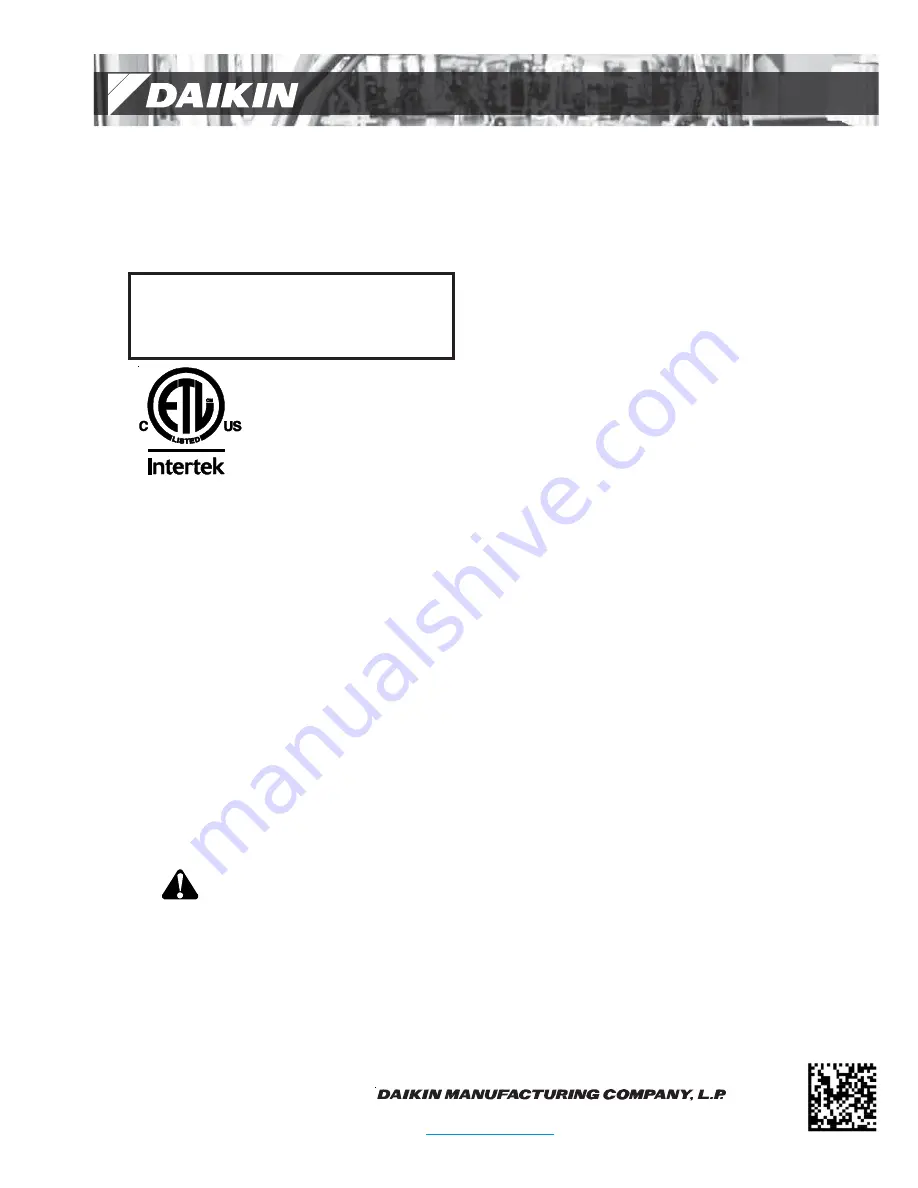
Our continuing commitment to quality products may mean a change in specifications without notice.
©
2014-2017
5151 San Felipe St., Suite 500, Houston, TX 77056
www.daikincomfort.com
DM96VC & DC96VC
T
WO
-S
TAGE
G
AS
F
URNACE
(Type FSP CATEGORY IV Direct
or Non Direct Vent Air Furnace)
These furnaces comply with requirements
embodied in the American National Standard /
National Standard of Canada ANSI Z21.47·CSA-
2.3 Gas Fired Central Furnaces.
Installer:
Affix all manuals
adjacent to the unit.
As a professional installer you have an obligation to know
the product better than the customer. This includes all safety
precautions and related items.
Prior to actual installation, thoroughly familiarize yourself
with this Instruction Manual. Pay special attention to all
safety warnings. Often during installation or repair it is
possible to place yourself in a position which is more
hazardous than when the unit is in operation.
Remember, it is your responsibility to install the product
safely and to know it well enough to be able to instruct a
customer in its safe use.
