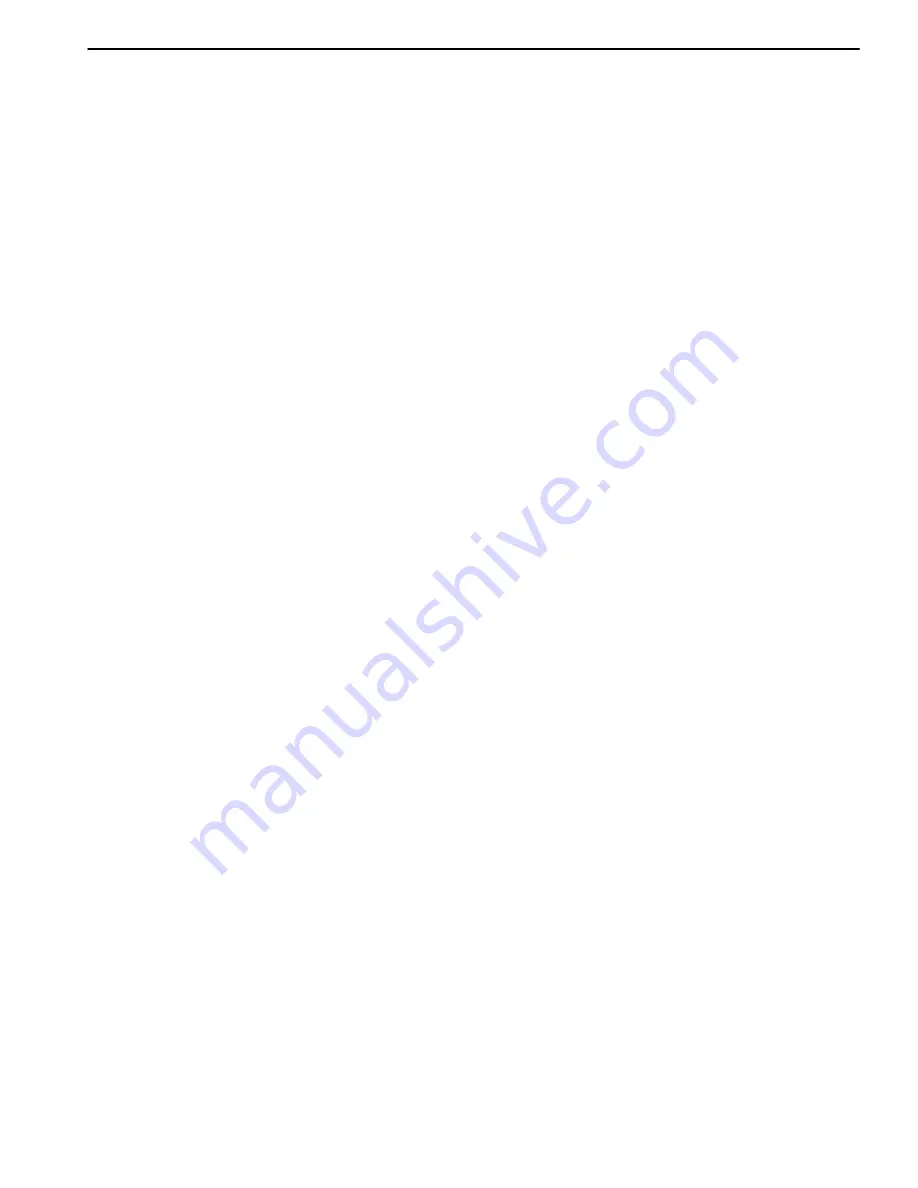
DAEWOO T-154 BL2,3
SECTION 1
ENGINE
CIELO EURO III
SECTION 1A
GENERAL ENGINE INFORMATION
TABLE OF CONTENTS
Diagnosis
1A-1
. . . . . . . . . . . . . . . . . . . . . . . . . . . . . . . . .
Compression Test
1A-1
. . . . . . . . . . . . . . . . . . . . . . . . .
Oil Pressure Test
1A-2
. . . . . . . . . . . . . . . . . . . . . . . . . .
Oil Leak Diagnosis
1A-3
. . . . . . . . . . . . . . . . . . . . . . . .
