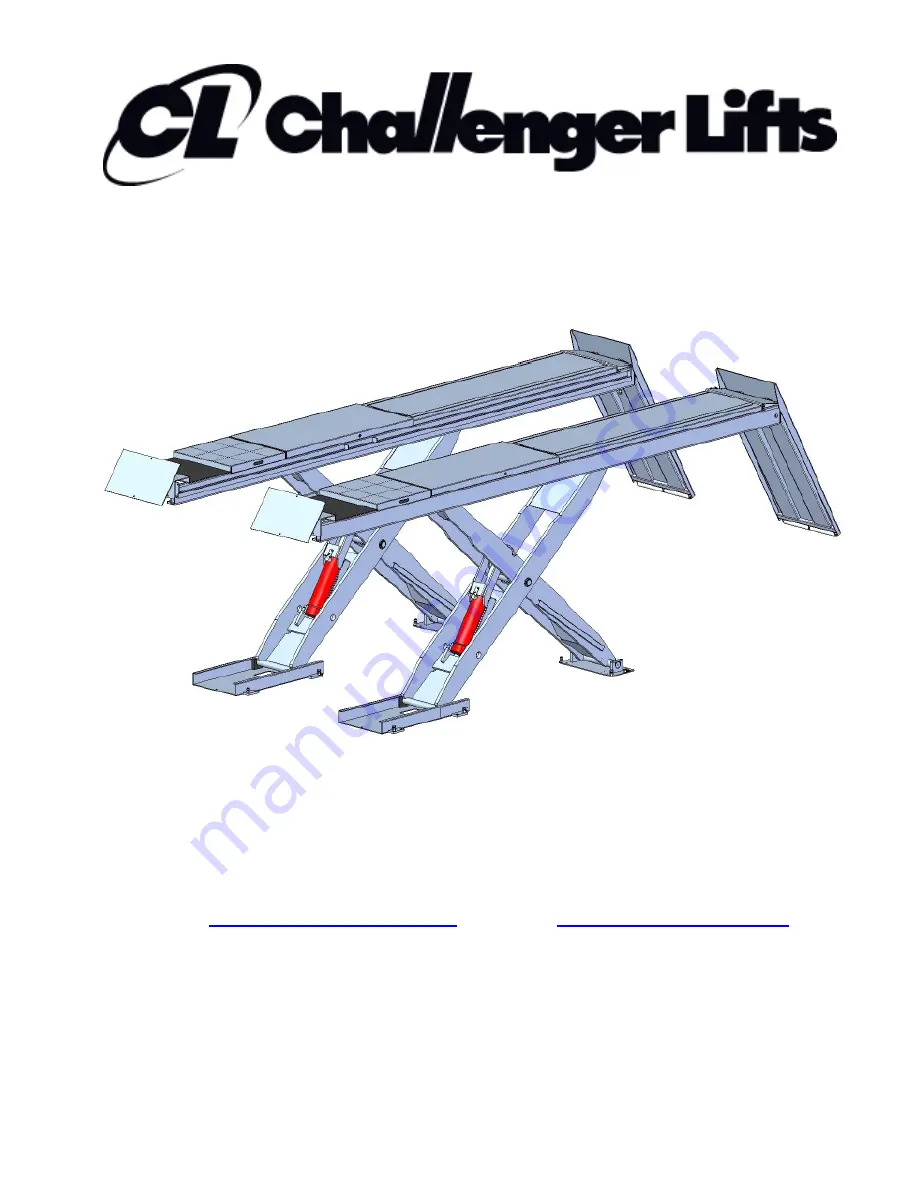
Rev. 1/9/20
Installation, Operation & Maintenance Manual
Scissor Alignment Lift
Model SX14 & SX14R
14,000 lbs. Capacity
7,000
LBS
.
PER
R
UNWAY
2311 South Park Rd Louisville, Kentucky 40219
Email:
Web site:
www.challengerlifts.com
Office: 800-648-5438 / 502-625-0700 Fax: 502-587-1933
IMPORTANT:
READ THIS MANUAL COMPLETELY BEFORE
INSTALLING or OPERATING LIFT
Summary of Contents for SX14
Page 4: ...4 LIFT BASE LAYOUT Fig 2 Base Layout PIT LAYOUT Fig 3 Pit Details...
Page 9: ...9...
Page 10: ...10 CONTROL UNIT 34 5 16 3 17 4 2 28 14 12 27 26 26 29 31 30 35...
Page 11: ...11 LABEL 2 LABEL 2A LABEL 3 LABEL 3A LABEL 4 LABEL 4A LABEL 5 LABEL 5A...
Page 12: ...12 LABEL 12 LABEL 14 LABEL 14A LABEL 16 LABEL 17...
Page 13: ...13 LABEL 22 LABEL 23 LABEL 25 LABEL 26 LABEL 27 LABEL 28 CHALLENGER SERIAL TAG LABEL 29...
Page 14: ...14 LABEL 30 LABEL 31 LABEL 34 LABEL 35 LABEL 35A...
Page 22: ...22 AIR SWITCH BASE SETTING...
Page 26: ...26 LUBRICATION POINTS repeat symmetrically on both sides of the lift...
Page 30: ...30 Fig 13 Electrical Wiring Diagram Console Lid Switches...
Page 31: ...31 Fig 13 Electrical Wiring Diagram Continued...
Page 32: ...32 Fig 14 Hydraulic Diagram...
Page 33: ...33 Fig 15 Pneumatic Diagram...
Page 34: ...34 PARTS BREAKDOWN 11 16 10 12 10 9 7 8 6 5 2 1 4 3 13 12 15 14...
Page 36: ...36 7 12 14 5 3 4 16 6 10 9 11 15 8 17 17 13 18 2 19 20 21 1 350 BAR 110 BAR...
Page 38: ...38 1 4 5 9 11 12 18 15 13 20 23 22 21 24 6 2 14 25 16 26 3 8 3 7 10...
Page 40: ...40 26 42 24 44 43 47 48 49 50 25 42 43 27 28 30 31 32 29...
Page 42: ...42...
Page 44: ...44 29 48 47 21...