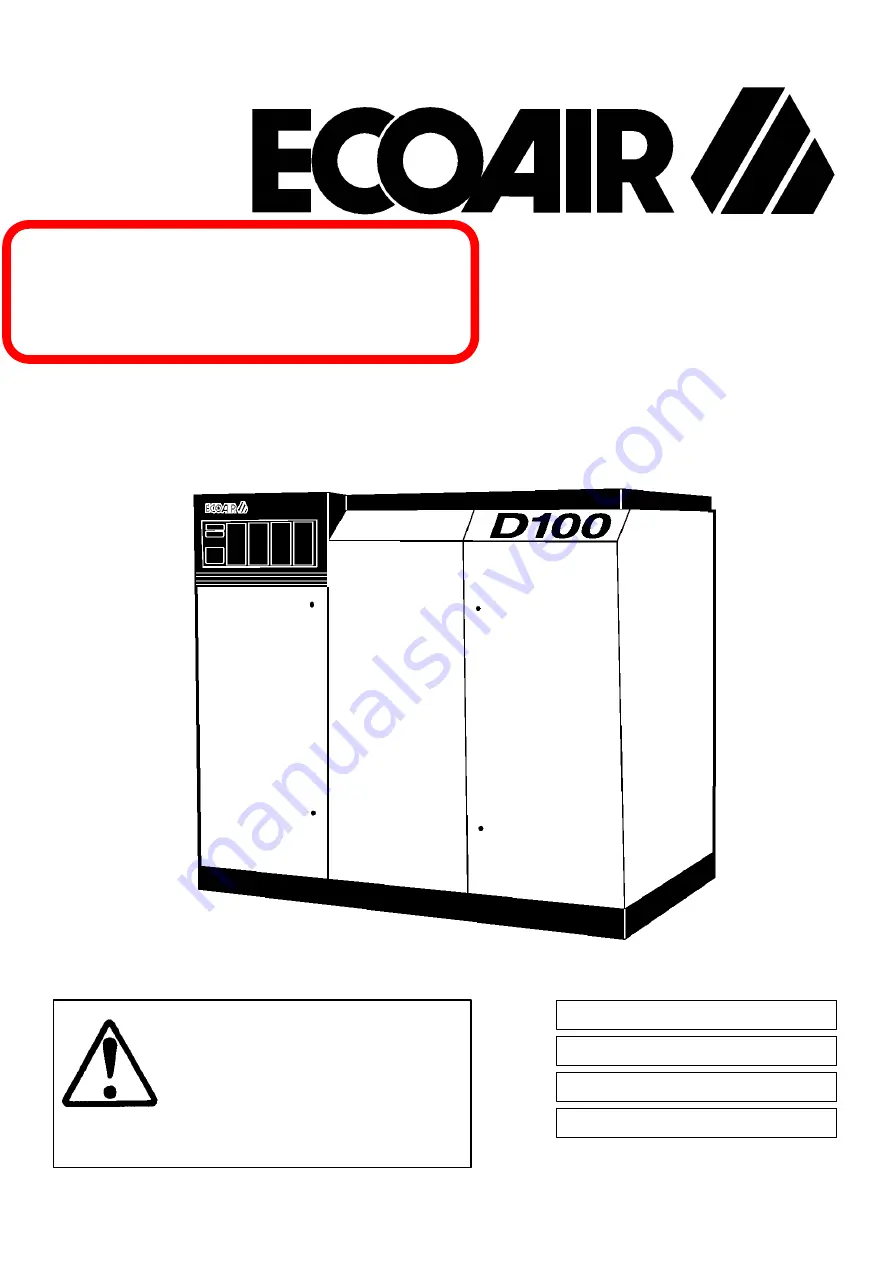
C.P.N. : 89290720 GB
DATE : AUGUST 2000
D60 D75
D100 D102
OPERATION AND MAINTENANCE MANUAL
1090200
D102
SERIAL No:
–>>
1085120
D100
SERIAL No:
–>>
1080110
D75
SERIAL No:
–>>
1075080
D60
SERIAL No:
–>>
This manual contains
important safety information
and must be made available to
personnel who operate and
maintain this machine.
Manual Closed Out
Machine no longer in production
Summary of Contents for D100
Page 2: ......
Page 15: ...GENERAL INFORMATION 12 D60 D75 D100 D102 ECOCONTROL ECOCONTROL ...
Page 16: ...GENERAL INFORMATION 13 D60 D75 D100 D102 ECOCONTROL ECOCONTROL ...
Page 20: ...GENERAL INFORMATION 17 D60 D75 D100 D102 ECOMATIC ECOMATIC ...
Page 21: ...GENERAL INFORMATION 18 D60 D75 D100 D102 ECOMATIC ECOMATIC ...
Page 51: ......
Page 52: ......
Page 53: ...Printed in the United Kingdom ...