Knock Diagnosis
1A-4
. . . . . . . . . . . . . . . . . . . . . . . . . .
Noise Diagnosis
1A-8
. . . . . . . . . . . . . . . . . . . . . . . . . . .
General Information
1A-11
. . . . . . . . . . . . . . . . . . . . . . .
Cleanliness and Care
1A-11
. . . . . . . . . . . . . . . . . . . . .
On-Engine Service
1A-11
. . . . . . . . . . . . . . . . . . . . . . .
DIAGNOSIS
COMPRESSION TEST
Important:
Disconnect the Crankshaft Position (CKP)
Sensor connector to disable the fuel and the ignition
systems.
Test the compression pressure for each cylinder. Low
compression pressure may be the fault of the valves or
the pistons. The following conditions should be consid-
ered when you check the cylinder compression:
D
The engine should be at normal operating tempera-
ture.
D
The throttle must be wide open.
D
All the spark plugs should be removed.
D
The battery must be at or near full charge.
1. Place approximately three squirts of oil from a plung-
er-type oiler into each spark plug port.
2. Insert the engine compression gauge into each spark
plug port.
3. Crank test each cylinder with four to five compression
strokes using the starter motor.
4. The lowest reading should not be less than 70% of
the highest reading. The compression gauge reading
should not be less than 689 kPa (100 psi) for any of
the cylinders.
5. Examine the gauge readings obtained after the four
‘‘puffs’’ per cylinder are obtained from cranking the
starter motor. The readings are explained in the follow-
ing descriptions:
D
Normal Condition – Compression builds up quickly
and evenly to the specified compression on each cylin-
der.
D
Piston Rings Faulty – Compression is low on the first
stroke and tends to build up on following strokes, but
the compression pressure does not reach normal. The
compression pressure improves considerably with the
addition of oil into the cylinder.
D
Valves Faulty – Low compression pressure on the
first stroke. The compression pressure does not tend
to build up on the following strokes. The compression
pressure does not improve much with the addition of
oil into the cylinder.
Summary of Contents for CIELO EURO III
Page 12: ...DAEWOO T 154 BL2 3 BLANK...
Page 20: ...1B 8 SOHC ENGINE MECHANICAL DAEWOO T 154 BL2 3 COMPONENT LOCATOR UPPER END A402B001...
Page 22: ...1B 10 SOHC ENGINE MECHANICAL DAEWOO T 154 BL2 3 LOWER END A202B006...
Page 128: ...DAEWOO T 154 BL2 3 BLANK...
Page 131: ......
Page 132: ...1E 4 ENGINE ELECTRICAL DAEWOO T 154 BL2 3 A402E002 CHARGING SYSTEM...
Page 180: ...1F 12 ENGINE CONTROLS DAEWOO T 154 BL2 3 TAA1F020 ECM WIRING DIAGRAM 1 5L SOHC 2 OF 6...
Page 181: ...ENGINE CONTROLS 1F 13 DAEWOO T 154 BL2 3 ECM WIRING DIAGRAM 1 5L SOHC 3 OF 6...
Page 182: ...1F 14 ENGINE CONTROLS ECM WIRING DIAGRAM 1 5L SOHC 4 OF 6...
Page 183: ...ENGINE CONTROLS 1F 15 DAEWOO T 154 BL2 3 ECM WIRING DIAGRAM 1 5L SOHC 5 OF 6...
Page 184: ...ENGINE CONTROLS 1F 16 DAEWOO T 154 BL2 3 ECM WIRING DIAGRAM 1 5L SOHC 6 OF 6...
Page 190: ...ENGINE CONTROLS 1F 22 DAEWOO T 154 BL2 3 BLANK...
Page 191: ...1F 23 ENGINE CONTROLS DAEWOO T 154 BL2 3 COMPONENT LOCATOR COMPONENT LOCATOR SOHC...
Page 195: ...DAEWOO T 154 BL2 3 BLANK...
Page 196: ...1F 28 ENGINE CONTROLS DAEWOO T 154 BL2 3 TTA1F250...
Page 199: ...ENGINE CONTROLS 1F 31 DAEWOO T 154 BL2 3 BLANK...
Page 203: ...ENGINE CONTROLS 1F 35 DAEWOO T 154 BL2 3 BLANK...
