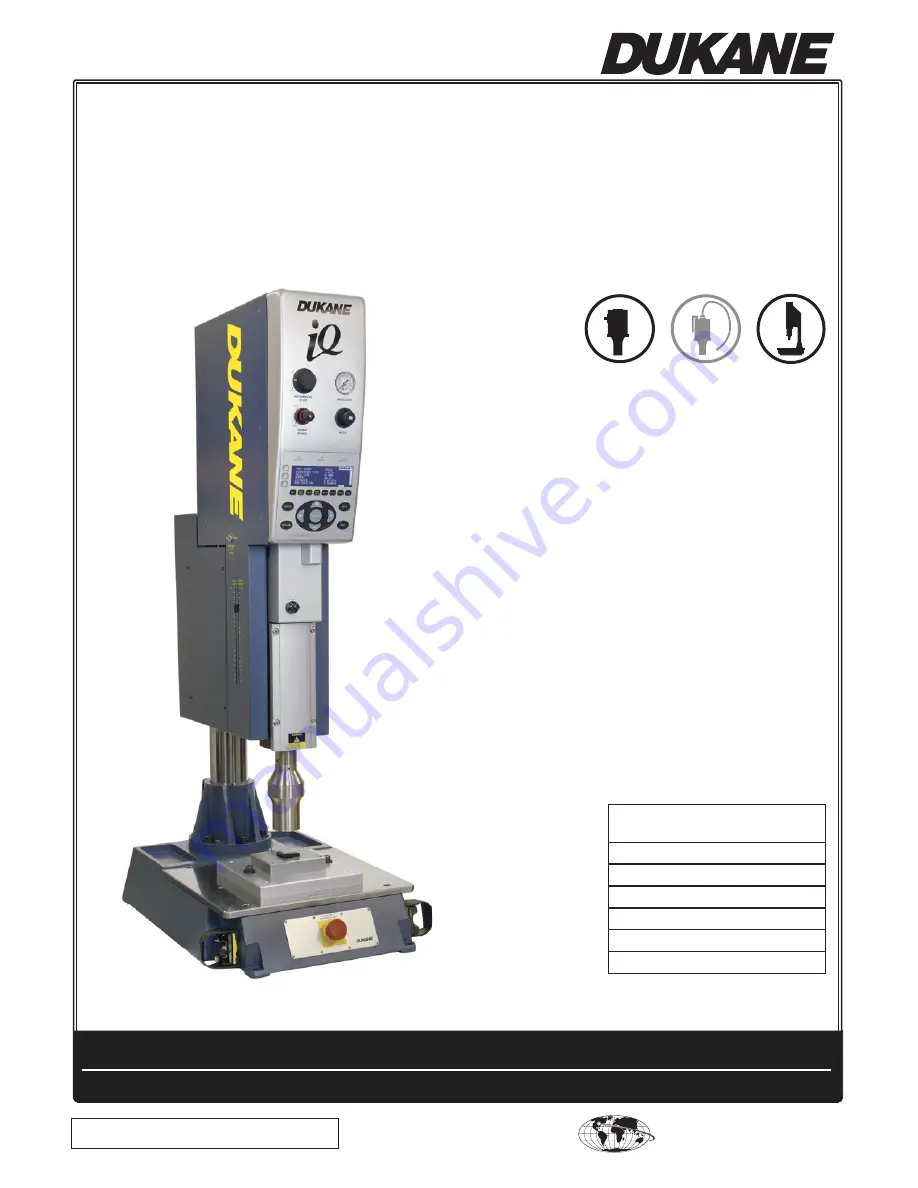
Intelligent Assembly Solutions
www.dukane.com/us
ISO 9001
Dukane products are manufactured
in ISO registered facilities
Dukane Intelligent Assembly Solutions • 2900 Dukane Drive • St. Charles, Illinois 60174 USA • TEL (630) 797–4900 • FAX (630) 797–4949
Dukane Part No. 403–594-02
iQ
Series
ULTRASONIC INTEGRATED PRESS SYSTEM
i 220
User's Manual
AUTOMATED
HAND PROBE
PRESS
This User's Manual
Covers These Models
20122XC0P3
20121XC0P3
20122XC0P5
20121XC0P5
20242XC0P3
20242XC0P5