
Assembly ..................................... 7-17
Tiles and cassette
Tiling preparation and assembly ... 17-18
Tiling plan ....................................... 19
Cassette installation ..................... 20-23
Fan installation ................................ 23