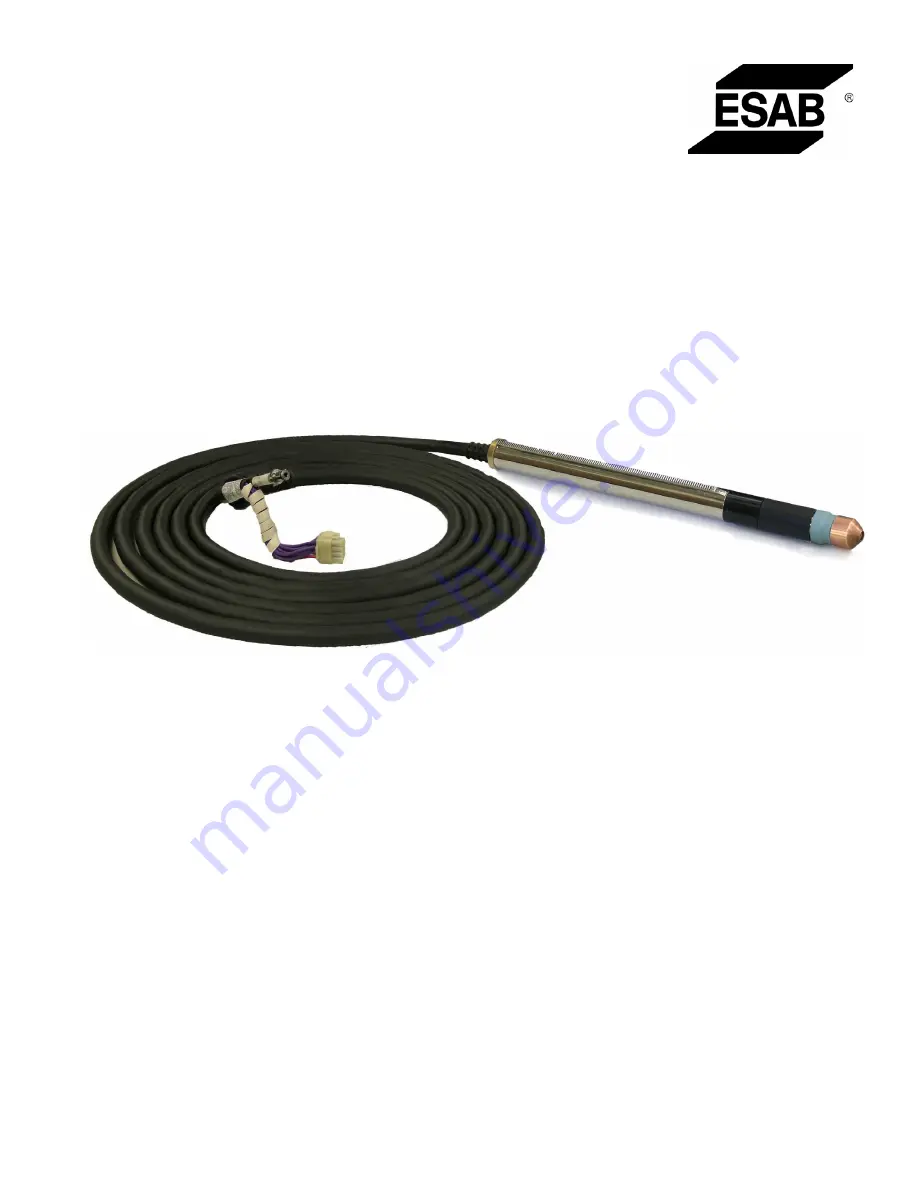
PT-37
Plasmarc Cutting Torches
0558005966
05/2011
Instruction Manual
P/N 0558004860 - PT-37 Torch with rack 4.5' (1.4 m)
P/N 0558004861 - PT-37 Torch with rack 17' (5.2 m)
P/N 0558004862 - PT-37 Torch with rack 25' (7.6 m)
P/N 0558004863 - PT-37 Torch with rack 50' (15.2 m)
P/N 0558004894 - PT-37 Torch w/o rack 4.5' (1.4 m)
P/N 0558004895 - PT-37 Torch w/o rack 17' (5.2 m)
P/N 0558004896 - PT-37 Torch w/o rack 25' (7.6 m)
P/N 0558004897 - PT-37 Torch w/o rack 50' (15.2 m)
Summary of Contents for PT-37
Page 4: ...4 TABLE OF CONTENTS ...
Page 30: ...30 section 4 operation ...
Page 64: ...64 section 4 operation ...
Page 72: ...72 SECTION 5 MAINTENANCE ...
Page 76: ...76 notes ...
Page 77: ...77 notes ...
Page 78: ...78 notes ...