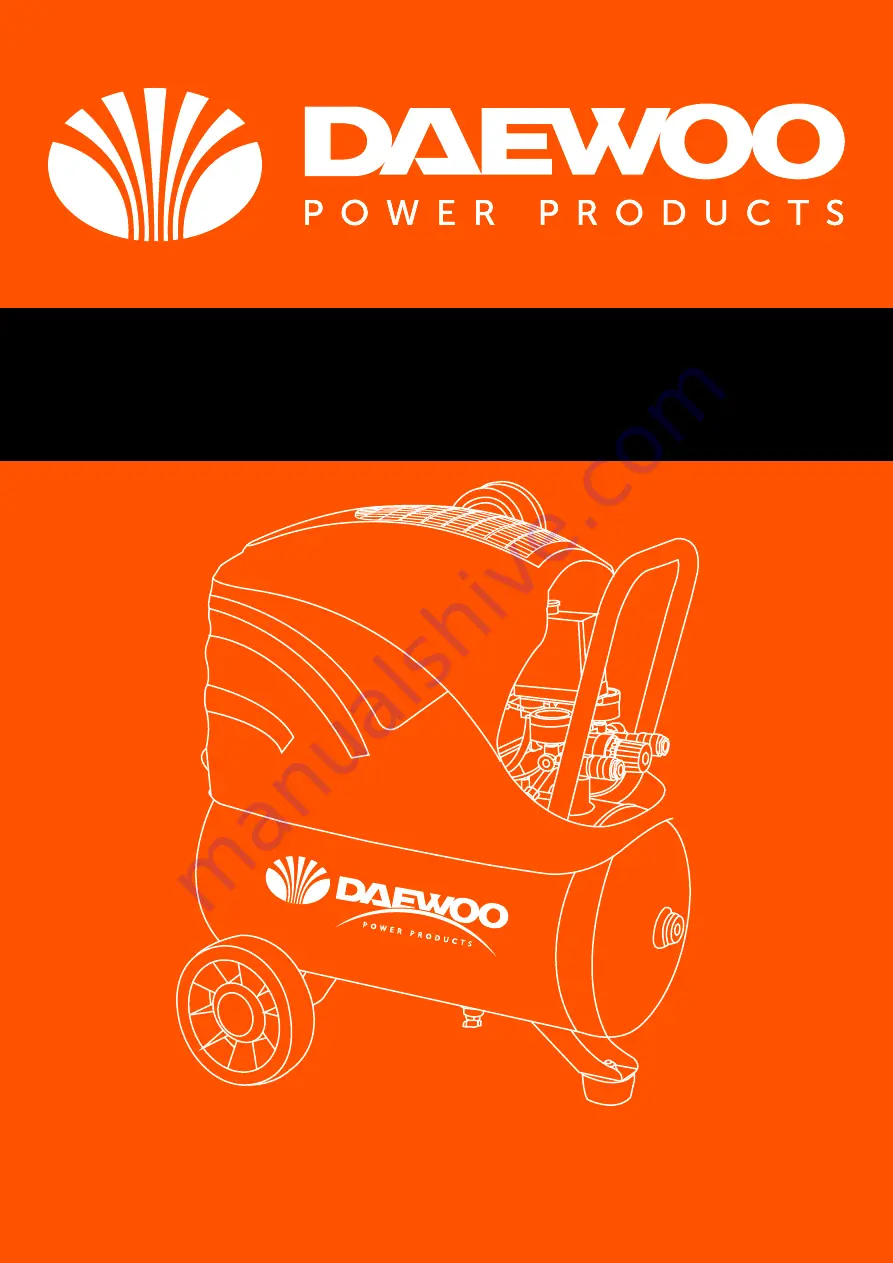
Manufactured under license of
Daewoo International Corporation
, Korea
www.daewoopowerproducts.com
USER'S MANUAL
DIRECT
AIR COMPRESSOR SERIES
1. PREPARATION FOR STARTING
(1) Air compressor should be placed in a clean, dry and ventilated area.
