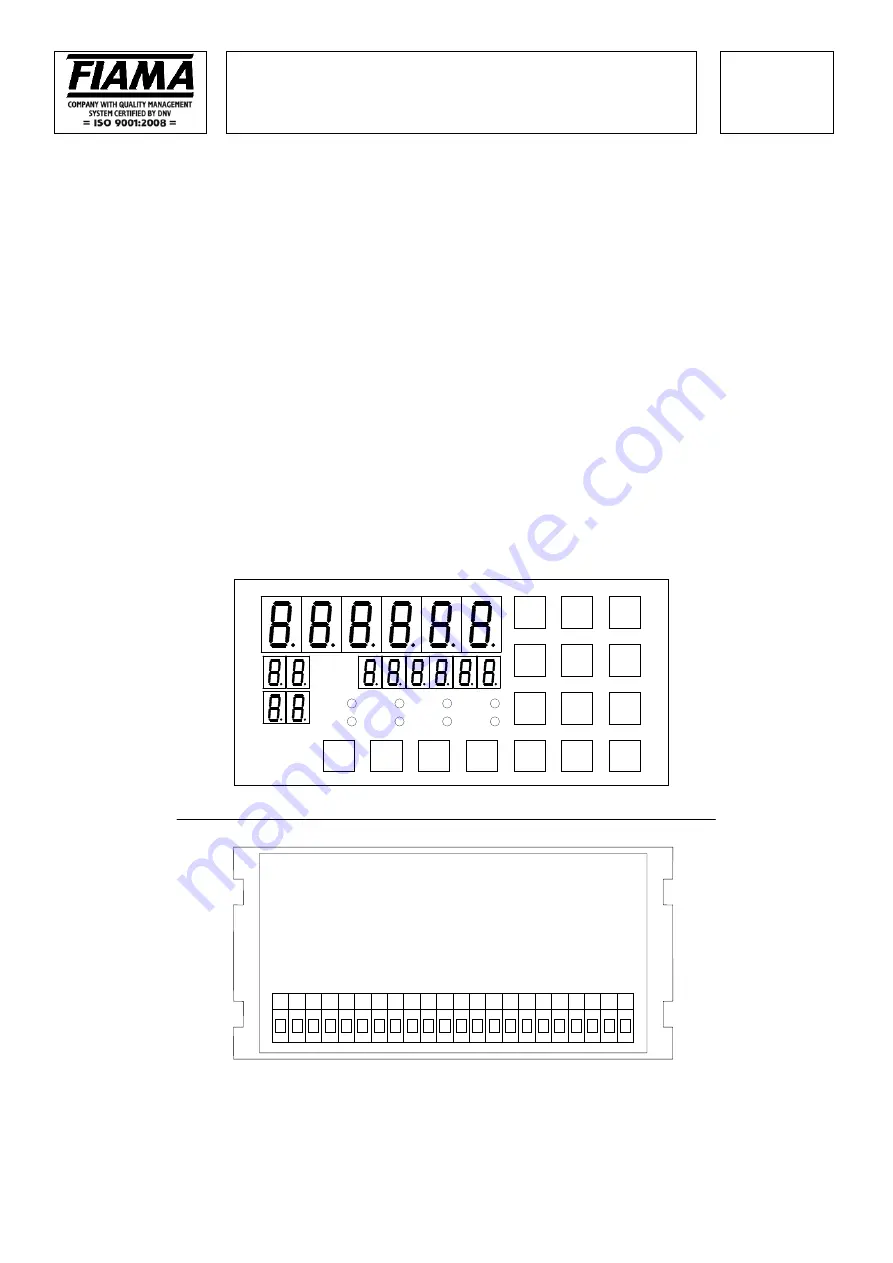
data: 13/03/03
file: P1X_ing.doc
Rev: 1.1
pag 1 di 11
The P1X is a programmable single-axis positioner with microprocessor with relay outputs that processes
signals supplied by incremental transducers such as encoders, magnetic lines, optical lines, etc.
Positioning is managed through the stop/onward/backward, slow/fast, end of positioning, and auxiliary outputs
and through the optoinsulated start, emergency, reset, and work counter inputs.
The axis dimension is displayed on the high brightness six-digit display (reading scale -99999, +999999) and
three auxiliary displays show the set dimension, the machine constants, and the processing parameters.
The keyboard with 16 keys and 8 function indicators make the positioner use and setting up easy.
The P1X can memorize up to 99 dimensions to create positioning programmes giving the possibility to manage
for every dimension the number of parts that are to be processed in sequence as well as the number of cycle
repetitions. In order to optimize positioning accuracy there are some parameters that can counterbalance
system inertia, clearances, and wear and tear of mechanical couplings.
Find below the other features characterising the instrument:
automatic/semiautomatic, manual functioning modes, absolute/line, single positioning, blade thickness
compensation, zero research, inputs and outputs test; and serial connection RS232 or RS485 with MODBUS
RTU protocol to dialogue with remote units.
The keeping of data when there is no power supply is guaranteed by a non volatile EEPROM memory.
The instrument is enclosed in a panel box 72x144 conforming to the DIN 43700 standard.
Front view
Back view
1 2 3 4 5 6 7 8 9 10 11 12 13 14 15 16 17 18 19 20 21 22
Positioner P1X
P1X0
P1X1
P1X2
P1X3
+
-
START
STOP
MAN
ZERO
SING
A/S
PROG
COST
TEST
CYCL
1
2
3
4
5
6
7
8
1
2
5
4
3
.
7
8
9
6
<
<<
>>
>
0
C
P
E