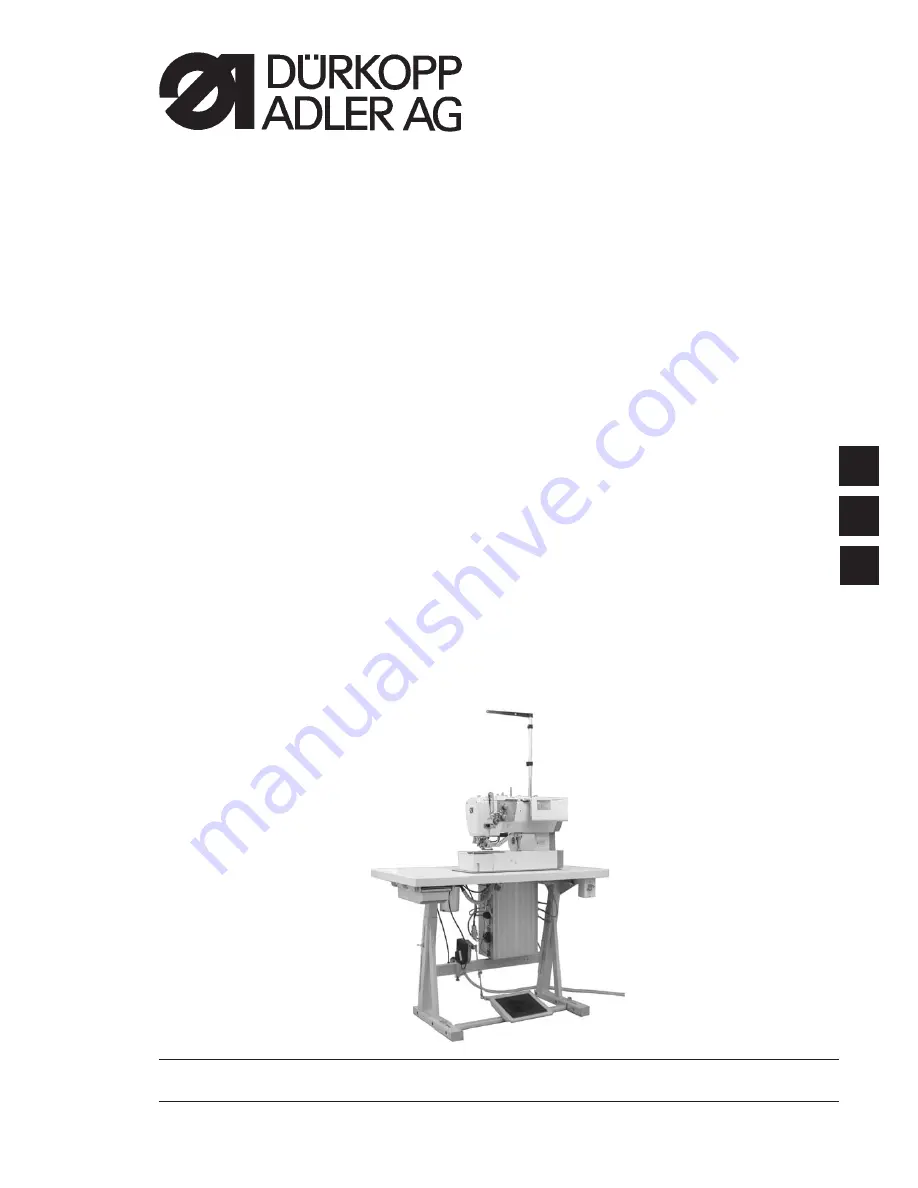
Manual, complete
540 - 100
CNC double lockstitch buttonholer
Operating Instructions
Installation Instructions
Service Instructions
Postfach 17 03 51, D-33703 Bielefeld • Potsdamer Straße 190, D-33719 Bielefeld
Phone + 49 (0) 5 21 / 9 25-00 •
Fax + 49 (0) 5 21 / 9 25 24 35 •
www.duerkopp-adler.com
1
2
3
Ausgabe / Edition: 04/2006
Printed in Federal Republic of Germany
Teile-Nr./Part.-No.: 0791 540001
Summary of Contents for 540 - 100
Page 40: ...Notes 36 ...