(2) In order to extend compressor lifespan ,reduce heat for moving parts by making sure this air
compressor cover must be at least 0.3~0.5 meters away from the wall.
(3) Keep voltage within±5% of rating
(4) Keep the oil level in the red circle leveler.
(5) Recommend compressor oil SAE30 or L-DAB 100 when temperature above 10
℃
, SAE10 or
L-DAB68 when temperature below 10
℃
.
(6) The normal temperature of working enviroment should be -5°c~35°c, and the altitude of the
working place should be 2000m below.
(7) The normal temperaure of compressor body is 180°c and the lubricating oil in the crankcase is
less than 70°c when the compressor is working.
(8) Open outlet valve and let air compressor compressor run 10 minutes without load before regular
operation
2. SAFETY GUIDELINES
DANGER-AN IMMEDIATE HAZARD THAT WILL CAUSE SERIOUS INJURY OR LOSS OF LIFE
(1).To reduce the risk of fire or explosion ,never spray flammable liquids in a confined area . It is
normal pressure switch to produce sparks while operating. If sparks come into contact with vapors
from gasoline or other solvents, they, may ignite causing fire or explosion, Always operate the com-
pressor in a well-ventilated area, Do not smoke while spraying. Do not spray where sparks or flame
are present, Keep compressor as far from spray area as possible.
(2).The solvents Trichloroethane and Methylene Chloride can chemically react with aluminum used
in paint spray guns, paint pumps, etc, and cause an explosion, If you are using these solvents, use
only stainless steel spray equipment, This does not affect your air compressor, but many affect the
equipment being used.
(3).Never directly use the compressed air produced by a compressor. It is not suitable for breathing
purposes.
3. WARNING-A POTENTIAL HAZARD THAT COULD CAUSE SERIOUS INJURY OR LOSS OF
LIFE.
(1).Do not weld on the air tank of this compressor. Welding on the air compressor tank strength and
cause an extremely hazardous condition. Welding on the tank in any manner will void the warranty
(2).Never use an electric air compressor outdoors when it is raining or on a wet surface, as it many
cause an electric shock.
(3).This unit starts automatically. Always shut off the compressor,
remove the plug from the outlet, and emptying all pressure from the system before servicing the
compressor, and when the compressor is not in use.
(4).Check the manufacture s maximum pressure rating for air tools and accessories. Compressor
outlet pressure must be regulated so as to never exceed the maximum pressure rating of the tool.
(5).High temperatures and moving parts are present under the protection cover.
To prevent burns or other injuries, Do not operate with the protection cover removed. Do not allow
the compressor parts to cool before handling or servicing.
(6).Be certain to read all labels when you are spraying paints or toxic materials and follow the safety
instructions. Use a respirator mask if there is a chance of inhaling anything you are spraying, Read
all instructions and be sure that your respirator mask will protect you.
(7).Always wear safety goggles or glasses when using an air compressor. Never point any nozzle or
sprayer toward a person or any part of the body.
(8).Do not adjust the pressure switch or relief valve for any reason, Doing so voids all warranties,
They have been preset at the factory for the maximum pressure of this unit.
4.CAUTION-A POTENTIALL HAZARD THAT MAY CAUSE MODEFATE INJURY OR DAMAGE TO
EQUIPMENT.
(1).Drain the mositure from the tank on a daily basis. A clean, dry tank will help prevent corrosion.
(2).Pull the pressure relief valve ring daily to ensure that the valve is functioning properly, and to
clear the valve of any possible(bstructions.
(3).To provide proper ventilation for cooling, the compressor must be kept a minimum of 31cm(12
inches)form the nearest wall, in a well-ventilated area.
(4).Fasten the compressor down securely if transporting is necessary, Pressure must be released
from the tank before transporting
(5).Protect the air hose and electric cord from damage and puncture. Inspect them weekly for weak
or worn spots and replace if necessary.
5.APPLICATION
The compressors are widely used in various pneumatic tools and machine of communication,
machinery manufacture, medical and health, garments, spinning and weaving works, such as tyre,
gas-filled, painting etc.
6. GENERAL VIEW AND MAIN COMPONENTS