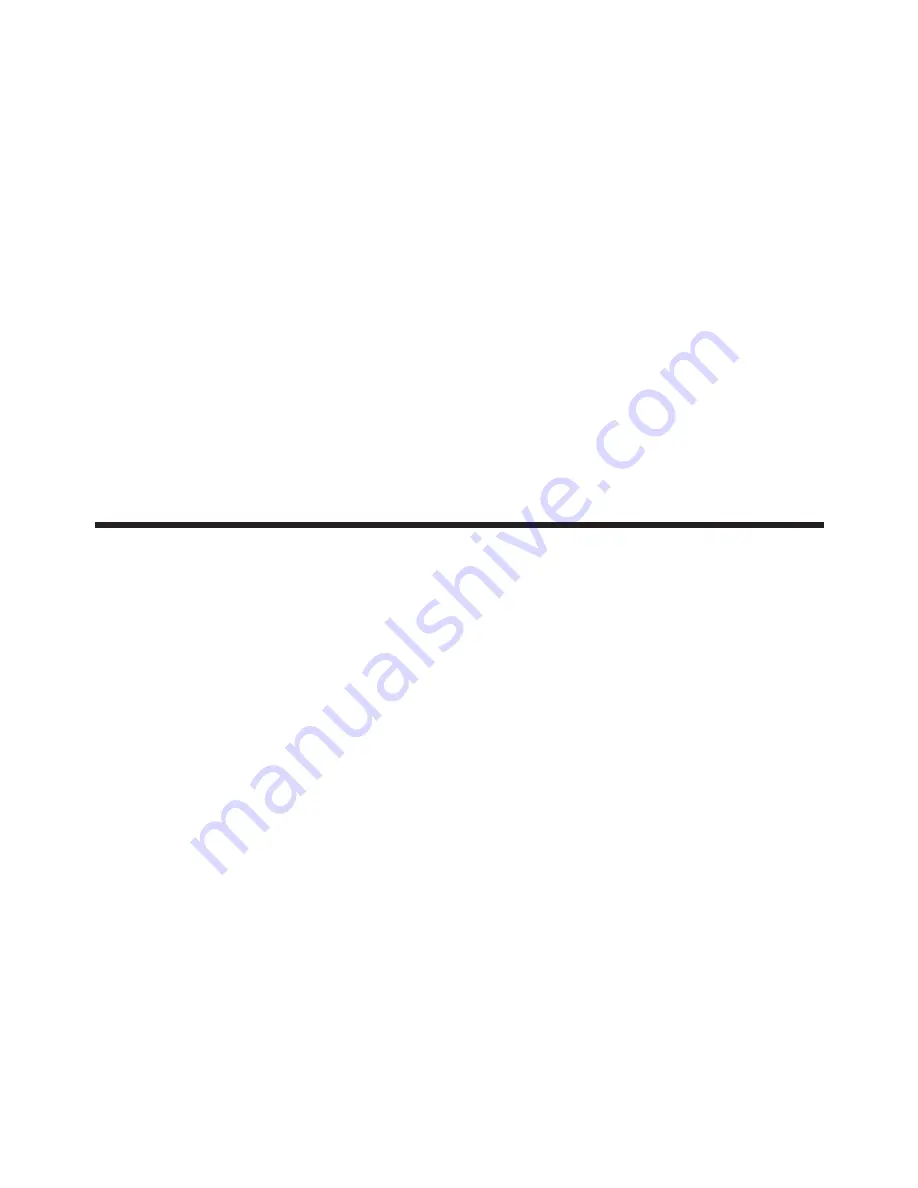
Operation &
Maintenance Manual
LIFT TRUCKS
D20S-3, D25S-3, D30S-3, D33S-3
G20E-3, G25E-3, G30E-3
GC20E-3, GC25E-3, GC30E-3
G20P-3, G25P-3, G30P-3, G33P-3
GC20P-3, GC25P-3, GC30P-3
D32S-3 (6,500lb@24"L.C.)
G32E-3 (6,500lb@24"L.C.)
G32P-3 (6,500lb@24"L.C.)
GC32E-3 (6,500lb@24"L.C.)
GC32P-3 (6,500lb@24"L.C.)
SB2302E06