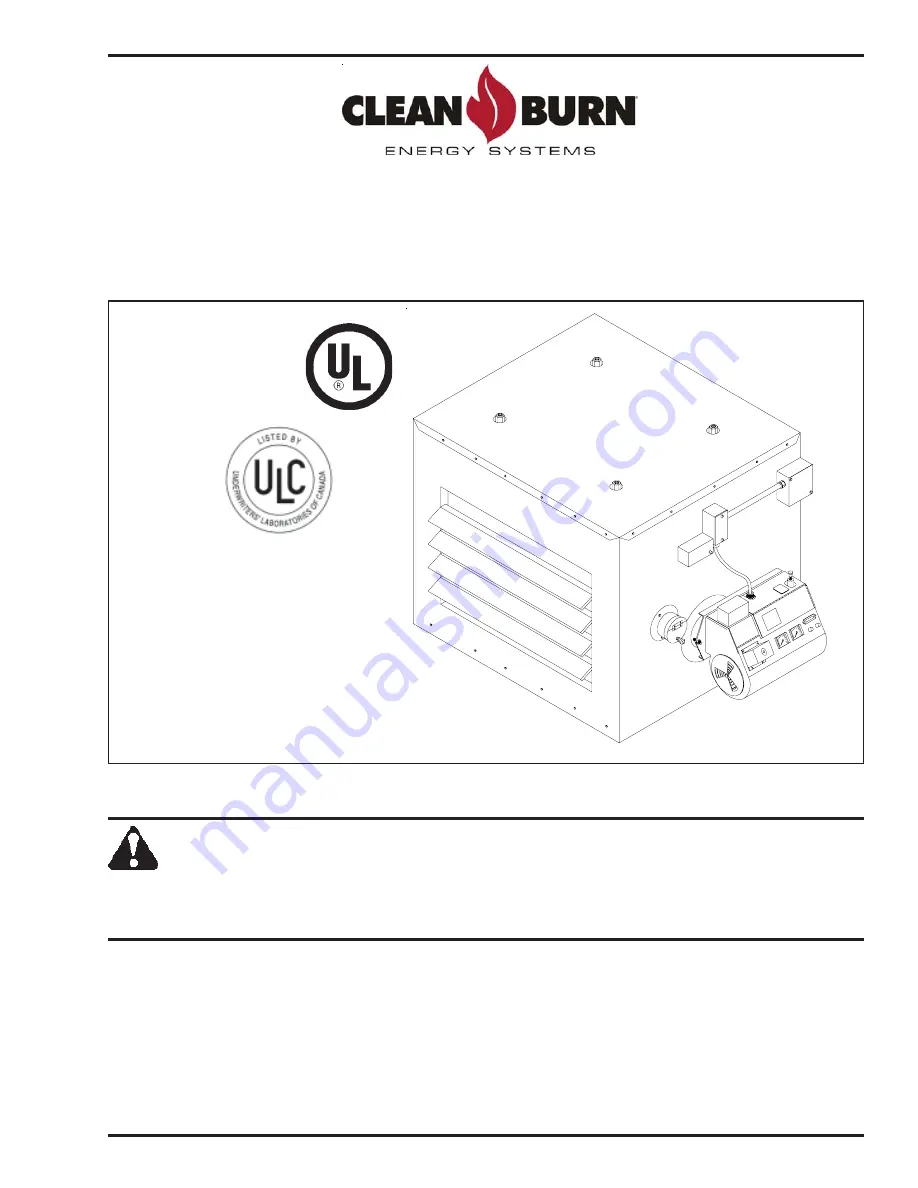
CLEAN BURN MODEL: CB-1400
MULTI-OIL FURNACE
with CB-525-S2 BURNER
IMPORTANT FOR U.S. INSTALLATIONS: All installations must be made in accordance with state and local codes
which may differ from the information provided in this manual. Save these instructions for reference.
IMPORTANT FOR CANADIAN INSTALLATIONS: These instructions have been reviewed and accepted by
Underwriters' Laboratories of Canada as being appropriate for the installation of the ULC labelled products
identified herein. The use of these instructions for the installation of products NOT bearing the ULC label and
NOT identified herein may result in an unacceptable or hazardous installation.
IMPORTANT FOR CANADIAN INSTALLATIONS: The installation of this equipment is to be accomplished by
qualified personnel and in accordance with the regulation of authorities having jurisdiction and CSA Standard B 139,
Installation Code for Oil Burning Equipment.
PUBLICATION DATE: 8/15/07, Rev. 3
CLEAN BURN PART # 43204
U.L. Listed Used Oil
Burning Appliance
#MH15393 (N)
U.L.-C Listed
#CMP217
WARNING: DO NOT assemble, install, operate, or maintain this equipment without first
reading and understanding the information provided in this manual. Installation and
service must be accomplished by qualified personnel. Failure to follow all safety precautions
and procedures as stated in this manual may result in property damage, serious personal injury
or death.
I88817
OPERATOR'S MANUAL
Summary of Contents for CB-1400
Page 2: ......
Page 8: ......
Page 18: ...Operator sManual ModelCB 1400 1 10 ...
Page 62: ...Operator sManual ModelCB 1400 5 8 ...
Page 68: ...Operator sManual ModelCB 1400 7 2 ...
Page 84: ...Operator sManual ModelCB 1400 9 10 ...
Page 92: ...Operator sManual ModelCB 1400 10 8 ...
Page 108: ...Operator sManual ModelCB 1400 C 2 ...