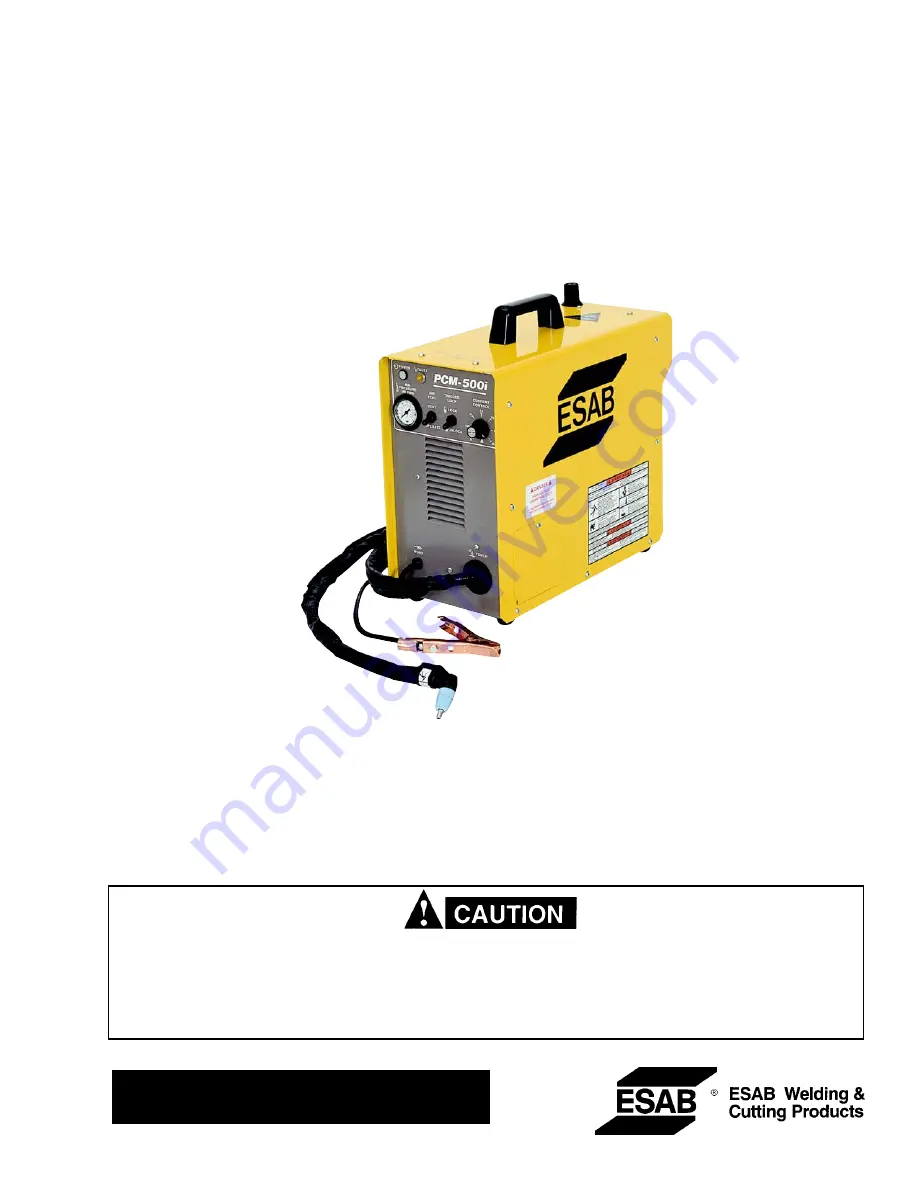
INSTRUCTION MANUAL
PCM-500i
PLASMA ARC CUTTING PACKAGES
These INSTRUCTIONS are for experienced operators. If you are not fully familiar with the principles of operation and
safe practices for arc welding equipment, we urge you to read our booklet, "Precautions and Safe Practices for Arc
Welding, Cutting, and Gouging," Form 52-529. Do NOT permit untrained persons to install, operate, or maintain this
equipment. Do NOT attempt to install or operate this equipment until you have read and fully understand these
instructions. If you do not fully understand these instructions, contact your supplier for further information. Be sure
to read the Safety Precautions before installing or operating this equipment.
F-15-296-
E
Feb.
, 200
4
This manual provides complete instructions for the following PCM-500i cutting packages starting with Serial No. PORI612001:
ESAB P/N 36314 - 208/230 V, 1-Phase, 50/60 Hz
ESAB P/N 36316 - 400 V (380/415 V), 3-Phase, 50/60 Hz
Be sure this information reaches the operator.
You can get extra copies through your supplier.
Summary of Contents for PCM-500i
Page 28: ...28 D 36403 G Sheet 1 Figure 5 2 Wiring Diagram PCM 500i 200 230 Vac 50 60 Hz 1 Phase Sheet 1 ...
Page 29: ...29 D 36403 G Sheet 2 Figure 5 2 Wiring Diagram PCM 500i 200 230 Vac 50 60 Hz 1 Phase Sheet 2 ...
Page 30: ...30 D 36339 E Figure 5 3 Schematic Diagram PCM 500i 380 415 Vac 50 60 Hz 3 Phase ...
Page 31: ...31 D 36524 E Sheet 1 Figure 5 4 Wiring Diagram PCM 500i 380 415 Vac 50 60 Hz 3 Phase Sheet 1 ...
Page 32: ...32 D 36524 E Sheet 2 Figure 5 4 Wiring Diagram PCM 500i 380 415 Vac 50 60 Hz 3 Phase Sheet 2 ...