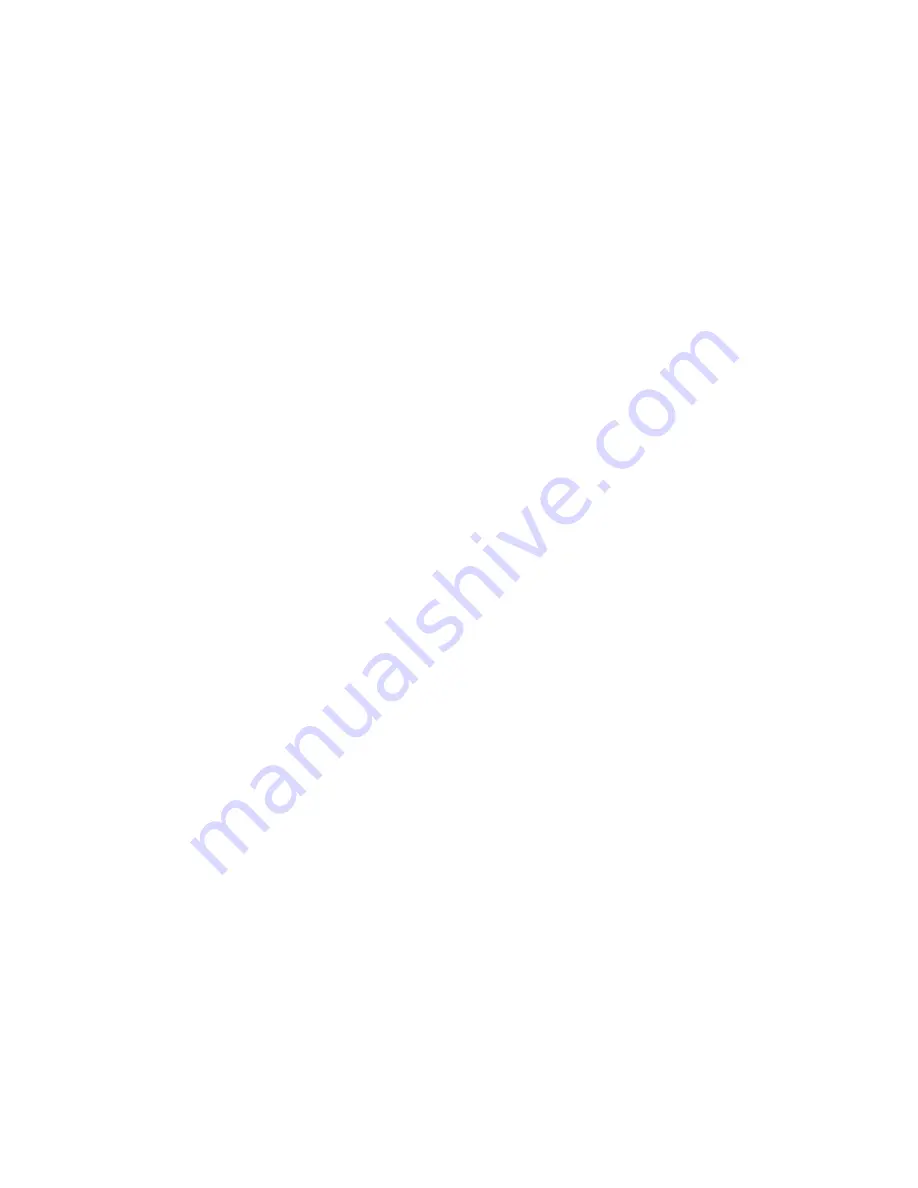
DG Flugzeugbau GmbH
Otto-Lilienthal-Weg 2 / Am Flugplatz
D-76646 Bruchsal
Germany
Postbox 1480, D-76604 Bruchsal
Deutschland
Tel. 07251/3020-100
Telefax 07251/3020-200
eMail: [email protected]
Spare part and material sales: Tel. 07251/3020-270
http://www.dg-flugzeugbau.de
M A I N T E N A N C E M A N U A L
F O R T H E
M O T O R G L I D E R
DG-808C
Type:
DG-800A
Model:
DG-808C
Data Sheet No.: EASA A.067 (LBA873)
Factory Serial No.:
__________________________
Registration No.:
__________________________
Date of issue:
June 2005
Issued: July 2017
Summary of Contents for DG-800A
Page 3: ...Maintenance Manual DG 808C Issued June 2005 0 2 This page was intentionally left blank...
Page 113: ......
Page 114: ......
Page 115: ......
Page 116: ......
Page 117: ......
Page 118: ......
Page 119: ......
Page 122: ......
Page 123: ......
Page 124: ......
Page 125: ......
Page 126: ......
Page 127: ......
Page 128: ......
Page 129: ......
Page 130: ......
Page 131: ......
Page 132: ......
Page 133: ......
Page 134: ......
Page 135: ......
Page 136: ......
Page 137: ......
Page 138: ......
Page 139: ......
Page 140: ......
Page 141: ......
Page 142: ......
Page 143: ......
Page 144: ......
Page 145: ......
Page 147: ......
Page 158: ......