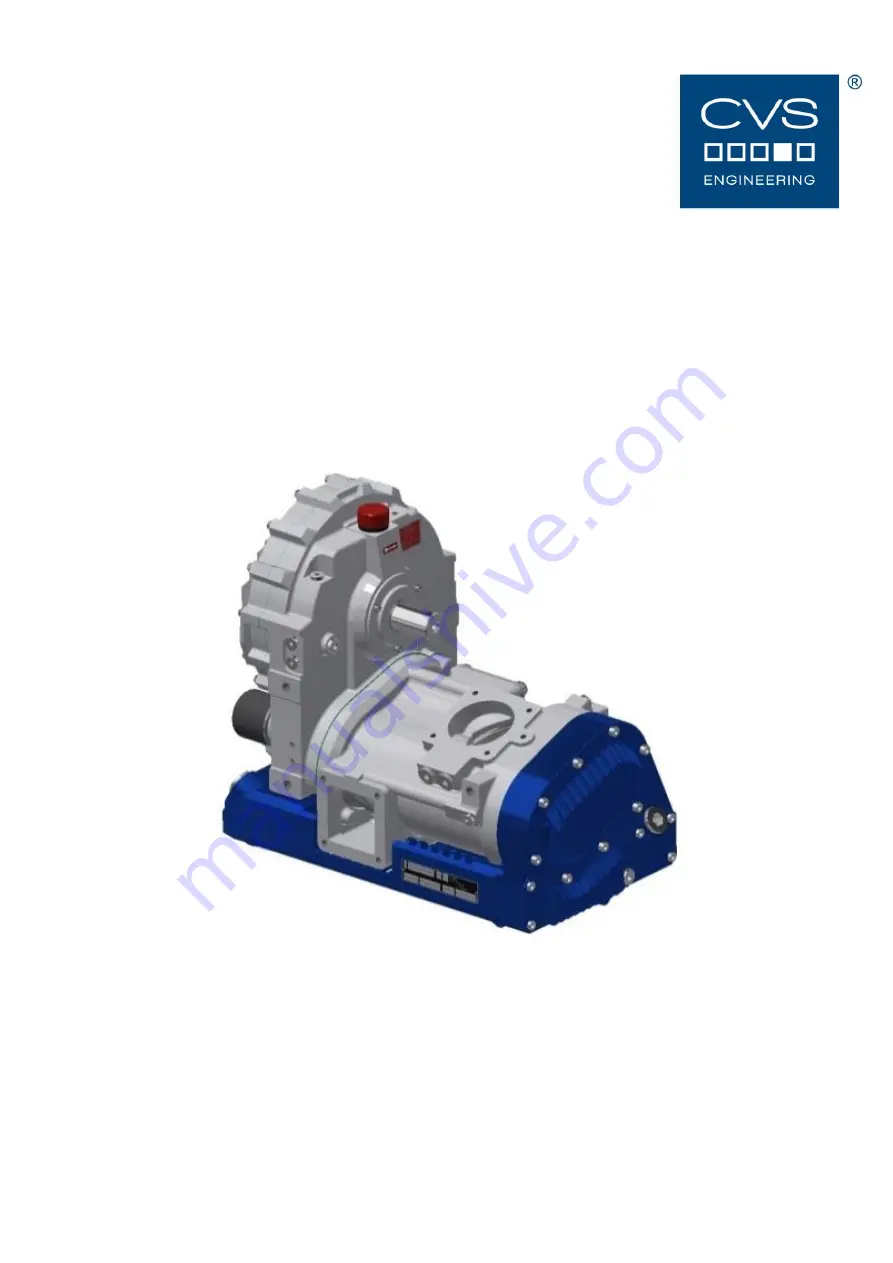
Contents
Assembly instructions
Screw compressor
SKL 1200 C
Doc-ID: 5113 / MA / EN
Release: Rev. 01 / 29/03/2019
Prior to installing the SKL 1200 C and putting it into operation you must have read and understood
these instructions. These instructions are only valid together with the operating instructions, they do
not replace them!
Summary of Contents for SKL 1200 C
Page 32: ......