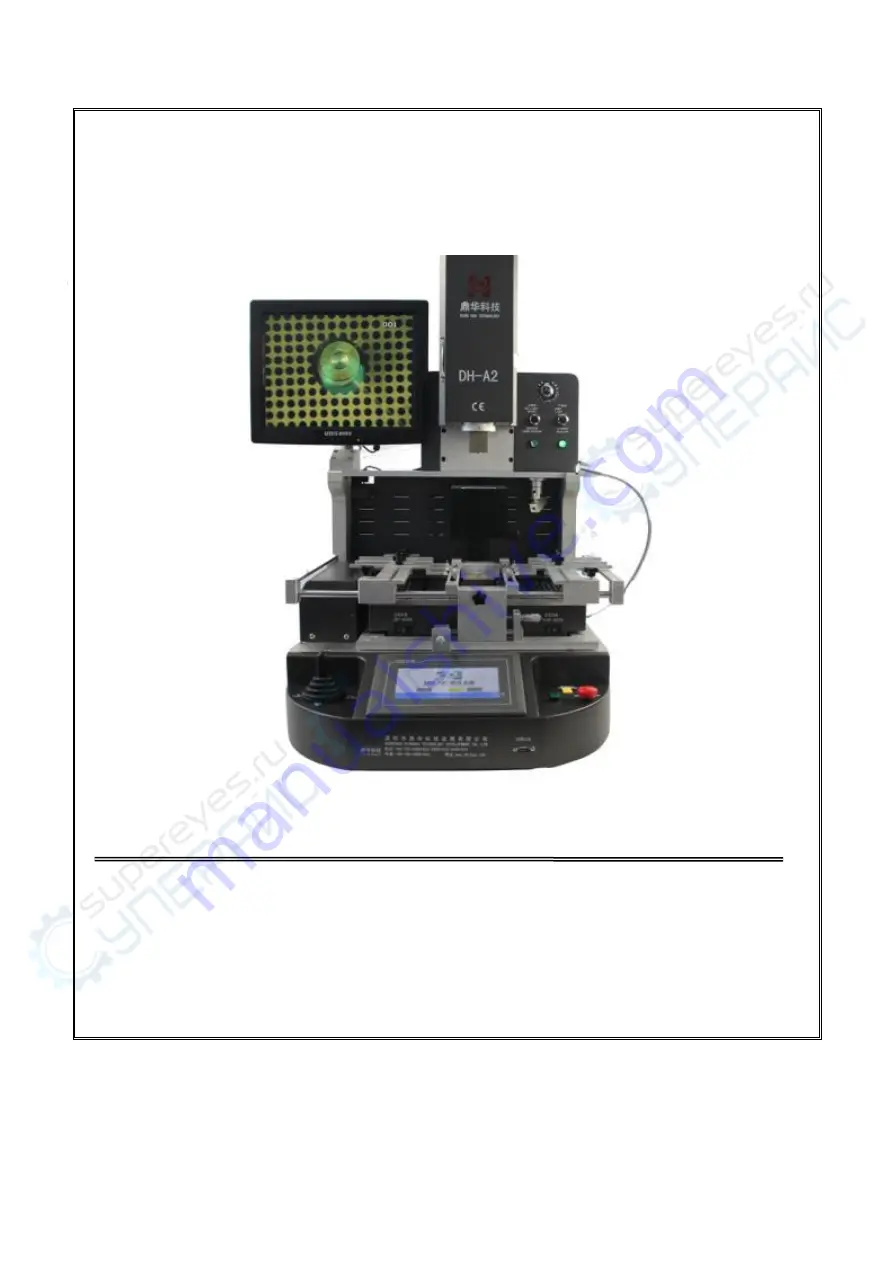
1
DH-A2 BGA Rework Station Manual
ADD:
4th Floor
,
Buliding 6B, Shengzuozhi Technoilogy Park
,
Bao’an District,
Xinqiao
,
Shajing Town, Bao’an District, Shenzhen, Guangdong
,
China
Tel:
0755-29091633/29091833
Fax:
0755-29091622
Website:
www.sinobga.com
E-mail:
深圳鼎华科技发展有限公司
Shenzhen Dinghua technology Development Co.,Ltd