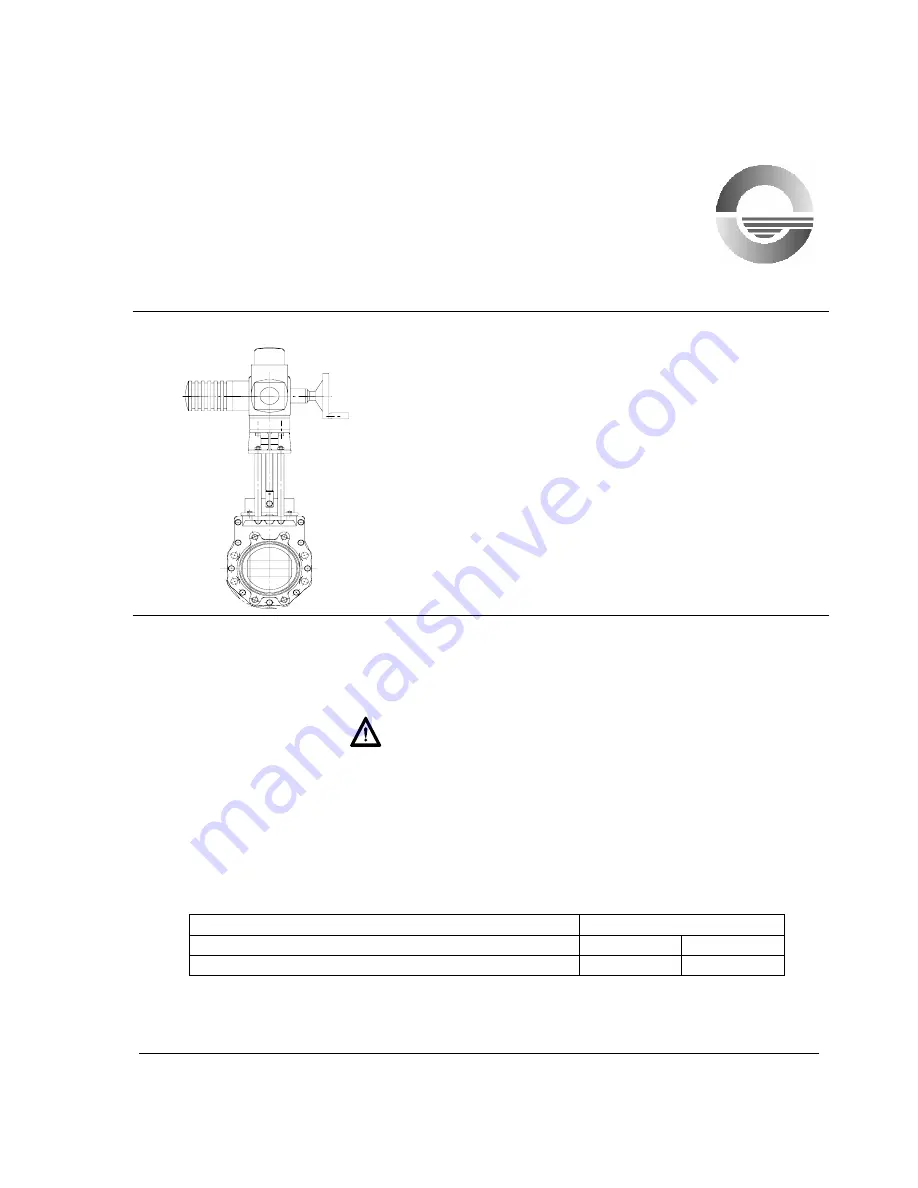
BA46E033
Operating Instructions
ERHARD ERU Knife Gate Valve K1
DN 50 - 300
Electric Actuator
1 Safety
2 Description of Product and Range of Application
3 Design Features – Technical Data
4 Performance and Mode of Operation
5 Storage
6 Installation into the Pipeline - Mounting
7 Initial
Operation
8 Operation
9 Maintenance
These operating instructions must always be used in combination with operating
instructions BA01E001!
1 Safety
Access to the range of movement of the gate of ERU Knife Gate Valves with electric
actuator has to be restricted by protective devices. Effective protective devices have to
be installed by the user.
On request, we will supply suitable protective guards.
2
Description of Product and Range of Application
Type/Design Product
Number
ERU Knife Gate Valve K1
4657
PN 10
ERU Knife Gate Valve K1 with regulating orifice
4623
PN 10
Design with electric actuator
BA46E033
July 2005
Rev. 4
ERHARD-Armaturen
x
D-89502 Heidenheim
x
Postfach 1280
(07321) 320-0
(07321) 320 491 e-mail:info
@
erhard.de
Internet: http://www.erhard.de
Page 1 of 13