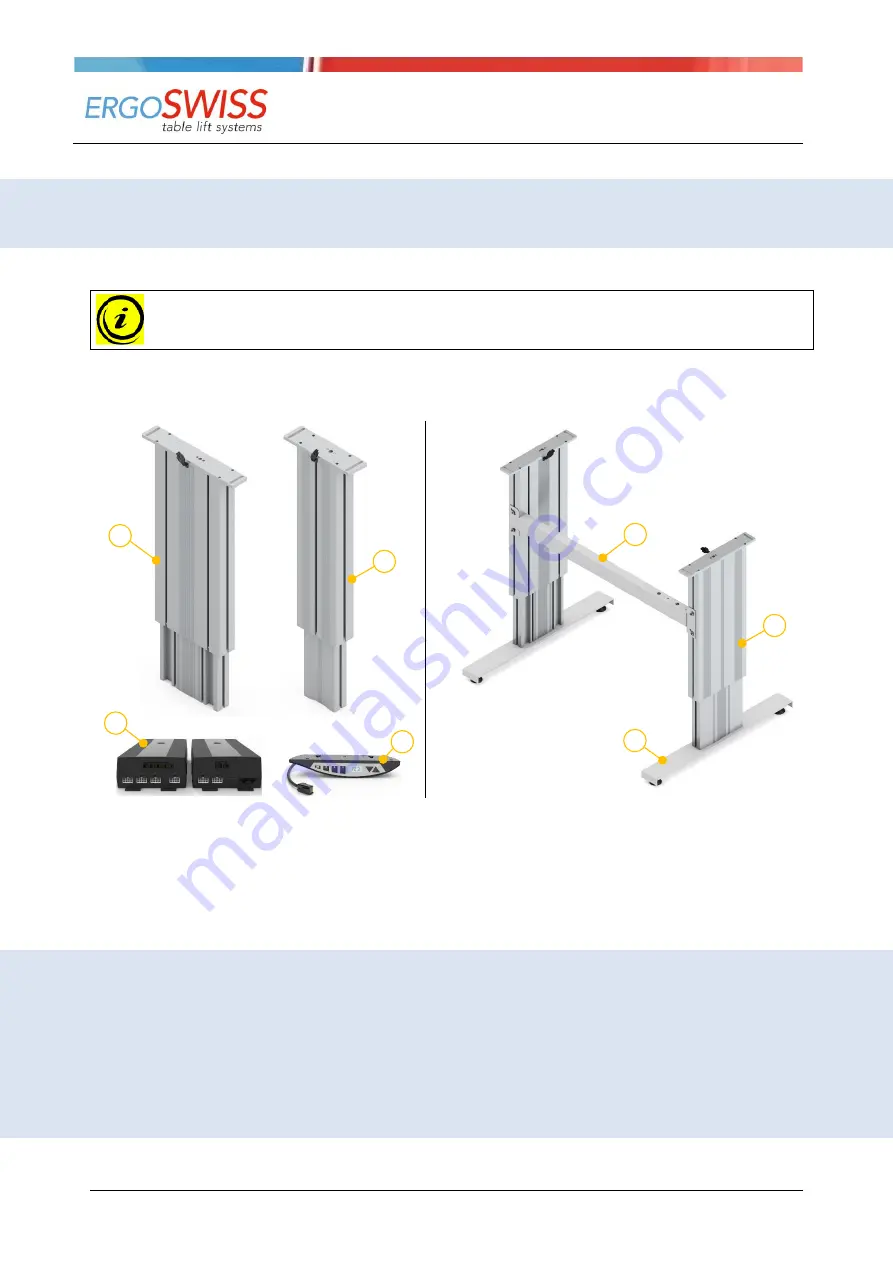
Operating Instruction
Spindle lifting system SL/SM 13xx with SCT iSMPS
Document no : B-00361
Edition 2020 06
Operating instruction EN
Copyright by Ergoswiss AG
1/27
Operating instruction
–
Spindle lifting system SL/SM 13xx with SCT iSMPS
It is essential to read this operating instruction thoroughly before commissioning the system.
Spindle lifting column type SL 13xx
Spindle lifting column type SM 13xx
Control box SCT iSMPS
Manual control switch Up-Down or Memory
Example of a table frame with two lifting columns
Cross bar
Table feet
Errors and technical changes reserved.
Ergoswiss AG does not assume any liability for operat-
ing errors or using the products outside of the intended
purpose use.
At the time of delivery Ergoswiss AG will replace or re-
pair defect products within accordance with the warranty
provisions. In addition, Ergoswiss assumes no other lia-
bility.
For your questions and special custom demand
Ergoswiss AG will be at your disposal.
Ergoswiss AG
Nöllenstrasse 15
CH-9443 Widnau
Tel.: +41 (0) 71 727 06 70
Fax: +41 (0) 71 727 06 79
[email protected]
www.ergoswiss.com
5
2
3
1
6
1
4