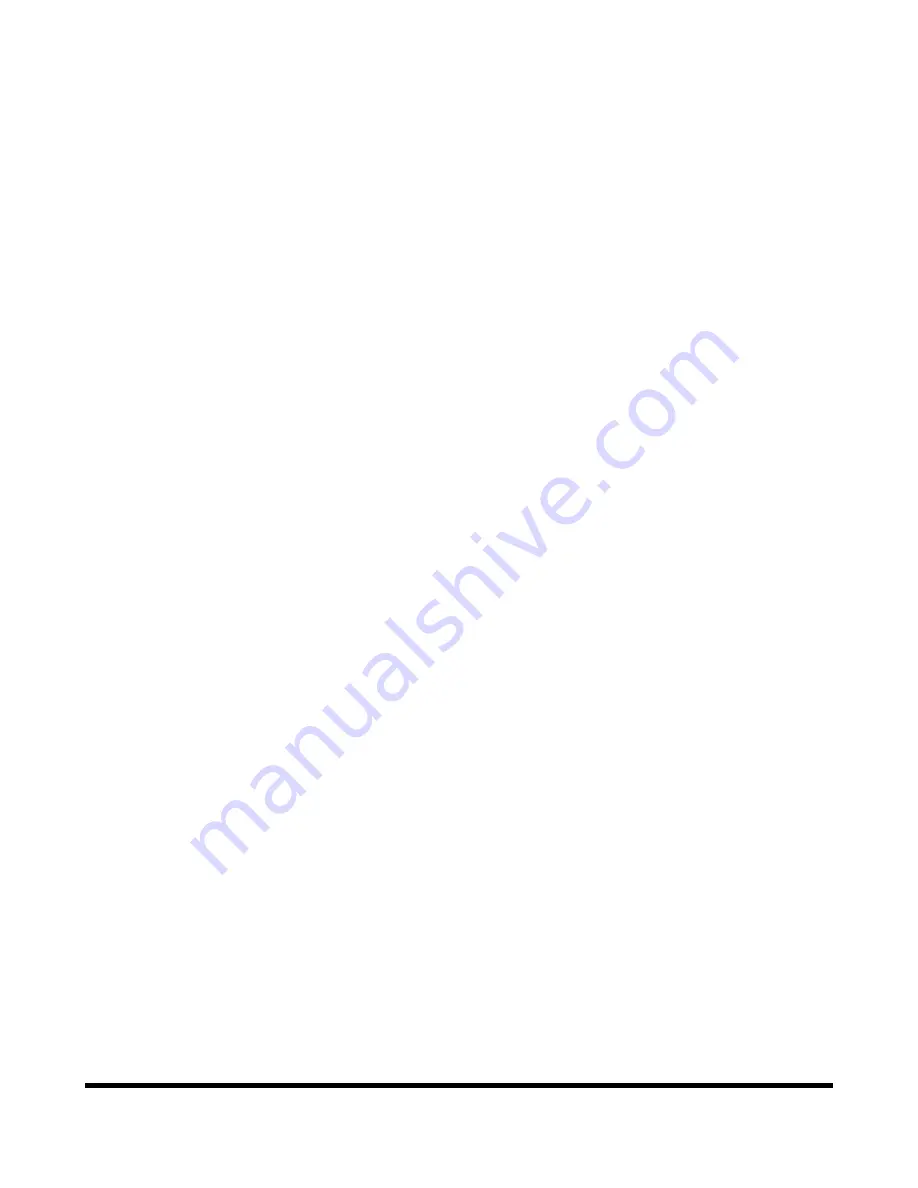
Copyright
Doosan
2006
K1028289E Operation and Maintenance Manual
DOOSAN
reserves the right to improve its products continuously, delivering the best possible product to
the marketplace. These improvements can be implemented at any time with no obligation to change
materials previously sold. It is recommended that consumers periodically contact their distributors for most
recent documentation on purchased equipment.
This documentation may include attachments and optional equipment not available in your machine's
package. Please call your distributor for additional items that you may require.
Illustrations used throughout this manual are used only as a representation of the actual piece of
equipment, and may vary from the actual item.
Operation and Maintenance Manual
K1028289E
Serial Number 5001 and Up
December 2006
DX27Z
Summary of Contents for DX27Z
Page 2: ......
Page 6: ...K1028289E Table of Contents IV ...
Page 58: ...OP000522 Safety 1 52 ...
Page 188: ...OP000524 Inspection Maintenance and Adjustment 4 60 ...