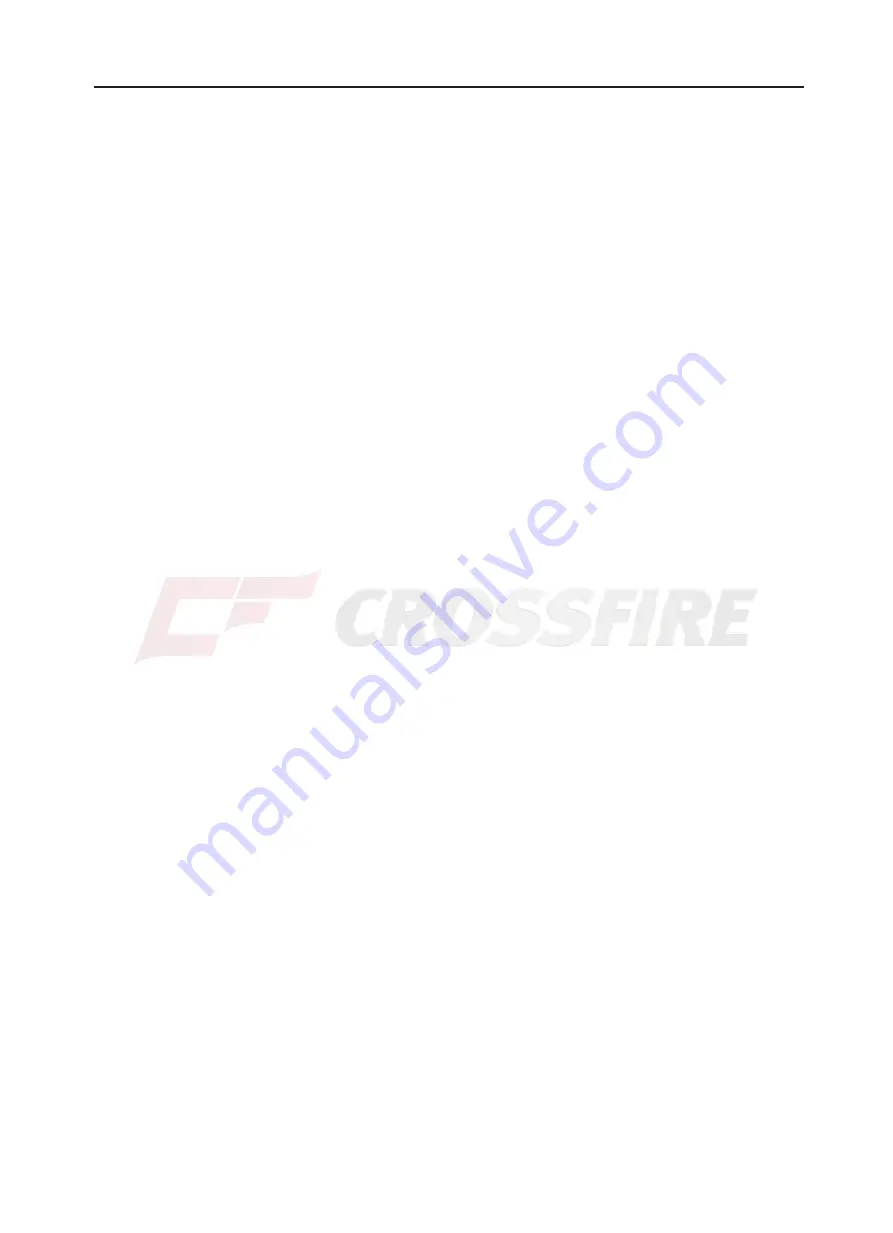
FOREWORD
Brief introduction to maintenance handbook of
HS1000UTV/HS900UTV/HS800UTV-5
The handbook is edited by Technical Center of Chongqing Huansong Science And
Technology Industrial Co.,Ltd, and is supplied to dealers and technicians as document of
technique.Mainly, the handbook gives methods to check, maintain and repair utility terrain
vehicles
(
UTV
)
, and supplies some relevant technique and performance data. Some
techniques and method inside may be used to check, maintain and repair other models of
UTV, although it is mainly for HS1000UTV/HS900UTV/HS800UTV-5.
Please read the handbook through and fully understand it; otherwise, any improper
repairing and amounting would bring you problems, and accident may occur in your use.
Proper use and maintenance can guarantee UTV being driven safely, reduce its
malfunction, and help the vehicle remain its best performance.
The standards, performances and specifications mentioned in interpretation are
based on the sample in design, and they are subject to changes according to the
product’s improvement without prior notice.
First version ,October, 2014
Published by
Chongqing Huansong Science And Technology Industrial Co.,Ltd
Chongqing Huansong Science And Technology Industrial Co.,Ltd holds the copy right.
No publishing and reprinting without permission.