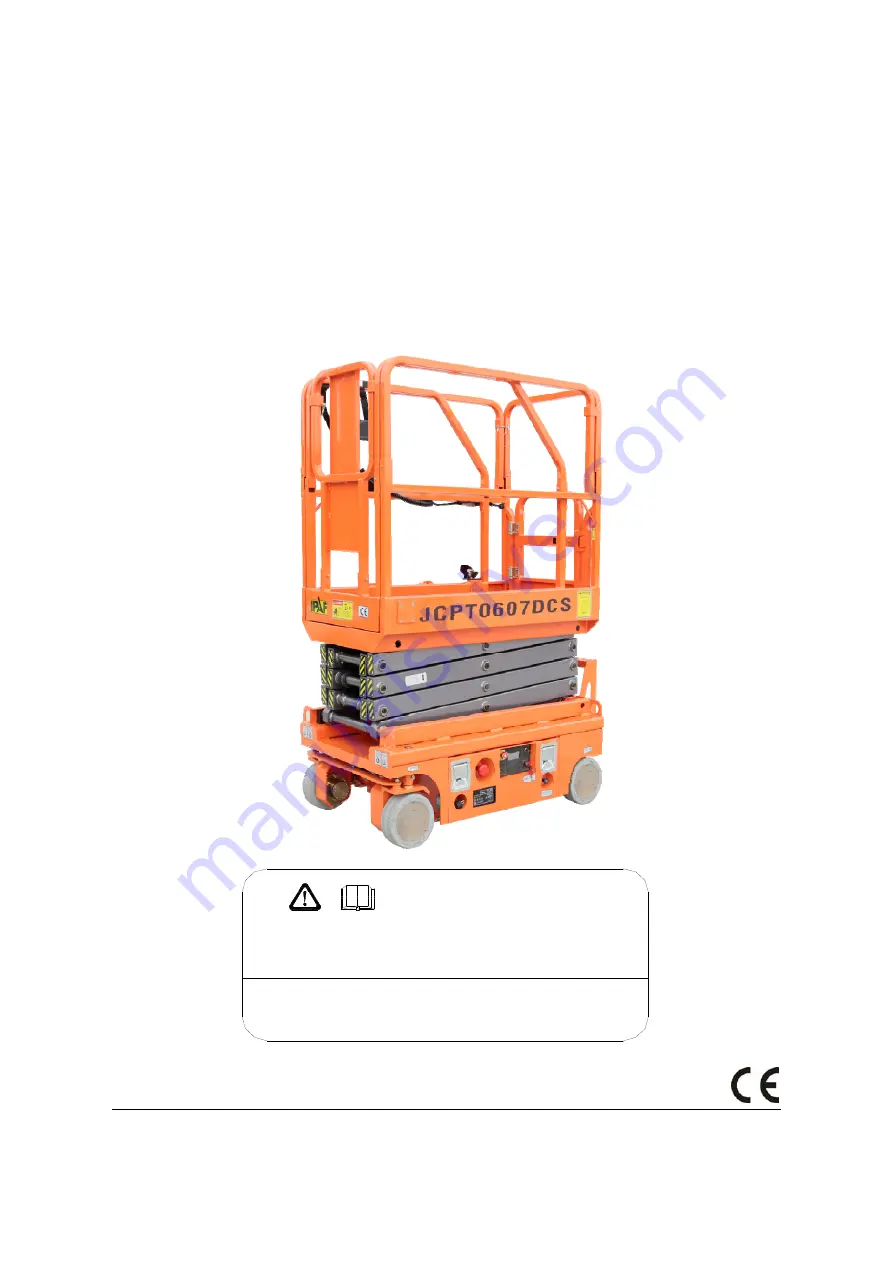
SELF-PROPELLED SCISSOR LIFTS
OPERATOR’S MANUAL
with Maintenance Information and Parts List
( For JCPT0607DCS )
Part Number: SM0115111
Zhejiang Dingli Machinery Co., Ltd.
First Edition, November 2015 Printing
WARNING
THE MANUFACTURER SHALL NOT BE HELD LIABLE IN CASE OF FAULTS
OR ACCIDENTS DUE TO NEGLIGENCE, INCAPACITY, INSTALLATION BY
UNQUALIFIED TECHNICIANS AND IMPROPER USE OF THE MACHINE
DO NOT OPERATE THIS MACHINE UNTIL YOU READ AND UNDERSTAND
ALL THE DANGERS,W ARNINGS AND CAUTIONS IN THIS MANUAL
Summary of Contents for JCPT0607DCS
Page 3: ......
Page 5: ......
Page 15: ...OPERATOR S MANUAL with Maintenance Information Decals 10 ...