Safety is a matter of common sense...a matter of thinking
before acting. Most dealers have a list of specific good
safety practices...follow them.
The precautions listed in this Installation Manual are intended
as supplemental to existing practices. However, if there is
a direct conflict between existing practices and the content
of this manual, the precautions listed here take precedence.
RECOGNIZE THIS SYMBOL
AS A SAFETY PRECAUTION.
*
NOTE: Please contact your distributor or our website for
the applicable Specification Sheet referred to in this manual.
TABLE OF CONTENTS
SAFETY CONSIDERATIONS .................................... 3
S
HIPPING
I
NSPECTION
......................................... 4
E
LECTROSTATIC
D
ISCHARGE
(ESD) P
RECAUTIONS
................. 4
T
O
T
HE
I
NSTALLER
........................................... 5
PRODUCT DESCRIPTION ....................................... 5
F
EATURES
................................................... 5
PRODUCT APPLICATION ....................................... 5
LOCATION REQUIREMENTS & CONSIDERATIONS ........... 6
C
LEARANCES
AND
A
CCESSIBILITY
................................ 7
E
XISTING
F
URNACE
R
EMOVAL
.................................. 8
T
HERMOSTAT
L
OCATION
....................................... 8
C
OMBUSTION
& V
ENTILATION
A
IR
R
EQUIREMENTS
................ 8
INSTALLATION POSITIONS .................................... 9
HORIZONTAL APPLICATIONS & CONSIDERATIONS ......... 9
F
URNACE
S
USPENSION
......................................... 9
F
RONT
C
OVER
P
RESSURE
S
WITCH
T
UBE
L
OCATION
............... 9
D
RAIN
T
RAP
AND
L
INES
....................................... 9
L
EVELING
................................................... 9
A
LTERNATE
V
ENT
/F
LUE
AND
C
OMBUSTION
A
IR
C
ONNECTIONS
..... 9
A
LTERNATE
E
LECTRICAL
AND
G
AS
L
INE
C
ONNECTIONS
............ 10
D
RAIN
P
AN
................................................. 10
F
REEZE
P
ROTECTION
......................................... 10
PROPANE GAS/HIGH ALTITUDE INSTALLATIONS .......... 10
VENT/FLUE PIPE & COMBUSTION AIR PIPE ................ 11
D
UAL
C
ERTIFICATION
: N
ON
-D
IRECT
/D
IRECT
V
ENT
.............. 11
M
ATERIALS
AND
J
OINING
M
ETHODS
............................ 11
P
ROPER
V
ENT
/F
LUE
AND
C
OMBUSTION
A
IR
P
IPING
P
RACTICES
.... 12
T
ERMINATION
L
OCATIONS
..................................... 12
C
ANADIAN
V
ENT
P
IPE
& C
OMBUSTION
A
IR
P
IPE
R
EQUIREMENTS
... 13
S
TANDARD
F
URNACE
C
ONNECTIONS
............................ 13
V
ENT
/F
LUE
P
IPE
........................................... 13
C
OMBUSTION
A
IR
P
IPE
D
IRECT
V
ENT
I
NSTALLATION
...............13
N
ON
-D
IRECT
V
ENT
(S
INGLE
P
IPE
) P
IPING
..................... 15
V
ENT
/I
NTAKE
T
ERMINATIONS
F
OR
I
NSTALLATION
OF
M
ULTIPLE
D
IRECT
V
ENT
F
URNACES
.................... 17
C
ONCENTRIC
V
ENT
T
ERMINATION
.............................. 18
S
IDE
W
ALL
V
ENT
K
IT
....................................... 18
CONDENSATE DRAIN LINES & DRAIN TRAP ................ 18
G
ENERAL
D
RAIN
I
NFORMATION
................................ 18
F
IELD
S
UPPLIED
D
RAIN
...................................... 19
U
PFLOW
M
ODEL
I
NSTALLED
V
ERTICALLY
....................... 19
D
RAIN
E
XITING
R
IGHT
S
IDE
................................... 19
D
RAIN
E
XITING
L
EFT
S
IDE
.................................... 19
U
PFLOW
M
ODEL
I
NSTALLED
H
ORIZONTALLY
WITH
R
IGHT
S
IDE
D
OWN
............................... 19
U
PFLOW
MODEL
INSTALLED
HORIZONTALLY
WITH
LEFT
SIDE
DOWN
. 20
U
PFLOW
MODEL
INSTALLED
HORIZONTALLY
WITH
LEFT
SIDE
DOWN
-
A
LTERNATE
................................................. 20
INSTALLATION INSTRUCTIONS
IOD-2008F
2/2017