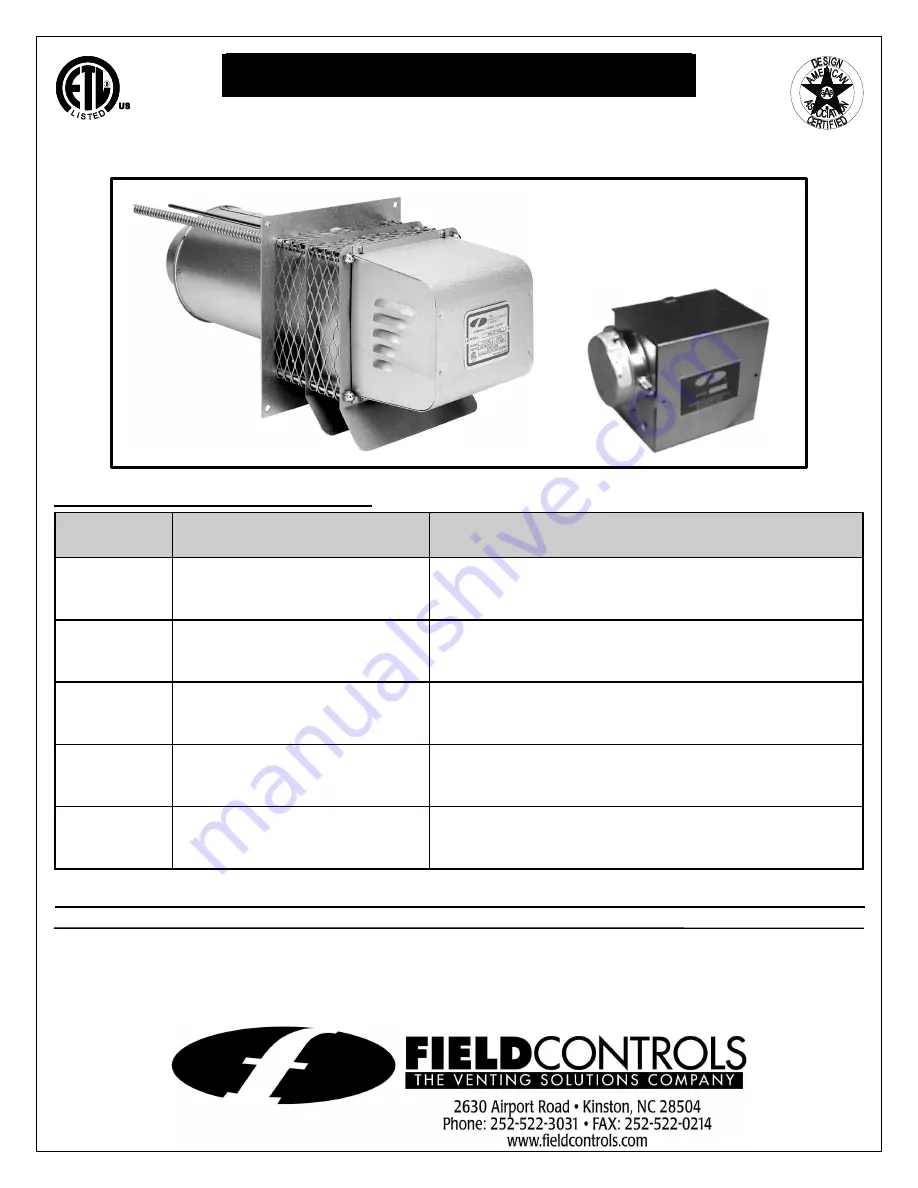
SIDEWALL POWER VENTER KIT
Model:
SWGII-5,6 AGA and SWG-8*
FOR COMMERCIAL WATER HEATERS
*Patented
TYPICAL VENTING SYSTEM COMPONENTS:
PART
NUMBER
DESCRIPTION
APPLICATION
239-81764-00
SWGII-5 POWER VENTER,
CK-41 24 VOLT CONTROL KIT
COMMERCIAL WATER HEATERS WITH 24 VOLT
CONTROLS WITH INPUT RATINGS OF UP TO 290,000
BTU/HR.
239-81765-00
SWGII-5 POWER VENTER,
CK-81 MILLIVOLT CONTROL KIT
COMMERCIAL WATER HEATERS WITH MILLIVOLT
CONTROLS WITH INPUT RATINGS OF UP TO 290,000
BTU/HR.
239-81766-00
SWGII-6 POWER VENTER,
CK-41 24 VOLT CONTROL KIT
COMMERCIAL WATER HEATERS WITH 24 VOLT
CONTROLS WITH INPUT RATINGS GREATER THAN
290,000 BTU/HR. UP TO 416,000 BTU/HR.
239-81767-00
SWGII-6 POWER VENTER,
CK-81 MILLIVOLT CONTROL KIT
COMMERCIAL WATER HEATERS WITH 24 VOLT
CONTROLS WITH INPUT RATINGS GREATER THAN
290,000 BTU/HR. UP TO 416,000 BTU/HR.
239-82148-00
SWG-8 POWER VENTER,
CK-41 24 VOLT CONTROL KIT
COMMERCIAL WATER HEATERS WITH 24 VOLT
CONTROLS WITH INPUT RATINGS GREATER THAN
415,000 BTU/HR.
DO NOT DESTROY
THESE INSTRUCTIONS MUST REMAIN WITH EQUIPMENT
Summary of Contents for 46256400
Page 9: ...Figure 11 Page 9 ...
Page 10: ...Figure 12 Page 10 ...
Page 16: ...PN 46256400 Rev B 7 00 ...