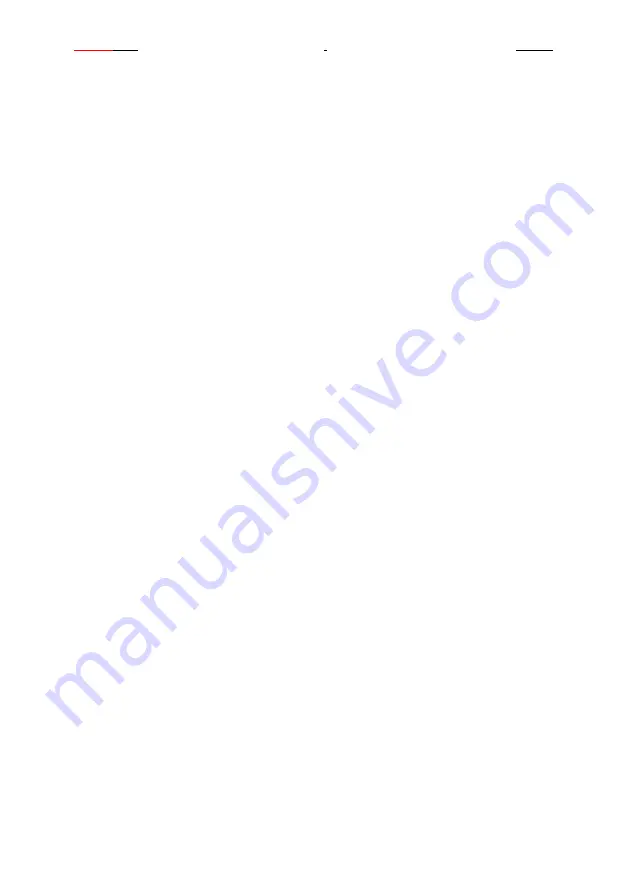
Cynko
Met
T-169
Page
1
CynkoMet Sp. z o.o.
ul. Fabryczna 7 W
16-020 Czarna Białostocka
phone (085) 710 24 56
TWO-AXLE TRACTOR TRAILER
THREE-WAY TIPPER
T-169/1
T-169/2
INSTRUCTIONS FOR USE AND OPERATION
Identification of the machine
Symbol/Type T-169/....
Serial number:…………………………….
The serial number is stamped on the rating plate and on the front
beam of the lower frame of the trailer. The rating plate is riveted
to the front beam of the upper frame.
When buying the trailer, check the conformity of the serial
number stamped on the trailer with the serial number given in the
warranty card, in the sales documents and in the instruction
manual.
Summary of Contents for T-169/1
Page 28: ...CynkoMet T 169 Page 28 Figure 4 Distribution of stickers...
Page 83: ...CynkoMet T 169 Page 83 Fig 20 Lubrication diagram...
Page 98: ...CynkoMet T 169 Page 98...
Page 99: ...CynkoMet T 169 Page 99 Spare parts catalogue...
Page 100: ...CynkoMet T 169 Page 100...
Page 104: ...CynkoMet T 169 Page 104 Chassis...
Page 106: ...CynkoMet T 169 Page 106 Push torsion system...
Page 108: ...CynkoMet T 169 Page 108 Rear spring suspension...
Page 110: ...CynkoMet T 169 Page 110 Front spring suspension...
Page 112: ...CynkoMet T 169 Page 112 Upper frame...
Page 114: ...CynkoMet T 169 Page 114 Rear closure...
Page 116: ...CynkoMet T 169 Page 116 Closure flexible connector...
Page 118: ...CynkoMet T 169 Page 118 Walls set...
Page 120: ...CynkoMet T 169 Page 120 Rear wall...
Page 122: ...CynkoMet T 169 Page 122 Extensions set...
Page 124: ...CynkoMet T 169 Page 124 Hydraulic installation...
Page 126: ...CynkoMet T 169 Page 126 Hydraulic installation continued...
Page 128: ...CynkoMet T 169 Page 128 Single cable pneumatic installation...
Page 130: ...CynkoMet T 169 Page 130 Single cable pneumatic installation continued...
Page 132: ...CynkoMet T 169 Page 132 Hand brake...
Page 134: ...CynkoMet T 169 Page 134 Tarpaulin frame...
Page 136: ...CynkoMet T 169 Page 136 Tarpaulin...
Page 138: ...CynkoMet T 169 Page 138 Electrical installation...
Page 140: ...CynkoMet T 169 Page 140 Hanger protection of the lighting...
Page 142: ...CynkoMet T 169 Page 142 Spare wheel hanger...
Page 144: ...CynkoMet T 169 Page 144 NOTES...