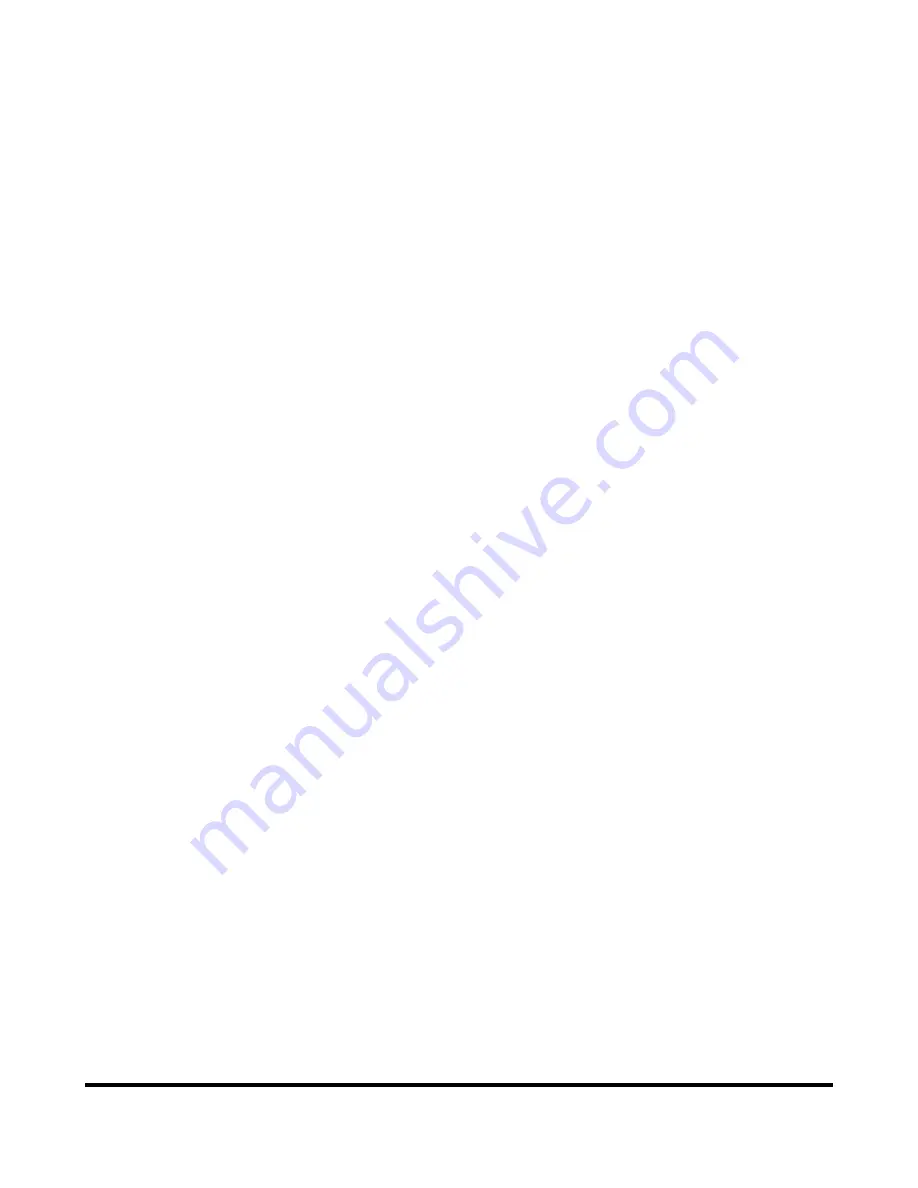
Copyright
Doosan
2006
K1024512E Operation and Maintenance Manual
DOOSAN
reserves the right to improve our products in a continuing process to provide the best possible product
to the market place. These improvements can be implemented at any time with no obligation to change materials
on previously sold products. It is recommended that consumers periodically contact their distributors for recent
documentation on purchased equipment.
This documentation may include attachments and optional equipment that is not available in your machine's
package. Please call your distributor for additional items that you may require.
Illustrations used throughout this manual are used only as a representation of the actual piece of equipment, and
may vary from the actual item.
Operation and Maintenance Manual
K1024512E
Serial Number 5001 and Up
September 2006
DX190W
Summary of Contents for DX190W
Page 2: ......
Page 71: ...OP000528 2 3 Operating Controls ...
Page 128: ...OP000528 Operating Controls 2 60 CD Player Optional AST DIR FG000109 Figure 135 ...
Page 196: ......
Page 292: ...OP000530 Inspection Maintenance and Adjustment 4 96 ...
Page 304: ...OP000440 6 8 Troubleshooting ...