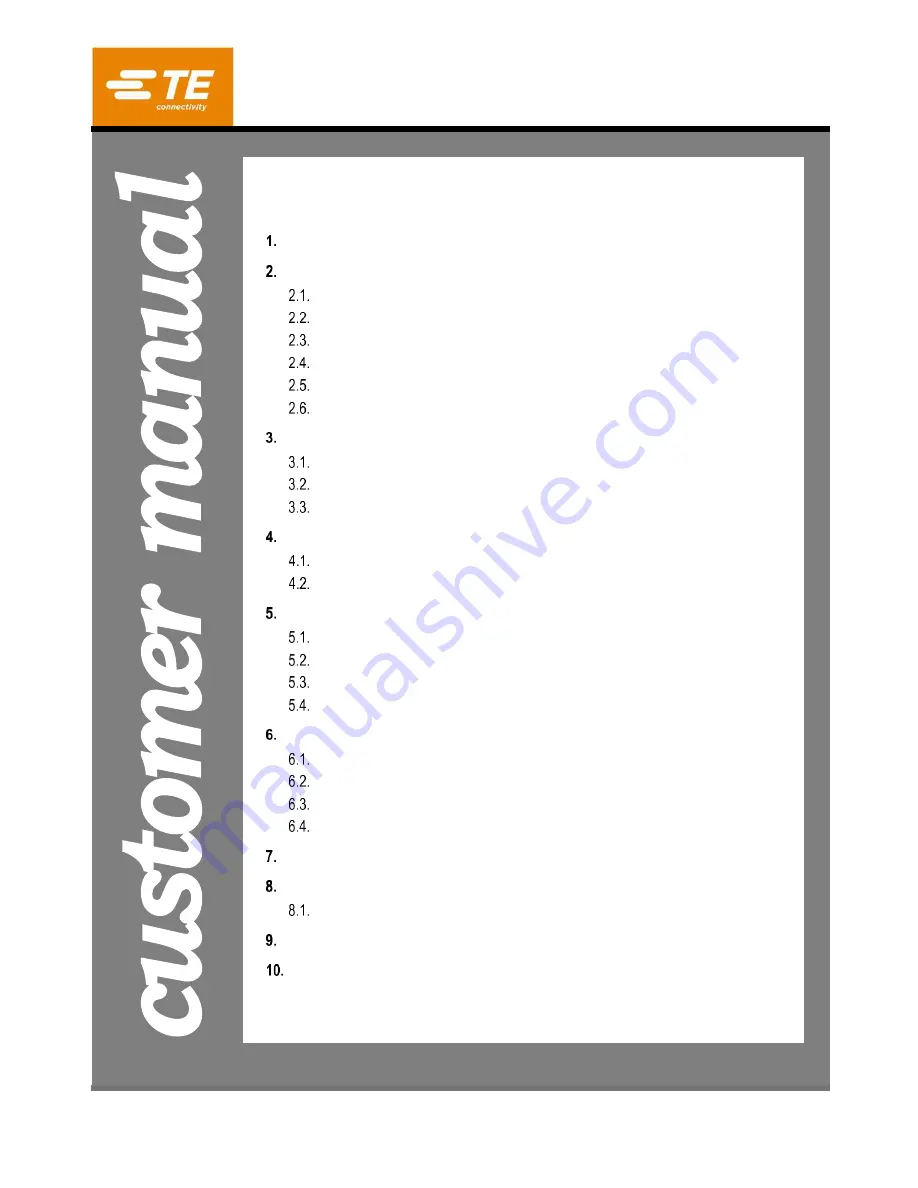
Customer Manual
1
of 83
© 2021 TE Connectivity Ltd. family of companies.
All Rights Reserved.
TE Connectivity, TE connectivity (logo), and TE (logo) are trademarks. Other logos, product, and/or company names may be trademarks of their respective owners.
PRODUCT INFORMATION 1-800-522-6752
This controlled document is subject to change.
For latest revision and Regional Customer Service,
visit our website at
409-35011
1 OCT 2021
Rev D
READ THIS FIRST! ..................................................................... 2
READ THIS FIRST! ...................................... 3
Semi-Automatic High Voltage Cable
Preparation Machine (PN 2335400-1)
O
R
IG
IN
A
L
IN
S
TR
U
C
TIONS