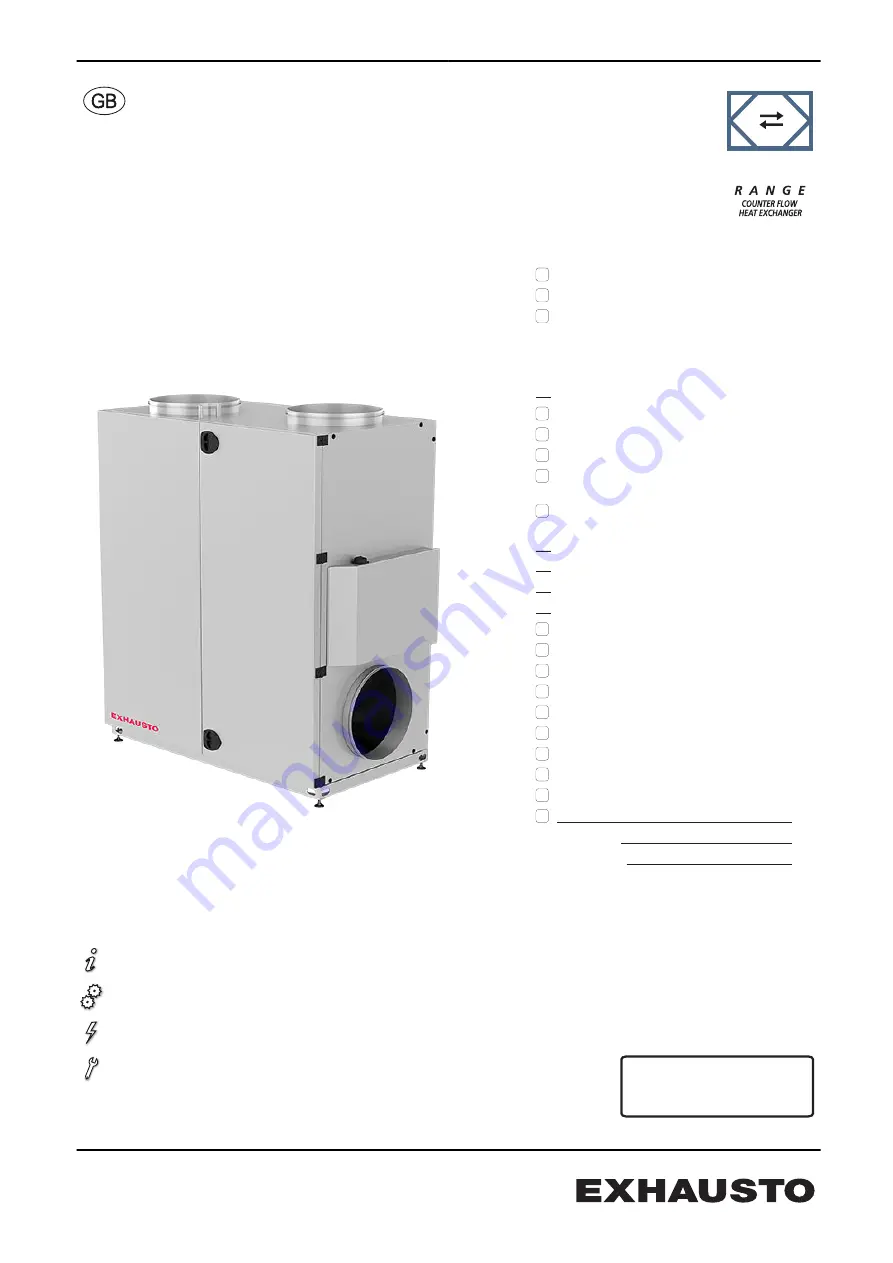
VEX160CF Vertical HCW
with EXact2 control
VEX100 CF
Product information........................................ Chapter 1 + 6
Mechanical assembly..................................... Chapter 2 + 3
Electrical installation.......................................Chapter 4
Maintenance...................................................Chapter 5
Unit supplied with (factory fitted):
The following accessories are supplied
separately:
VDI 6022
M5-compact filter, FP
F7-compact filter, FP
pieces, control panel, HMI
Motor valve, MVM ______K
vs
-value
Closing damper, LS500-24, (LSA exhaust)
Closing damper, LS500-24, (LSF outdoor)
Closing damper, LSR500-24, with
spring-return (LSAR exhaust)
Closing damper, LSR500-24, with
spring-return (LSFR outdoor)
pieces, Fire thermostat, BT40
pieces, Fire thermostat, BT50
pieces, Fire thermostat, BT70
pieces, Constant pressure control, MPT-DUCT
Motion sensor, MIO-PIR
Humidity sensor, MIO-RH
CO
2
-sensor, MIO-CO2-DUCT
CO
2
-sensor, MIO-CO2-ROOM
Temperature sensor, MIO-TS-DUCT
Temperature sensor, MIO-TS-ROOM
Control for external cooling unit, MXCU
Mounting base, MSV160V
TS-RPT-X
Prod.order no.:
Sales order no.:
Original instructions
3005706-2017-06-08
VEX160CF V_HCW
EXHAUSTO A/S
Odensevej 76
GB-5550 Langeskov
Tel. +45 65 66 12 34
Fax +45 65 66 11 10
[email protected]
www.exhausto.dk
Summary of Contents for VEX100CF Series
Page 33: ...3005706 2017 06 08 33 36 ...
Page 34: ...3005706 2017 06 08 34 36 ...
Page 35: ...3005706 2017 06 08 35 36 ...
Page 36: ......