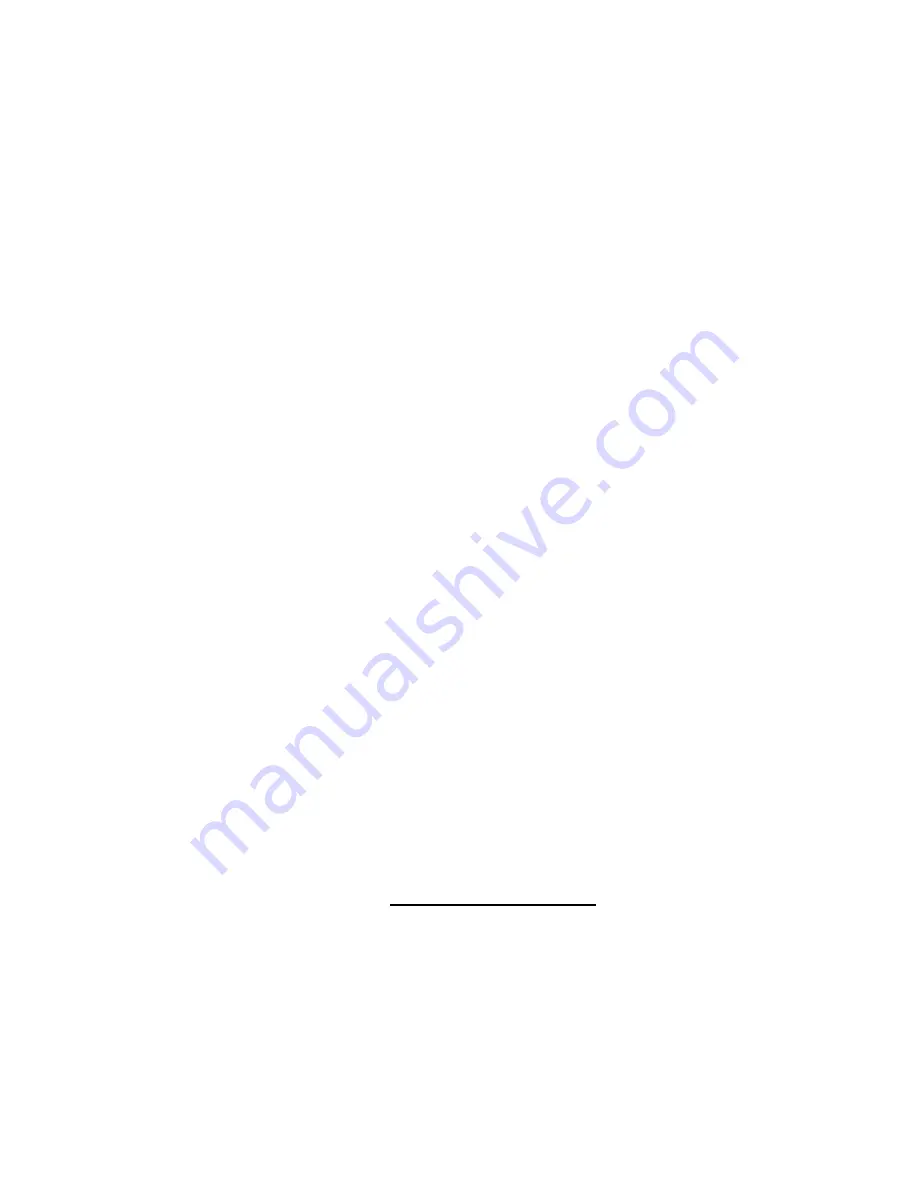
C136142 revH
11/18
Operation and Maintenance
Instructions Manual
ZE / ZF MODEL ENGINES
FOR
FIRE PUMP APPLICATIONS
Clarke UK, Ltd.
Clarke Fire Protection Products, Inc.
Unit 1, Grange Works
100 Progress Place
Lomond Road
Cincinnati, OH 45246
Coatbridge
U.S.A.
ML5 2NN
United Kingdom
TELE: +44(0)1236 429946
FAX: +44(0)1236 427274
TELE: +1.513.771.2200 Ext. 427
FAX: +1.513.771.5375
www.clarkefire.com