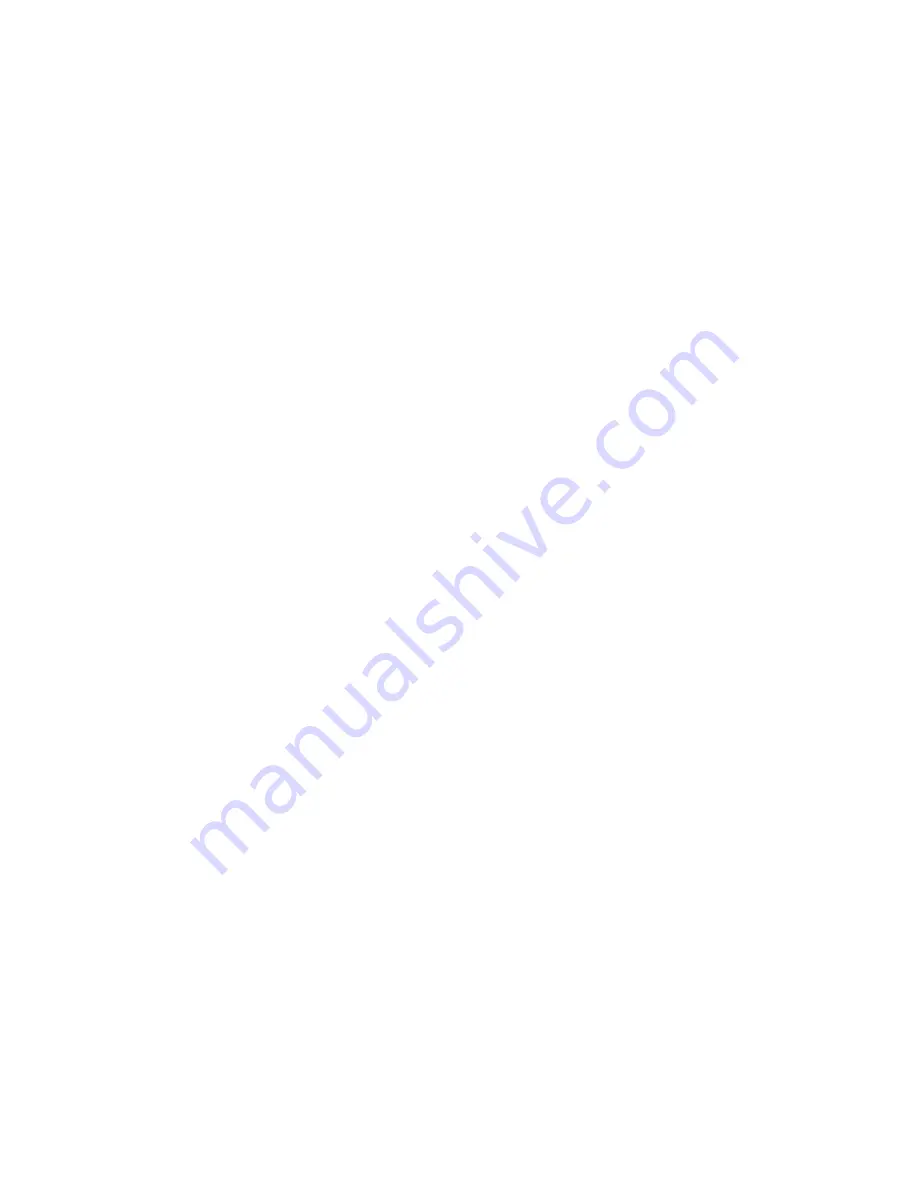
CHEMINSTRUMENTS
HOT MELT DRAWDOWN COATER
MODEL HLCL-1000
OPERATING INSTRUCTIONS
PRODUCT DESCRIPTION ..................................................................................................2
UNPACKING ........................................................................................................................2
ASSEMBLY ..........................................................................................................................2
Key Components ........................................................................................................3
DIAGRAM ............................................................................................................................4
DIAGRAM ............................................................................................................................5
ASSEMBLY ..........................................................................................................................7
OPERATION .........................................................................................................................8
Theory of Operation ...................................................................................................8
Power Up ...................................................................................................................8
Controller Operation ..................................................................................................8
Coating Operation .....................................................................................................10
MAINTENANCE ..................................................................................................................11
Cleaning .....................................................................................................................11
Troubleshooting .........................................................................................................12
Thermocouple Connections .......................................................................................12
Heating Rod Connections ..........................................................................................13
Replacing the Relay ...................................................................................................14
WARRANTY ........................................................................................................................15
1