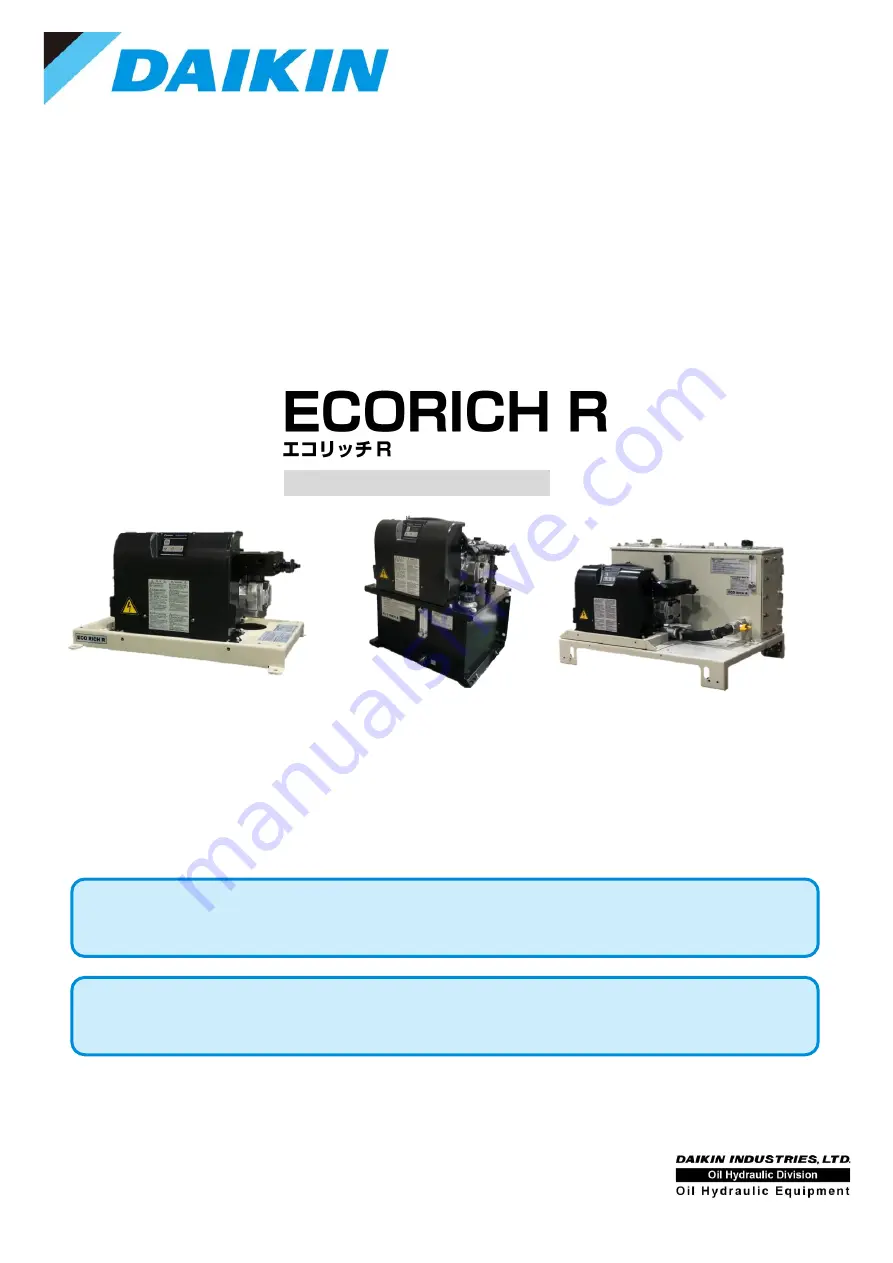
PIM00587
取扱説明書
Instruction Manual
H y b r i d H y d r a u l i c S y s t e m
Design #40 Series
EHU15R0700-40-03 / EHU15R0702-40 / EHU15R0703-40-03
EHU15R1000-40-03 / EHU15R1002-40 / EHU15R1003-40-03
EHU30R0700-40-03 / EHU30R0702-40 / EHU30R0703-40-03
日本語
................................................ JP-1
~
JP-97
English ........................................ EN-1 to EN-102