Page 204: ...1F 36 ENGINE CONTROLS DAEWOO T 154 BL2 3 TAA1F240...
Page 205: ...ENGINE CONTROLS 1F 37 DAEWOO T 154 BL2 3 TAA1F260...
Page 213: ...ENGINE CONTROLS 1F 45 DAEWOO T 154 BL2 3 BLANK...
Page 214: ...1F 46 ENGINE CONTROLS DAEWOO T 154 BL2 3 TAA1F230...
Page 218: ...1F 50 ENGINE CONTROLS DAEWOO T 154 BL2 3 TAB1F230...
Page 223: ...ENGINE CONTROLS 1F 55 DAEWOO T 154 BL2 3 BLANK...
Page 227: ...ENGINE CONTROLS 1F 59 DAEWOO T 154 BL2 3 BLANK...
Page 233: ...ENGINE CONTROLS 1F 65 DAEWOO T 154 BL2 3 BLANK...
Page 234: ...1F 66 ENGINE CONTROLS DAEWOO T 154 BL2 3 TAA1F240...
Page 249: ...ENGINE CONTROLS 1F 81 DAEWOO T 154 BL2 3 BLANK...
Page 250: ...1F 82 ENGINE CONTROLS DAEWOO T 154 BL2 3 TAA1F250...
Page 253: ...ENGINE CONTROLS 1F 85 DAEWOO T 154 BL2 3 BLANK...
Page 255: ...ENGINE CONTROLS 1F 87 DAEWOO T 154 BL2 3 BLANK...
Page 259: ...ENGINE CONTROLS 1F 90 DAEWOO T 154 BL2 3 BLANK...
Page 263: ...ENGINE CONTROLS 1F 94 DAEWOO T 154 BL2 3 BLANK...
Page 269: ...ENGINE CONTROLS 1F 100 DAEWOO T 154 BL2 3 BLANK...
Page 275: ...ENGINE CONTROLS 1F 106 DAEWOO T 154 BL2 3 BLANK...
Page 279: ...ENGINE CONTROLS 1F 110 DAEWOO T 154 BL2 3 BLANK...
Page 287: ...ENGINE CONTROLS 1F 118 DAEWOO T 154 BL2 3 BLANK...
Page 293: ...ENGINE CONTROLS 1F 124 DAEWOO T 154 BL2 3 BLANK...
Page 299: ...ENGINE CONTROLS 1F 130 DAEWOO T 154 BL2 3 BLANK...
Page 305: ...ENGINE CONTROLS 1F 136 DAEWOO T 154 BL2 3 BLANK...
Page 311: ...ENGINE CONTROLS 1F 142 DAEWOO T 154 BL2 3 BLANK...
Page 319: ...ENGINE CONTROLS 1F 150 DAEWOO T 154 BL2 3 BLANK...
Page 323: ...ENGINE CONTROLS 1F 154 DAEWOO T 154 BL2 3 BLANK...
Page 335: ...ENGINE CONTROLS 1F 166 DAEWOO T 154 BL2 3 BLANK...
Page 339: ...ENGINE CONTROLS 1F 170 DAEWOO T 154 BL2 3 BLANK...
Page 343: ...ENGINE CONTROLS 1F 174 DAEWOO T 154 BL2 3 BLANK...
Page 347: ...ENGINE CONTROLS 1F 178 DAEWOO T 154 BL2 3 BLANK...
Page 355: ...ENGINE CONTROLS 1F 186 DAEWOO T 154 BL2 3 BLANK...
Page 368: ...1F 199 ENGINE CONTROLS DAEWOO T 154 BL2 3 FAA1F210...
Page 371: ...ENGINE CONTROLS 1F 202 DAEWOO T 154 BL2 3 BLANK...
Page 372: ...1F 203 ENGINE CONTROLS DAEWOO T 154 BL2 3 FAA1F210...
Page 375: ...ENGINE CONTROLS 1F 206 DAEWOO T 154 BL2 3 BLANK...
Page 376: ...1F 207 ENGINE CONTROLS DAEWOO T 154 BL2 3 FAA1F210...
Page 379: ...ENGINE CONTROLS 1F 210 DAEWOO T 154 BL2 3 BLANK...
