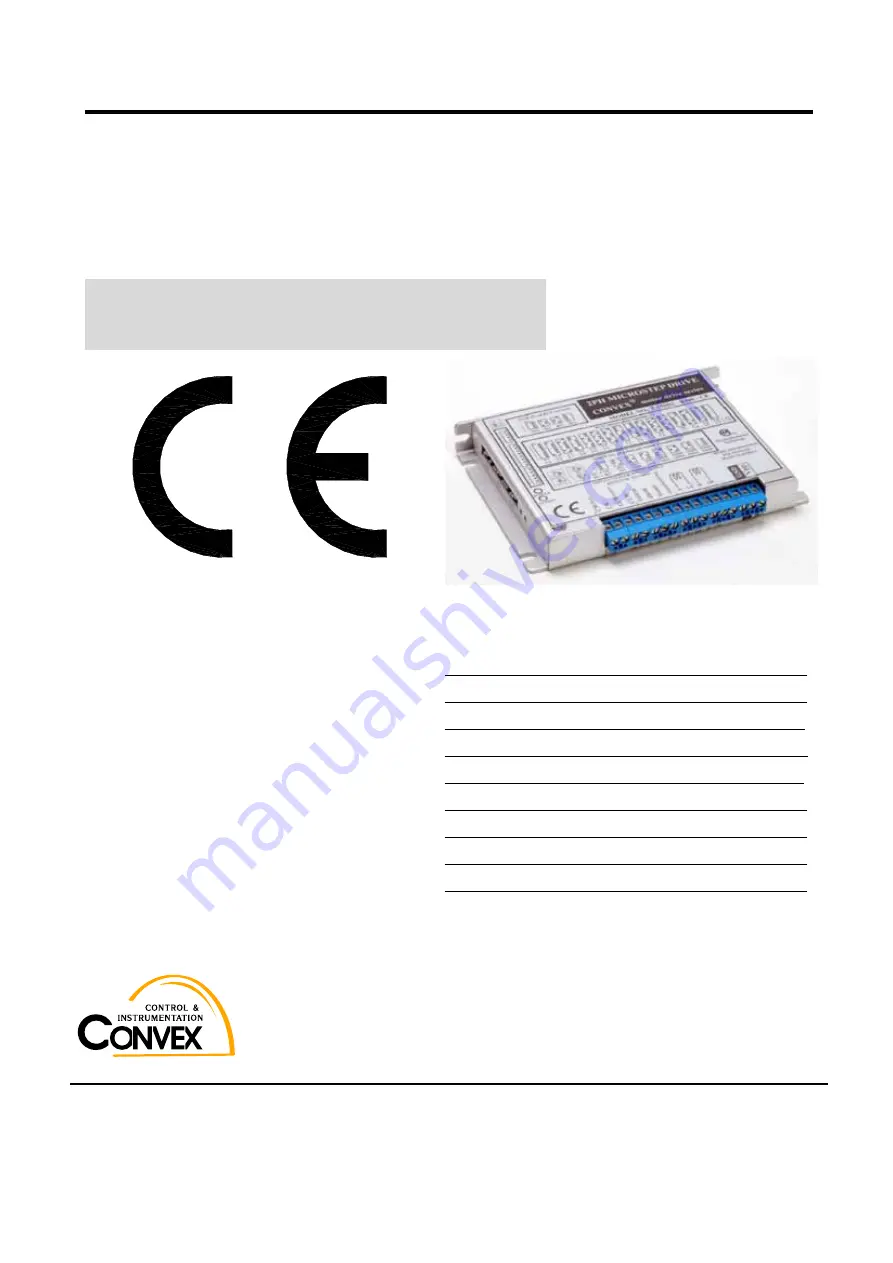
Manual no. CSMD2-440-CE-ENG-050124
CONVEX Microstep Driver FOR 2PH Step Motor
CSMD2 – U440
(UNIPOLAR DRIVE)
CSMD2 – B440
(BIPOLAR DRIVE)
USERS’ GUIDE
< CONTENTS >
1. Safety Cautions P.2
2. Unpacking and Inspection P.4
3. Driver Configuration P.4
4. Mounting P.6
5. Driver Current and Mode set P.8
6. Input Pulse Timing Chart P.11
7. Connection and Wiring P.13
8. Trouble Shooting P.17
9. Specifications P.19
Thank you for choosing the Convex Microstep Driver CSMD2 series.
Please read this manual carefully so that the equipment is used to its optimum.
A copy of this manual should be forwarded to the end user.