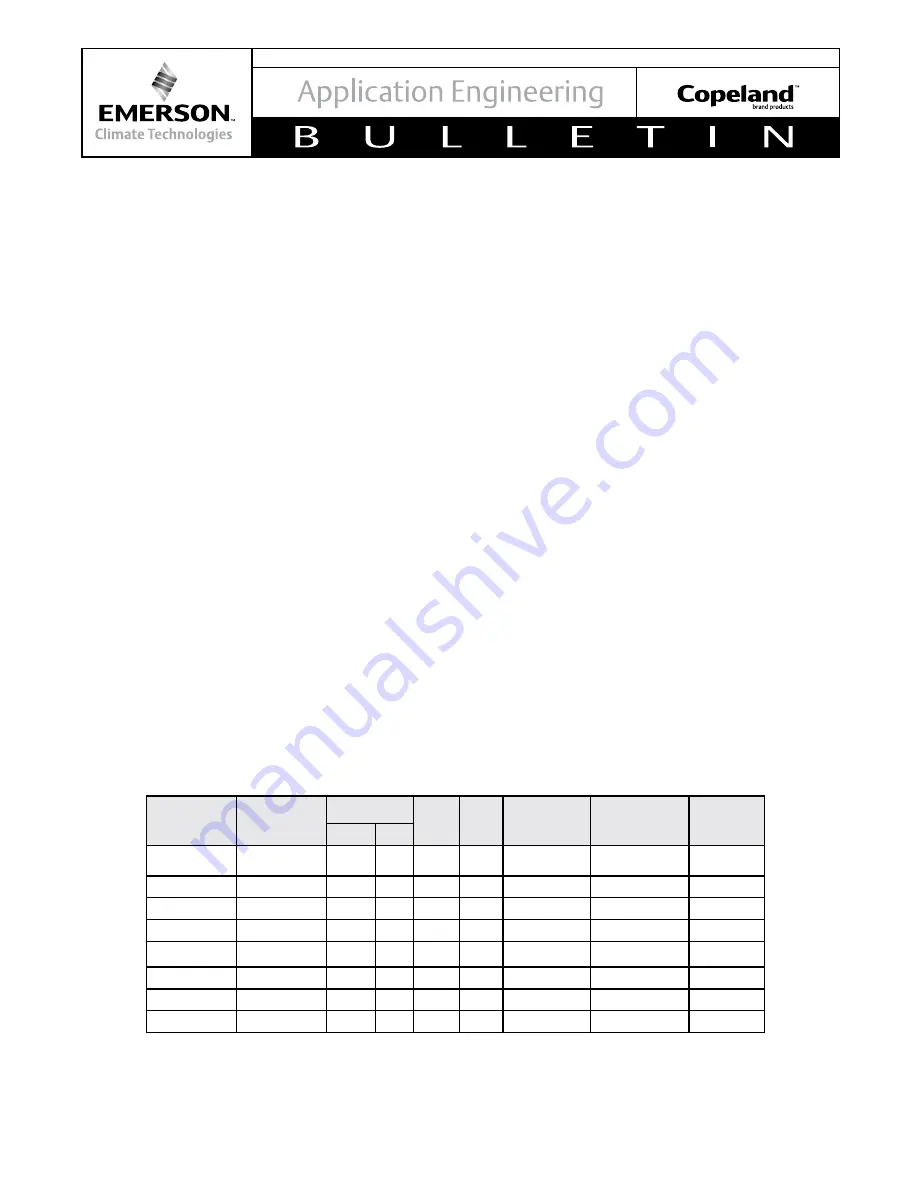
AE4-1312 R2
© 2010 Emerson Climate Technologies
Printed in the U.S.A.
1
AE4-1312 R2
January, 2005
Reformatted November 2010
Application Guidelines for 1.5 to 6.75 Ton Refrigerant
R-22, 407C, 134A Copeland Scroll
®
Compressors
Introduction
The ZR*KA, ZR*KC, ZR*K3, & ZR*K4 Copeland Scroll
®
compressors include a wide range of capacities,
electrical options, and features. Typical model numbers
are ZR24K4-PFV and ZR81KC-TF5. This bulletin
describes the operating characteristics, design features,
and application requirements for these models. For
additional information, please refer to the online
product information accessible from the Emerson
Climate Technologies website at www.emersonclimate.
com. Operating principles of the Copeland Scroll are
described in
Figure 7
at the end of this bulletin.
The ZR*KA scroll compressors are designed for
air
conditioning systems only
in the 12+ SEER range
but may be applied to 10 SEER A/C systems if desired.
They range in size from 16,000 to 54000 Btu/hr (4.7 to
15.8 kw-hr).
The ZR*K3 and K4 are models designed for 11+ SEER
A/C and heat pump usage ranging in size from 16,000
to 61,000 Btu/hr (4.7 to 17.9 kw-hr).
The ZR*KC models are designed for 10 SEER
A/C and heat pump usage ranging in size from 16,000
to 81,000 Btu/hr (4.7 to 23.7 kw-hr).
The models include a number of features outlined in
the matrix below:
IPR Valve-Internal Pressure Relief Valve
The internal pressure relief valve is located between
the high side and the low side of the compressor. It
is designed to open when the discharge to suction
differential pressure exceeds 375 to 450 psid (26 – 32
kg/cm2). When the valve opens, hot discharge gas
is routed back into the area of the motor protector to
cause a trip.During developmental blocked fan testing,
it is sometimes noted that the valve opens, but the
compressor does not shut off while the discharge
pressure continues to climb. This condition is normally
caused by refrigerant flood back and may be corrected
by using a more restrictive expansion device or reducing
the refrigerant charge.
Internal Temperature Protection
The Therm-O-Disc
®
or TOD is a temperature-sensitive
snap disc device located between the high and low
pressure side of the scroll. It is designed to open and
route excessively hot discharge gas back to the motor
protector. During a situation such as loss of charge,
the compressor will be protected for some time while
it trips on the protector. However, as refrigerant leaks
out, the mass flow and the amperage draw are reduced
and the scrolls will start to overheat. Normally, during
air conditioning operation the problem is detected
because of rising indoor temperatures before damage
is done. This may not be the case during heat pump
Motor
Frame Size*
Application
IPR
TOD Quiet Shut
Down
Discharge
Check Valve
Motor
Protector
AC
HP
ZR16-29KC
53
X
X
NO
X
X
X
X
ZR16-24K4
53
X
X
NO
X
X
X
X
ZR16-34KA
53
X
NO
X
X
X
X
X
ZR38-54KA
63
X
NO
X
X
X
X
X
ZR18-48K3
63
X
X
X
X
X
X
X
ZR26-48KC
63
X
X
X
X
X
X
X
ZR54-61K3
70
X
X
X
X
X
X
X
ZR54-81KC
70
X
X
X
X
X
X
X
*
Approximate Shell Diameter (e.g. 53 = 5.5 Inches)