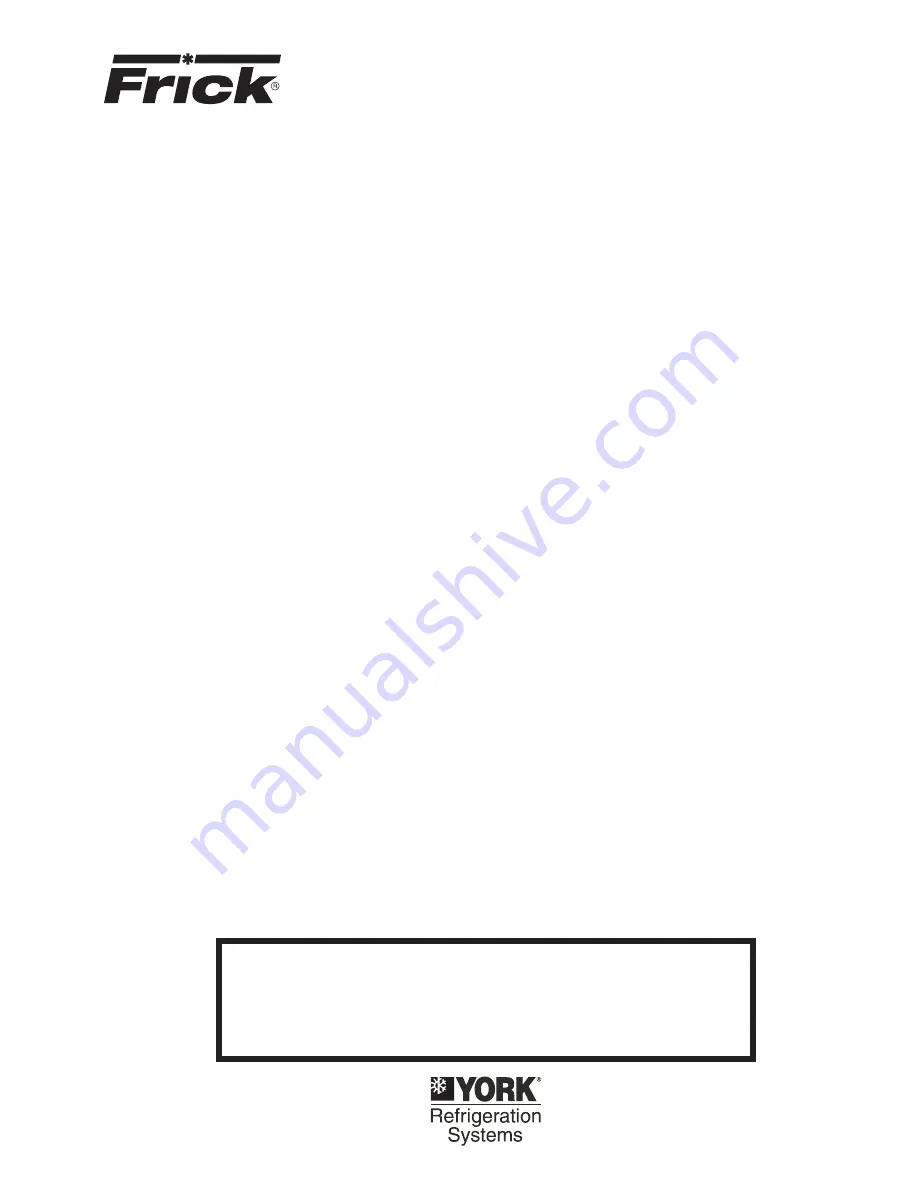
Installation - Operation - Maintenance
ROTARY SCREW COMPRESSOR UNITS
ALL REFRIGERANTS
MODELS
100 through 480
THIS MANUAL CONTAINS RIGGING, ASSEMBLY, START-UP, AND
MAINTENANCE INSTRUCTIONS. READ THOROUGHLY BEFORE
BEGINNING INSTALLATION. FAILURE TO FOLLOW THESE IN-
STRUCTIONS COULD RESULT IN DAMAGE OR IMPROPER OPERA-
TION OF THE UNIT.
S70-600 IOM/MAY 2001
File:
SERVICE MANUAL - Section 70
Replaces:
S70-600 IOM/MAR 2000
Dist:
3, 3a, 3b, 3c
RWF
Summary of Contents for RWF
Page 37: ...RWF ROTARY SCREW COMPRESSOR UNITS MAINTENANCE S70 600 IOM Page 37 P I DIAGRAM ...
Page 47: ...RWF ROTARY SCREW COMPRESSOR UNITS MAINTENANCE S70 600 IOM Page 47 OPERATING LOG SHEET ...
Page 53: ...RWF ROTARY SCREW COMPRESSOR UNITS MAINTENANCE S70 600 IOM Page 53 ...
Page 54: ...RWF ROTARY SCREW COMPRESSOR UNITS MAINTENANCE S70 600 IOM Page 54 ...
Page 55: ...RWF ROTARY SCREW COMPRESSOR UNITS MAINTENANCE S70 600 IOM Page 55 ...