Page 380: ...1F 211 ENGINE CONTROLS DAEWOO T 154 BL2 3 FAA1F210...
Page 383: ...ENGINE CONTROLS 1F 214 DAEWOO T 154 BL2 3 BLANK...
Page 384: ...1F 215 ENGINE CONTROLS DAEWOO T 154 BL2 3 FAA1F220...
Page 389: ...ENGINE CONTROLS 1F 220 DAEWOO T 154 BL2 3 BLANK...
Page 390: ...1F 221 ENGINE CONTROLS DAEWOO T 154 BL2 3 FAA1F220...
Page 395: ...ENGINE CONTROLS 1F 224 DAEWOO T 154 BL2 3 BLANK...
Page 396: ...1F 225 ENGINE CONTROLS DAEWOO T 154 BL2 3 FAA1F220...
Page 401: ...ENGINE CONTROLS 1F 230 DAEWOO T 154 BL2 3 BLANK...
Page 402: ...1F 231 ENGINE CONTROLS DAEWOO T 154 BL2 3 FAA1F220...
Page 407: ...ENGINE CONTROLS 1F 237 DAEWOO T 154 BL2 3 BLANK...
Page 408: ...1F 238 ENGINE CONTROLS DAEWOO T 154 BL2 3 FAA1F220...
Page 413: ...ENGINE CONTROLS 1F 243 DAEWOO T 154 BL2 3 BLANK...
Page 417: ...ENGINE CONTROLS 1F 247 DAEWOO T 154 BL2 3 BLANK...
Page 423: ...ENGINE CONTROLS 1F 253 DAEWOO T 154 BL2 3 BLANK...
Page 427: ...ENGINE CONTROLS 1F 257 DAEWOO T 154 BL2 3 BLANK...
Page 433: ...ENGINE CONTROLS 1F 263 DAEWOO T 154 BL2 3 BLANK...
Page 437: ...ENGINE CONTROLS 1F 267 DAEWOO T 154 BL2 3 BLANK...
Page 441: ...ENGINE CONTROLS 1F 271 DAEWOO T 154 BL2 3 BLANK...
Page 442: ...1F 272 ENGINE CONTROLS DAEWOO T 154 BL2 3 TAA1F240...
Page 445: ...ENGINE CONTROLS 1F 275 DAEWOO T 154 BL2 3 BLANK...
Page 446: ...1F 276 ENGINE CONTROLS DAEWOO T 154 BL2 3 TAA1F240...
Page 449: ...ENGINE CONTROLS 1F 279 DAEWOO T 154 BL2 3 BLANK...
Page 453: ...ENGINE CONTROLS 1F 283 DAEWOO T 154 BL2 3 BLANK...
Page 457: ...ENGINE CONTROLS 1F 287 DAEWOO T 154 BL2 3 BLANK...
Page 461: ...ENGINE CONTROLS 1F 291 DAEWOO T 154 BL2 3 BLANK...
Page 469: ...ENGINE CONTROLS 1F 299 DAEWOO T 154 BL2 3 BLANK...
Page 470: ...1F 300 ENGINE CONTROLS DAEWOO T 154 BL2 3 TAA1F290...
Page 474: ...1F 304 ENGINE CONTROLS DAEWOO T 154 BL2 3 TAA1F290...
Page 478: ...1F 308 ENGINE CONTROLS DAEWOO T 154 BL2 3 TAA1F290...
Page 482: ...1F 312 ENGINE CONTROLS DAEWOO T 154 BL2 3 TAA1F290...
Page 486: ...1F 316 ENGINE CONTROLS DAEWOO T 154 BL2 3 TAA1F290...
Page 493: ...ENGINE CONTROLS 1F 323 DAEWOO T 154 BL2 3 BLANK...
Page 513: ...ENGINE CONTROLS 1F 343 DAEWOO T 154 BL2 3 BLANK...
Page 517: ...ENGINE CONTROLS 1F 347 DAEWOO T 154 BL2 3 BLANK...
Page 521: ...ENGINE CONTROLS 1F 351 DAEWOO T 154 BL2 3 BLANK...
Page 527: ...DAEWOO T 154 BL2 3 BLANK...
Page 557: ...ENGINE CONTROLS 1F 387 DAEWOO T 154 BL2 3...